Investment Casting Services
- We provide precision investment casting services that deliver near-net-shape parts with excellent dimensional accuracy and smooth surfaces.
- From design to final assembly, we offer complete, ready-to-use components tailored to your industry's performance and material needs.
- Dimensional Accuracy: ±0.1 mm -- ±2.0 mm
- Main Process Types: Silica Sol, Water Glass
- Compatible with Most Metals
- Supports Complex Part Designs
- No Flash or Parting Lines
- Environmentally Friendly Casting Process
Our Investment Casting Process
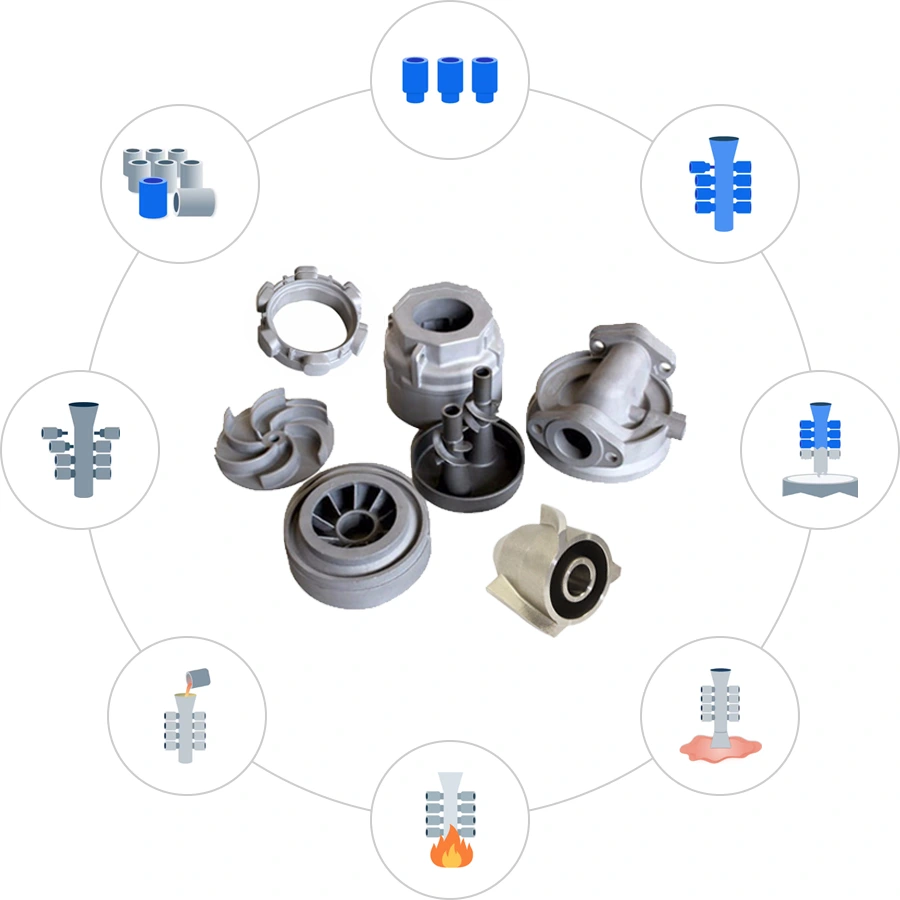
Wax Pattern Creation
Pattern Assembly
Shell Building
Wax Removal
Shell Firing
Metal Pouring
Shell Removal
Post-Casting Processing
Main Investment Casting Types
- Silica sol binder gives tight tolerance and smooth surfaces.
- Ideal for aerospace, medical, and precision industrial applications.
- Produces complex shapes, thin walls, and reduces post-processing.
- Water glass binder fits large, simple parts needing moderate precision.
- Common in automotive, agricultural, and machinery industries.
- Supports mass production of iron and low-alloy steel parts.
