Upset Forging Services
- We specialize in upset forging to produce high-strength, precision-engineered components with complex geometries.
- Our advanced techniques improve material flow, boost strength, reduce waste, and deliver high performance and cost efficiency for demanding industrial applications.
- 30%+ increase in forming efficiency
- 15%-20% reduction in material resistance
- Grain size reduced to <5μm
- Ideal for complex components like deep blind hole shells
Our Upset Forging Process
From material selection to inspection, our upset forging process prioritizes quality to create precision, high-strength components.
Material Selection
We begin by selecting high-quality metal billets, ensuring the material is suited for the desired component strength.
Heating
Billets are heated to optimal temperatures, enhancing material ductility and enabling efficient deformation during the forging process.
Upsetting
After the billet is heated, it is put in a die and compressed with force to take on the required shape.
Shaping
Upset forging shapes the billet into specific dimensions, improving its mechanical properties by aligning the grain structure.
Finishing
The forged part undergoes finishing processes, including trimming, cleaning, and heat treatment, ensuring the component meets precise specifications.
Inspection
We conduct rigorous inspection, including dimensional checks and mechanical testing, ensuring each part adheres to our strict quality standards.
Main Upset Forging Types
Upset forging types include horizontal split-die and vertical closed-die processes, each tailored for different component specifications.
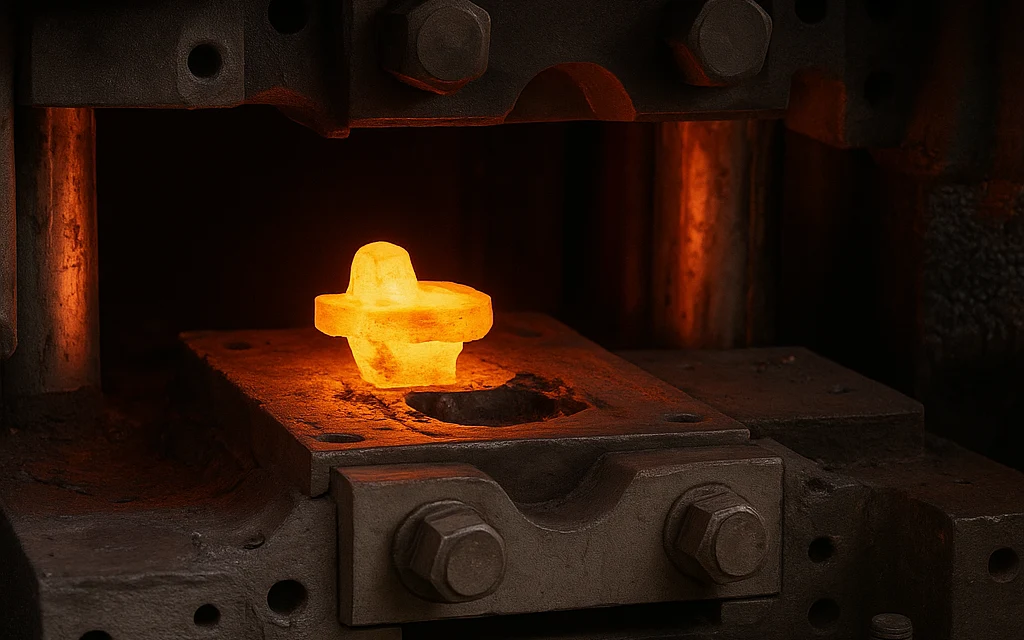
Horizontal Split-die Upset Forging
- Split-die tooling for horizontal deformation with even material distribution.
- Ideal for heavy components requiring precision and strength.
- Used for steel, aluminum, and titanium alloy parts.