Available Materials
To satisfy your unique performance, corrosion resistance, and mechanical property needs, we provide a wide range of materials:
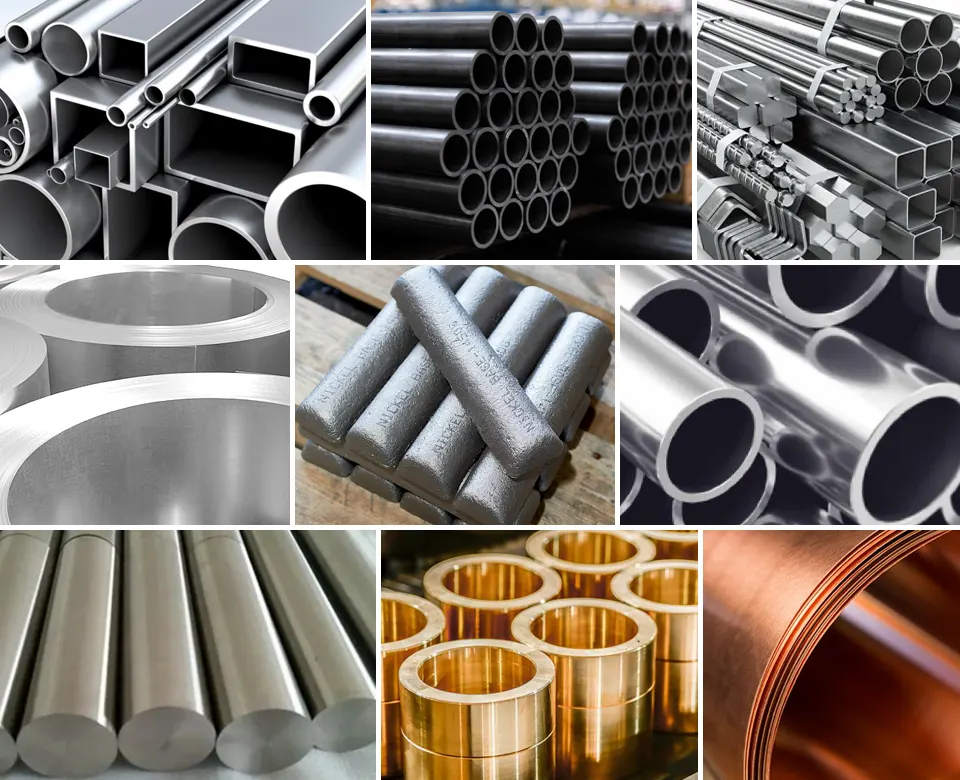
Stainless Steel
Carbon Steel
Alloy Steel
Nickel-Based Alloys
Cobalt-Based Alloys
Aluminum Alloys
Titanium Alloys
Bronze
Copper Alloys
Dimensions in Investment Casting
Parameter | Specification |
Max Casting Size | Up to 1200 mm (L) × 800 mm (W) × 600 mm (H) |
Min Casting Size | 5 mm × 5 mm × 5 mm |
Wall Thickness | 0.5 mm – 10 mm |
Tolerance Levels | ±0.05 mm – ±0.5 mm |
Hole Diameter | 0.5 mm – 50 mm |
Surface Roughness (Ra) | 0.8 – 3.2 µm |
Aspect Ratio | Up to 10:1 |
Tolerance for Investment Casting Services
We provide precise investment casting services with strict quality standards, ensuring accurate tolerances for your specific application needs.
Tolerance Parameter | Typical Range |
Dimensional Tolerance | ±0.1 mm to ±2.0 mm |
Wall Thickness Tolerance | ±0.3 mm to ±1.5 mm |
Geometric Tolerance | ±0.1 mm to ±1.5 mm |
Surface Finish (Ra) | Ra 0.8 to Ra 6.3 |
Casting Defects (Porosity) | ≤ 1.5% of total volume |
Roundness (Circularity) | ≤ 0.05 mm to ≤ 0.5 mm |
Flatness | ±0.2 mm to ±1.0 mm |
Parallelism | ±0.1 mm to ±0.5 mm |
Angle Tolerance | ±0.5° to ±3.0° |
Hole Positioning Tolerance | ±0.1 mm to ±0.5 mm |
Casting Shrinkage | 0.3% to 2.0% |
Metal Flow Control | ±0.5 mm to ±2.0 mm |
Radii and Fillets | ±0.1 mm to ±0.3 mm |
Core Shifting | ≤ 0.3 mm |
Internal Surface Finish (Ra) | Ra 1.6 to Ra 3.2 |
Corner Radius | ±0.2 mm to ±1.0 mm |
Thickness Variability | ±0.5 mm to ±1.5 mm |
Casting Alignment Tolerance | ±0.2 mm to ±1.0 mm |
Length and Width Tolerance | ±0.1 mm to ±2.0 mm |
Post-Casting Processing
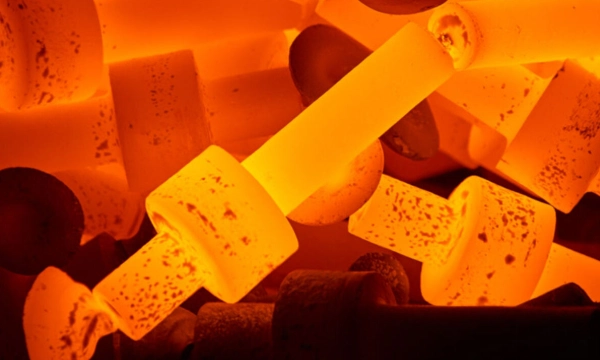
Heat Treatment
Performed in furnaces like annealing, quenching, tempering, and solution to enhance structure, hardness, and mechanical performance of castings.
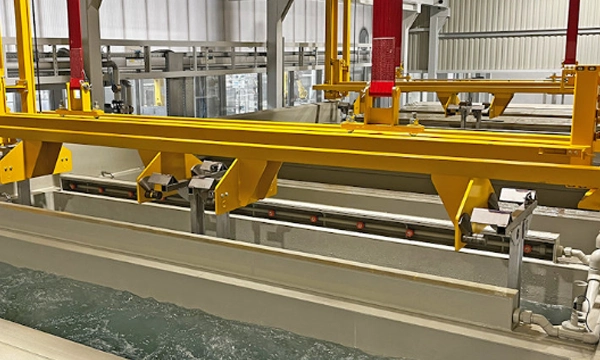
Surface Finishing
Includes shot/sand blasting, pickling, passivation, and alkali cleaning to remove oxide scales and improve stainless steel casting surfaces.
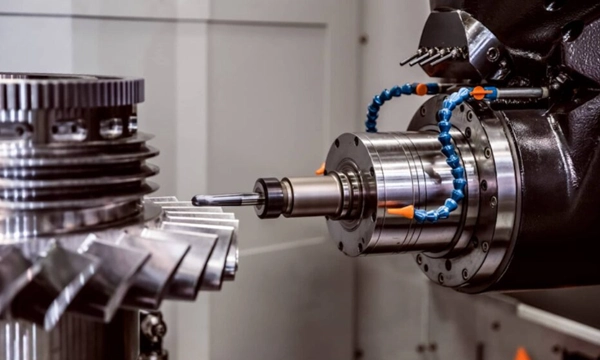
Machining
Utilizes CNC lathes, milling, and drilling to achieve required precision, tolerance, and surface finish for functional casting applications.
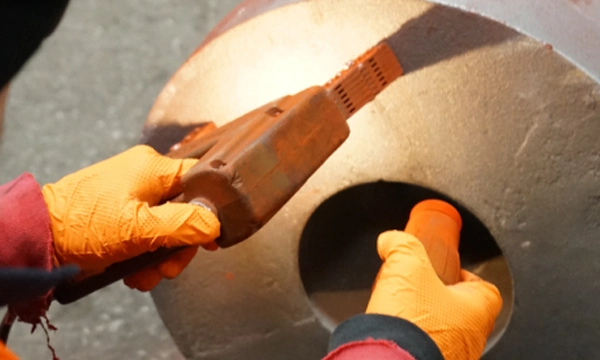
NDT Testing
Dye penetrant, ultrasonic, and X-ray testing detect internal or surface defects without damaging the casting’s structural integrity or appearance.
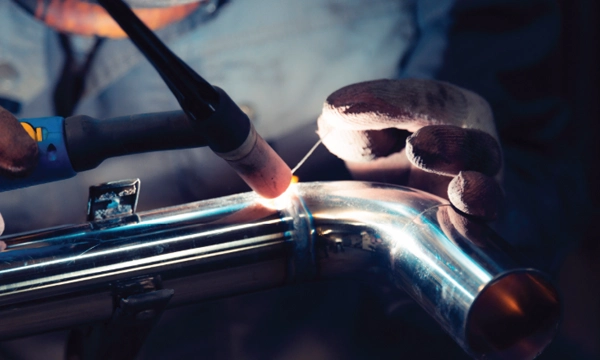
Welding
TIG welding is applied to repair minor casting defects within standards, ensuring reliable strength, surface integrity, and dimensional accuracy.
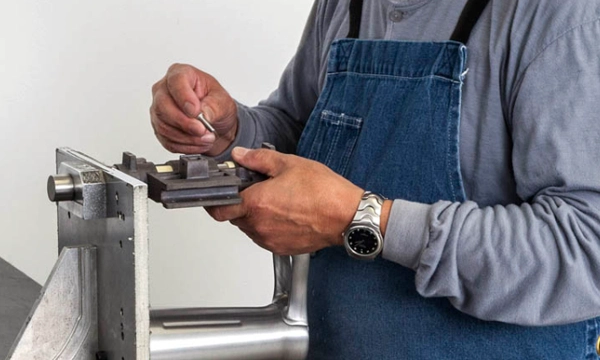
Assembly & Fitting
Components are fitted or assembled into complete units, ensuring compatibility, function, and readiness for final application or customer delivery.
Inspection Techniques
We implement rigorous inspection techniques to ensure casting accuracy, structural integrity, and compliance with material and performance standards.