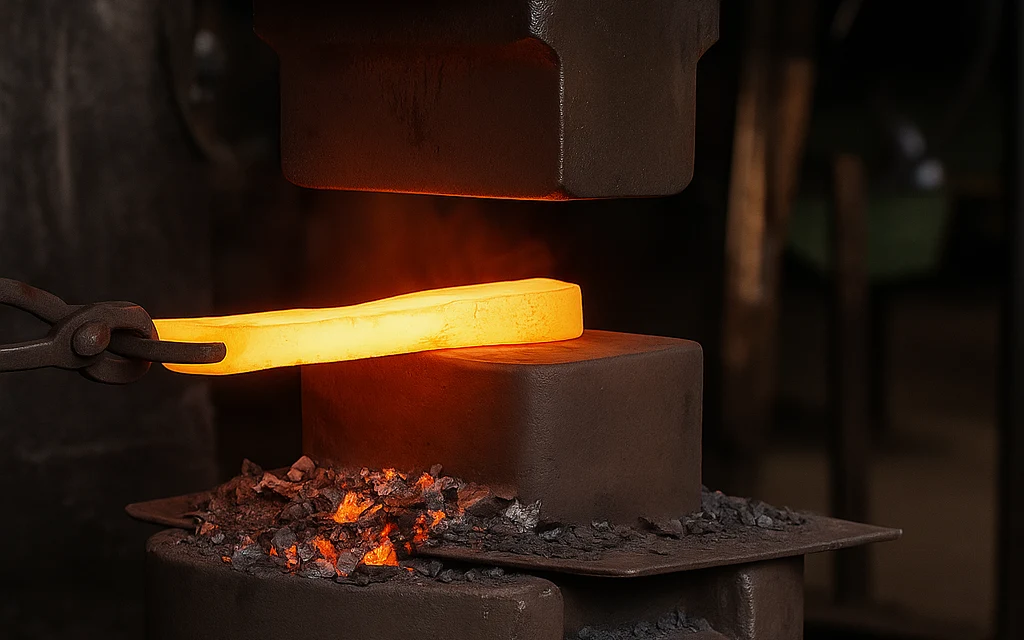
Vertical Closed-die Upset Forging
- Enclosed tooling for vertical deformation with high precision.
- Ideal for smaller, high-impact resistance parts in automotive, aerospace.
- Reduces material waste by controlling material flow.
Upset Forging Materials
We offer a wide range of premium metal materials for upset forgings, ensuring optimal strength, durability, and performance for both industrial and precision components.
Common Materials We Forge:
- Carbon Steel
- Stainless Steel
- Alloy Steel
- Aluminum Alloys
- Copper Alloys
- Titanium Alloys
- Nickel Alloys
- Magnesium Alloys
- Superalloys
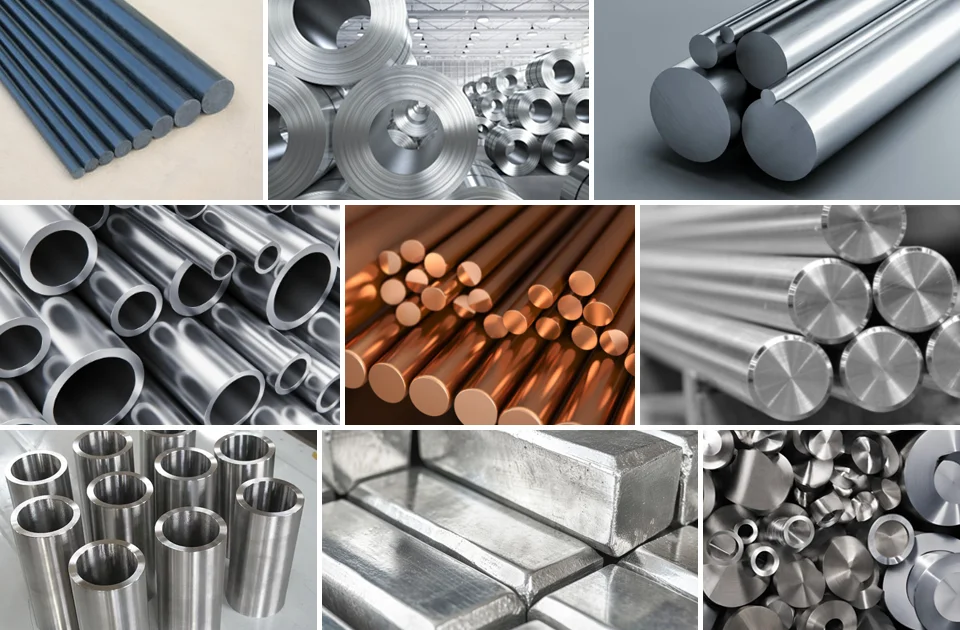
Tolerance for Upset Forging Services
We uphold rigorous standards in our upset forging processes to guarantee exceptional quality and performance. Below are the standard tolerances we provide:
Parameter | Tolerance Range |
Upset Length | ±0.1 mm to ±0.3 mm |
Upset Diameter | ±0.2 mm to ±0.5 mm |
Flow Line Orientation | ±5° from axial direction |
Flange Thickness | ±0.2 mm |
Forged Thread Tolerance | ISO 965-1 Class 6H |