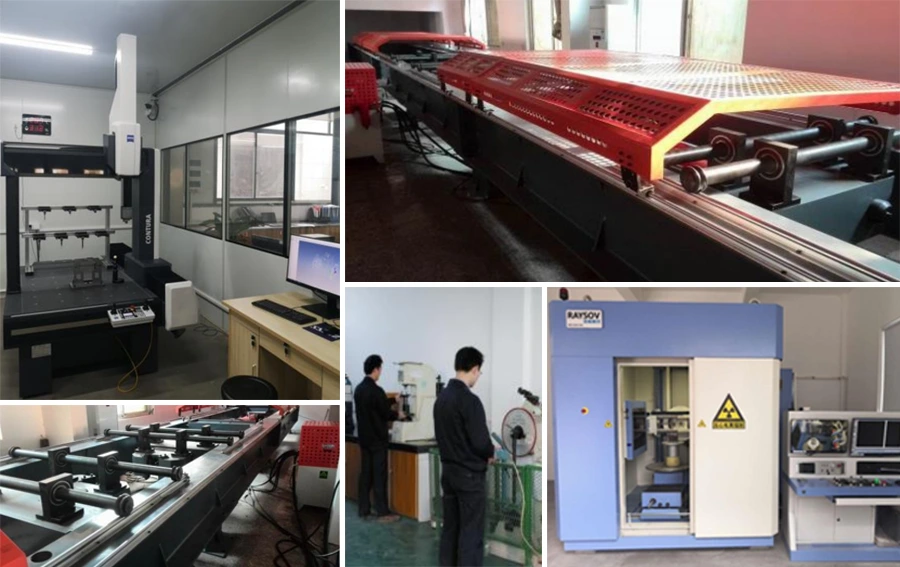
Dimension Inspection
Appearance Inspection
Internal Quality Inspection
Mechanical Properties Testing
Chemical Composition Analysis
Metallographic Analysis
Our Investment Casting Parts
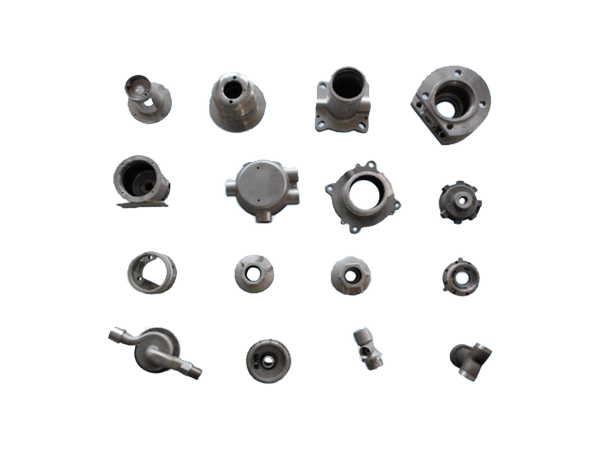
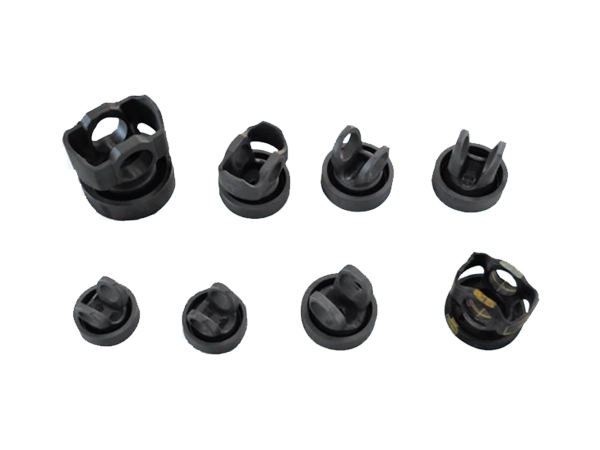
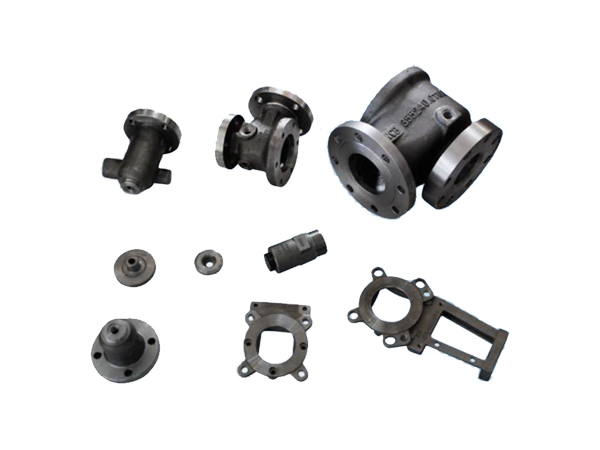
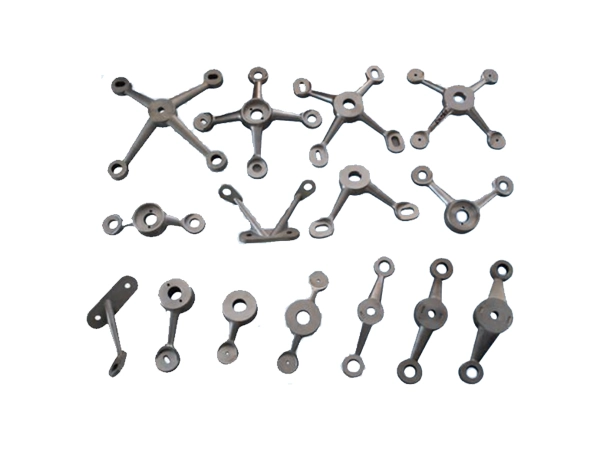
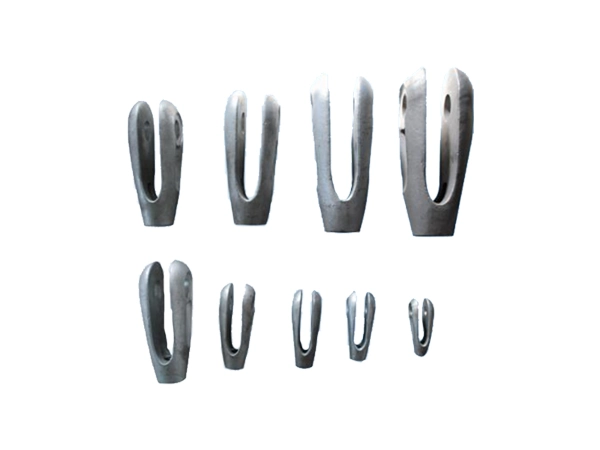
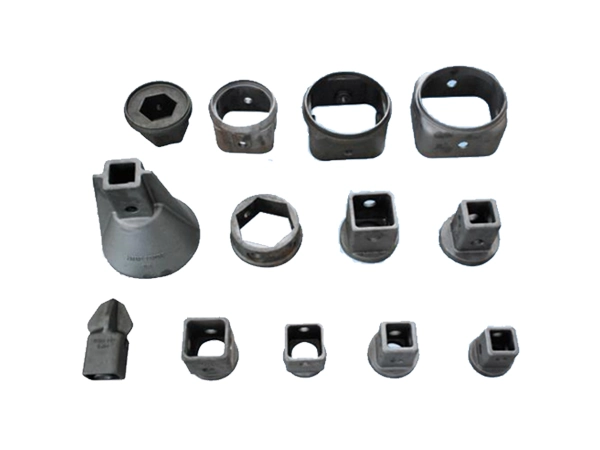
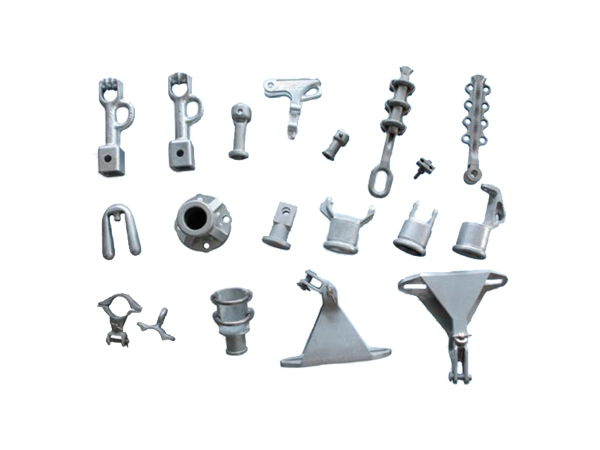
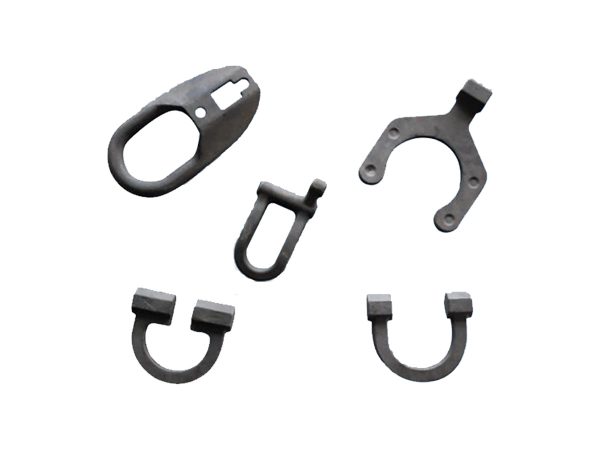
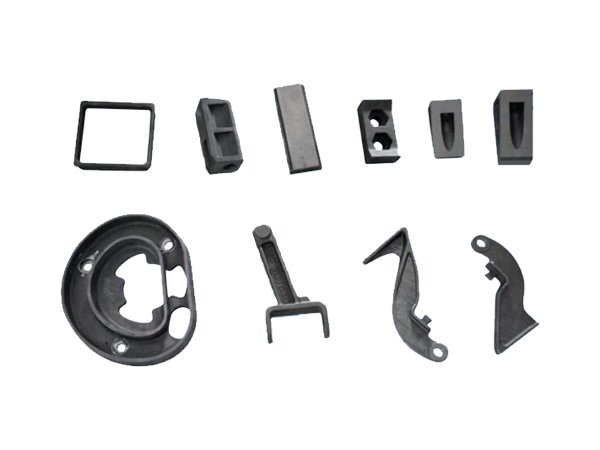
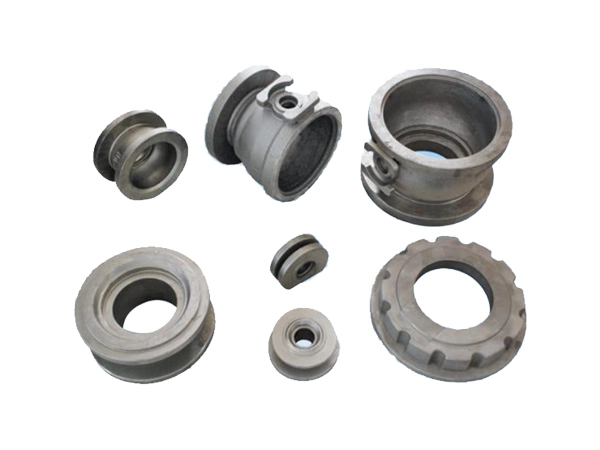
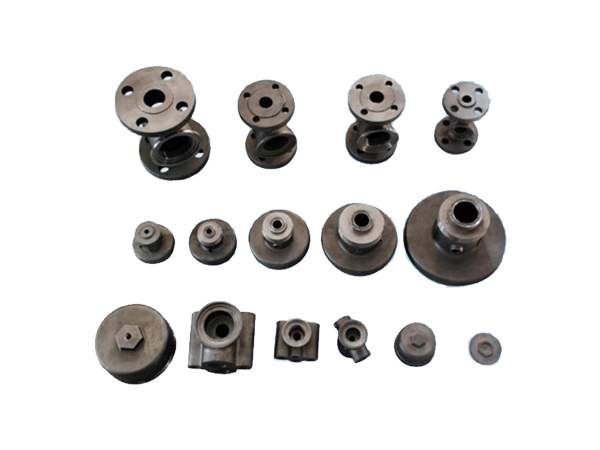
Applications
Our investment casting supports complex, high-performance parts across industries, offering precision, strength, and versatility in diverse critical applications.