Critical Diameter | ±0.1 mm to ±0.3 mm |
Hardness After Forging | 350-450 HB |
Decarburization Depth | ≤ 0.15 mm |
Barrel Distortion | ≤ 0.25 mm |
Die Wear Allowance | ±0.1 mm per 1000 parts |
Common Upset Forging Applications
Upset forging is essential for producing high-strength components across industries. Here are key applications where it ensures durability and performance:
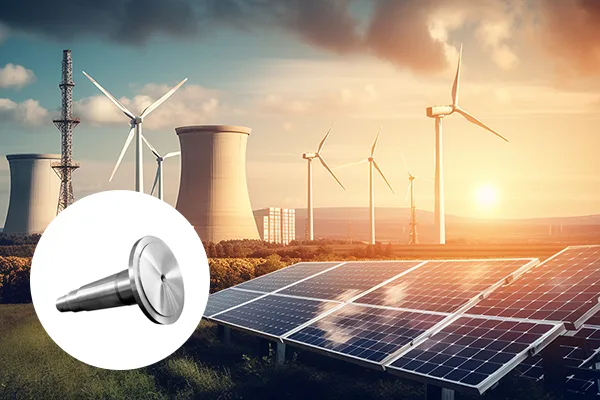
- Turbine rotors, generator main shafts
- Transformer cores and bushings
- Compressor and pump components
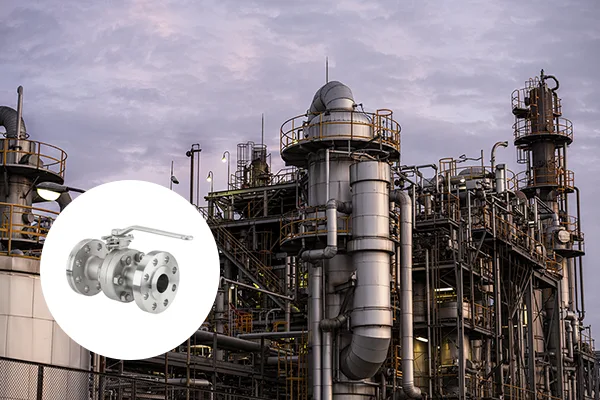
- Pressure vessel heads
- Pipeline connectors
- Valve bodies and flanges
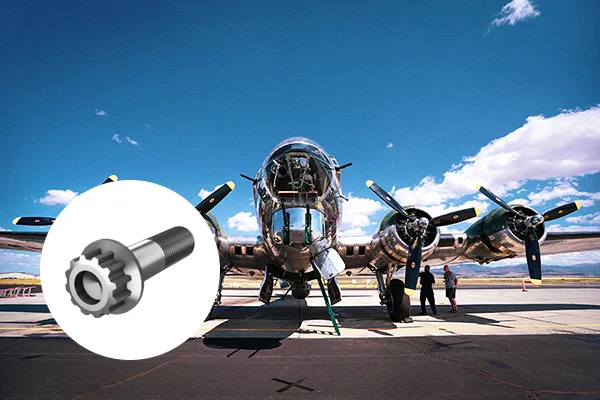
- Engine casings
- Landing gear parts
- Structural components for aircraft
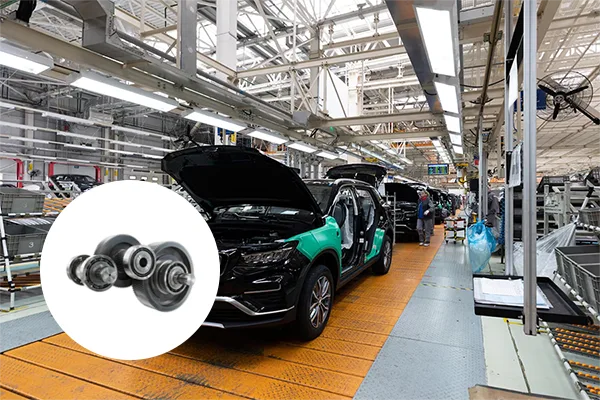
- Crankshafts, connecting rods
- Axles, gears, and bearings
- Wheel hubs and suspension components
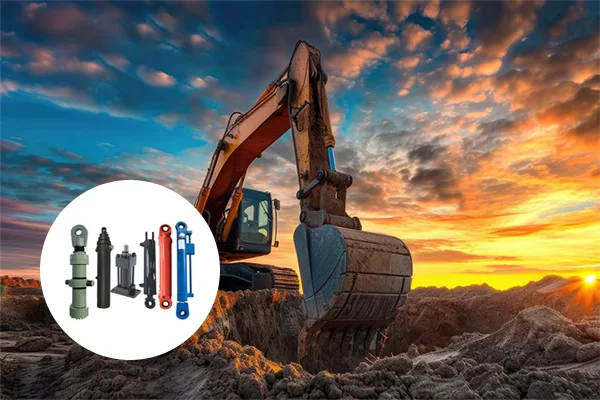
- Large gear blanks
- Hydraulic cylinders
- Heavy-duty shafts and pins
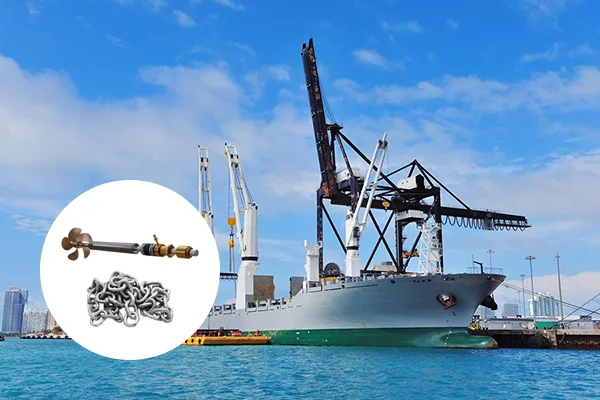
- Propeller shafts
- Anchor chains
- Turbine blades and housings
Contact Us Now
FAQs
Can upset forging reduce machining time?
Yes, upset forging reduces the need for additional machining by achieving near-final shapes with high accuracy.
What types of parts can be made with upset forging?
Upset forging can produce gears, shafts, fasteners, and other high-strength parts with complex geometries.
What is the typical tolerance achieved in upset forging?
Upset forging can achieve high dimensional accuracy, with tolerances as tight as ±0.1mm, depending on the part’s size and complexity.
How does upset forging differ from conventional forging?
Upset forging focuses on compressing the billet along its length, while traditional forging involves shaping the material through various methods.
Can upset forging be automated?
Yes, upset forging processes are often automated using hydraulic presses and robotic systems for consistent production.
Is upset forging suitable for low-volume production?
While upset forging is more efficient for high-volume runs, it can still be cost-effective for low-volume production depending on part complexity and requirements.