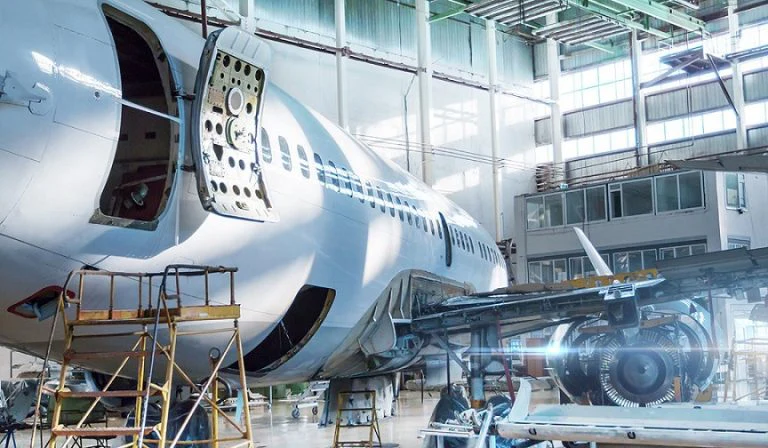
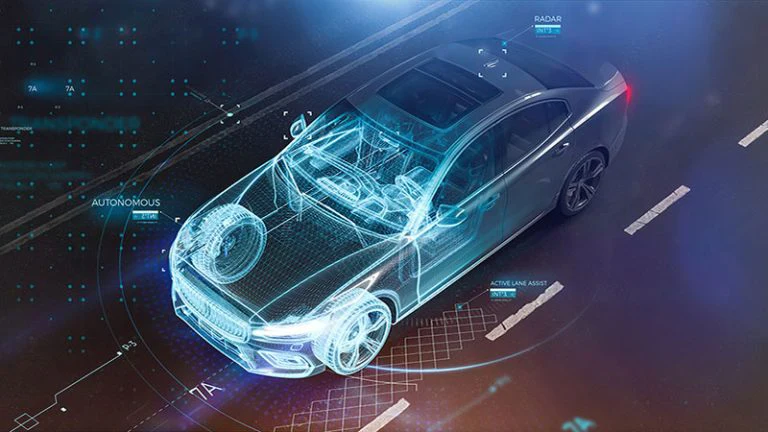
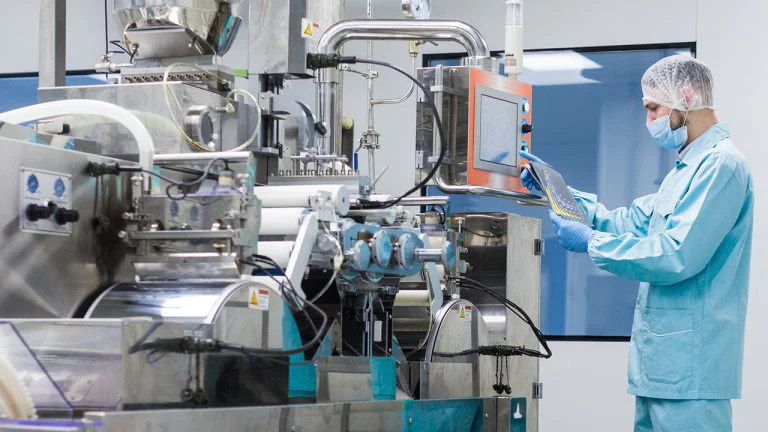
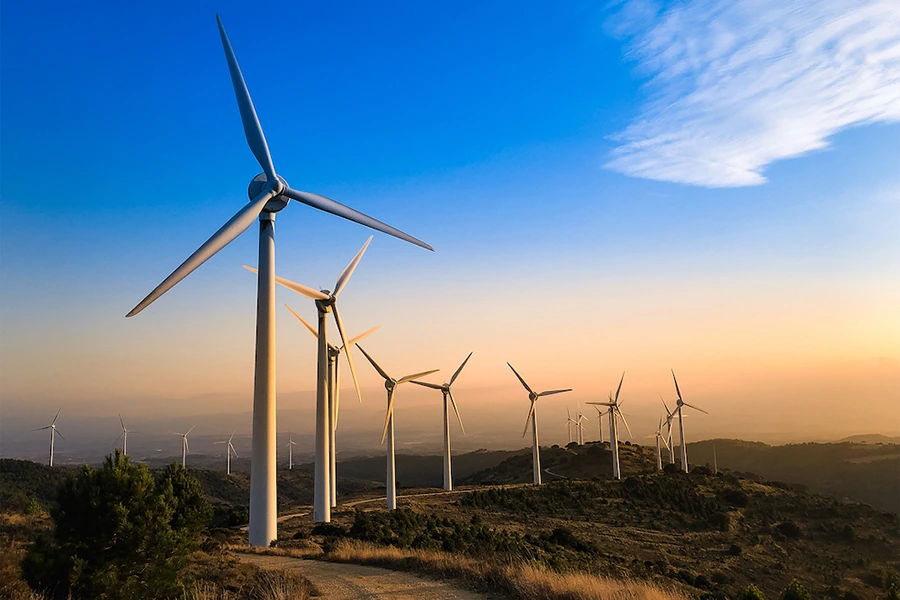
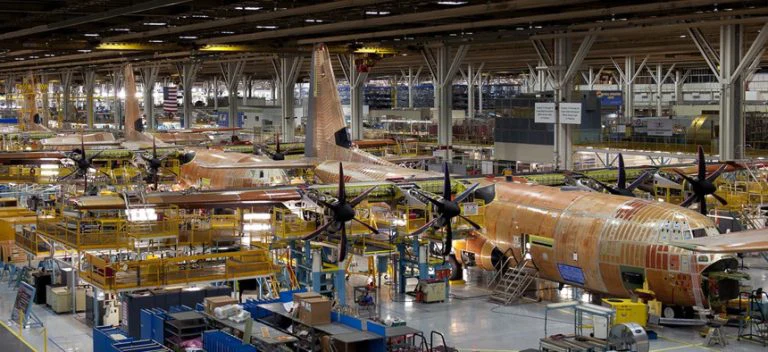
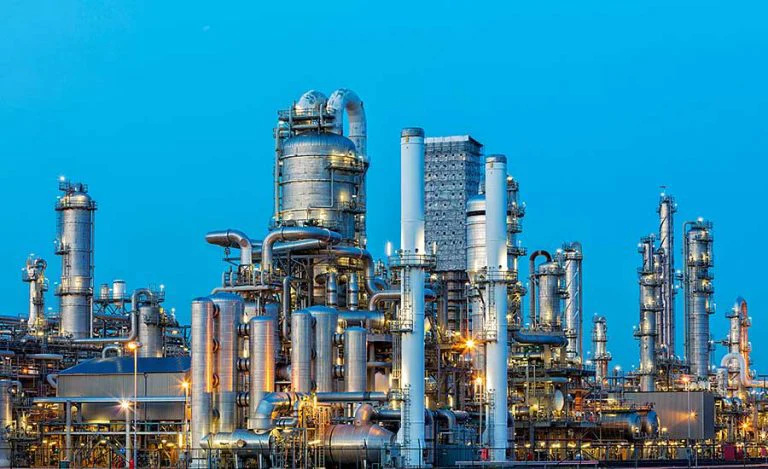
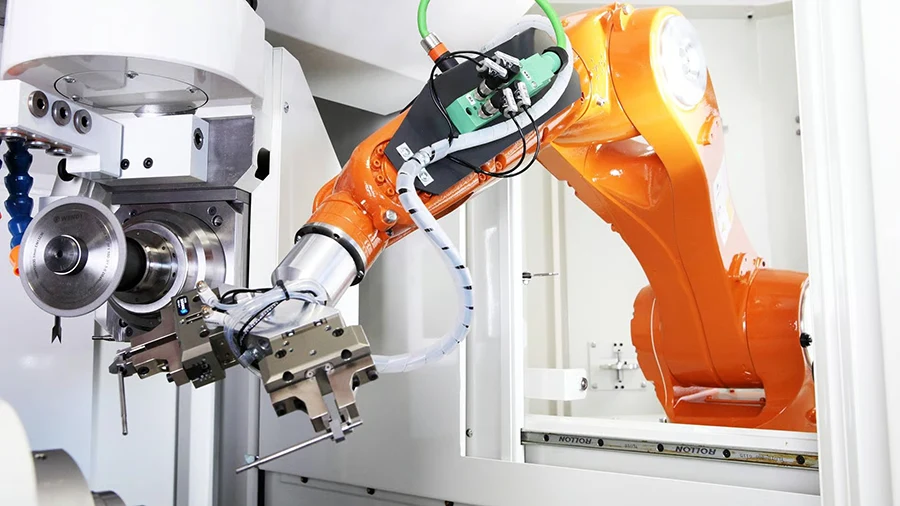
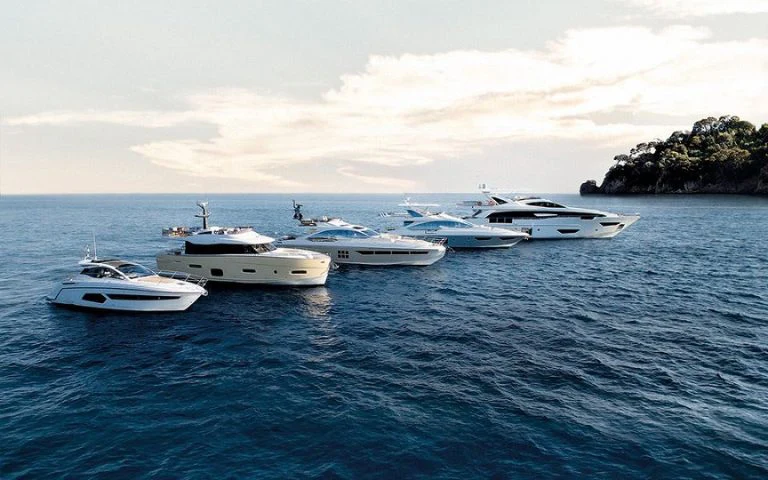
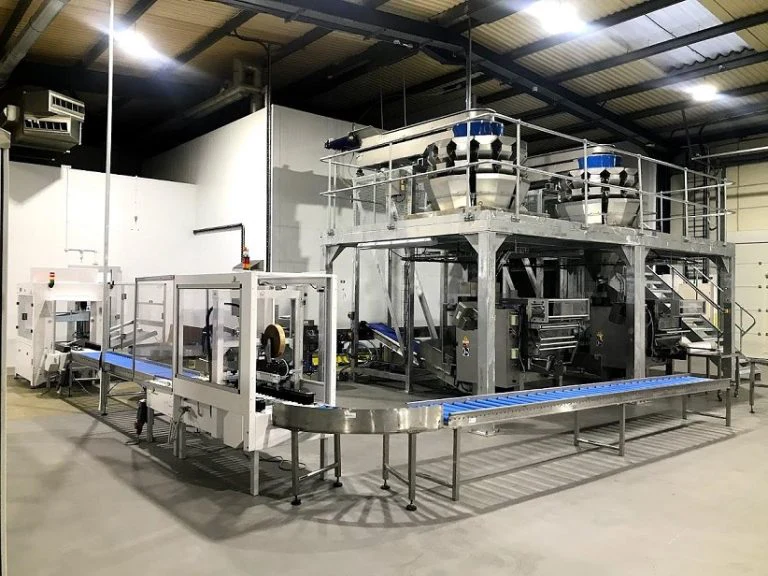
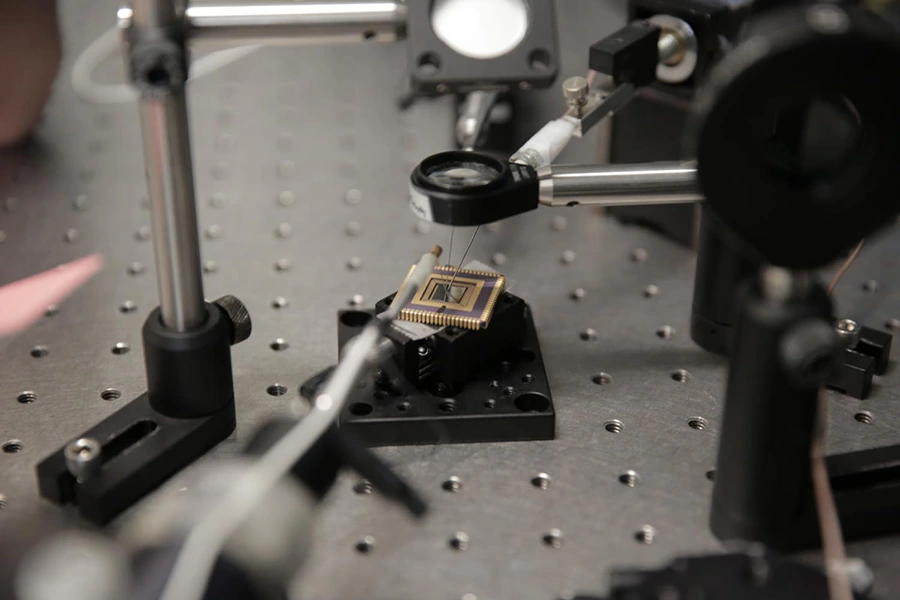