Drop Forging Services
- Our drop forging uses high-speed hammers to shape metal precisely, ensuring tight tolerances and excellent mechanical properties.
- It improves grain alignment, boosts impact resistance, and minimizes machining, ideal for complex, high-strength parts in cost-effective, large-scale production.
- Flexible Design Solutions
- Wide Material Selection
- Up to 25% Stronger Components
- Up to 20% Less Material Waste
- Suitable for Small & Medium Batches
Our Drop Forging Process
Raw Material Selection
We source high-quality metal billets or bars tailored to required mechanical properties and chemical composition.
01
Cutting and Heating
The material is cut to length and uniformly heated to forging temperature, ensuring plasticity and structural integrity.
02
Die Preparation
Precision-machined forging dies are prepared and aligned to ensure accurate shaping and repeatability for each forging cycle.
03
Drop Forging Operation
A heated billet is placed in the die, then repeatedly struck by a drop hammer or press to form the desired shape.
04
Trimming and Flash Removal
Excess material (flash) is trimmed from the forged part using a secondary die or trimming press.
05
Heat Treatment (Optional)
Parts may undergo quenching, tempering, or annealing to enhance strength, hardness, and fatigue resistance based on application.
06
Surface Cleaning
Forgings are cleaned using shot blasting or pickling to remove scale, improve appearance, and prepare for further processing.
07
Machining and Finishing
Critical dimensions are CNC machined, and additional finishing processes are applied for precision and surface quality.
08
Main Drop Forging Types
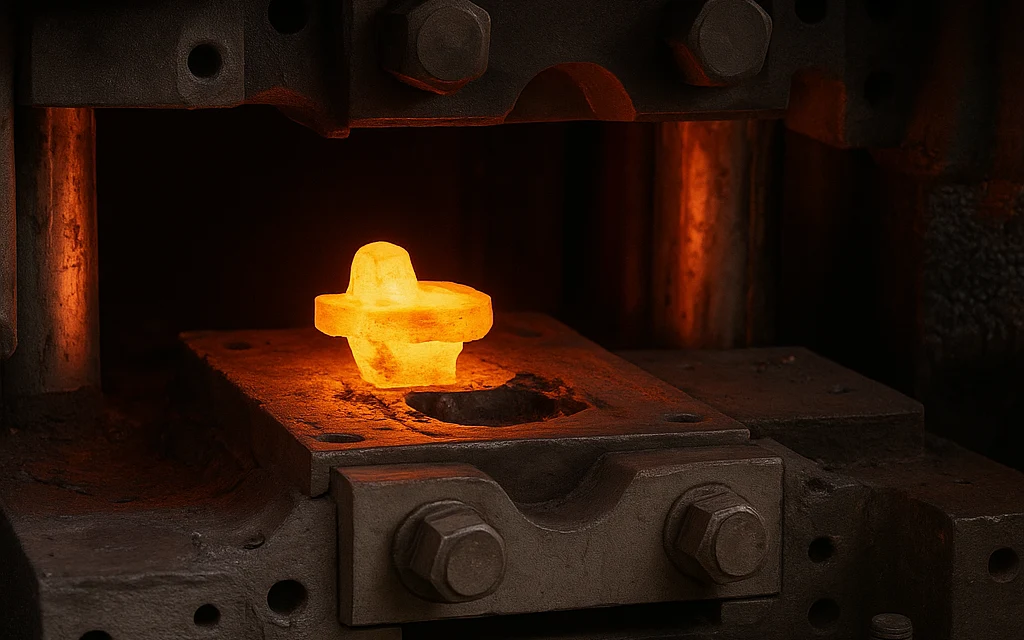
Closed Die Drop Forging
- Metal is compressed in shaped dies to form precise, near-net parts.
- Best for high-volume production needing tight tolerances and part consistency.
- Common in automotive, aerospace, and industries requiring complex, strong components.
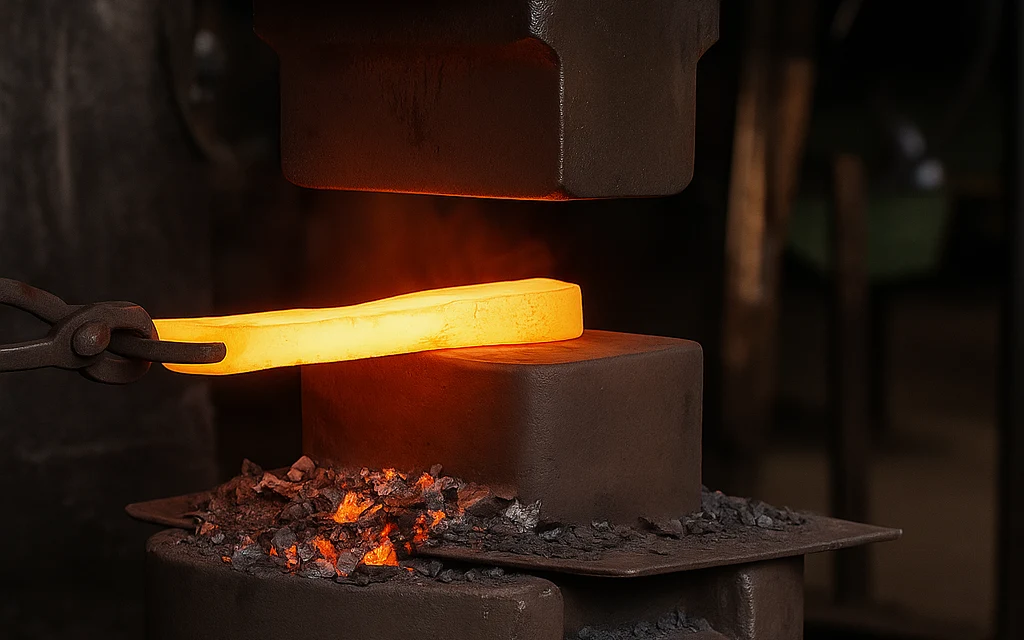
Open Die Drop Forging
- Heated metal is shaped with repeated blows between flat or contoured dies.
- Ideal for large parts needing strength and controlled grain structure.
- More shape flexibility, but requires machining for final dimensions.
Drop Forging Materials
We use high-performance metals to produce drop forged parts that meet mechanical and environmental requirements. Materials are selected for strength, wear, corrosion, and forgeability.
Common Materials We Forge:
- Carbon Steel
- Alloy Steel
- Stainless Steel
- Aluminum Alloys
- Titanium Alloys
- Nickel Alloys
- Copper Alloys
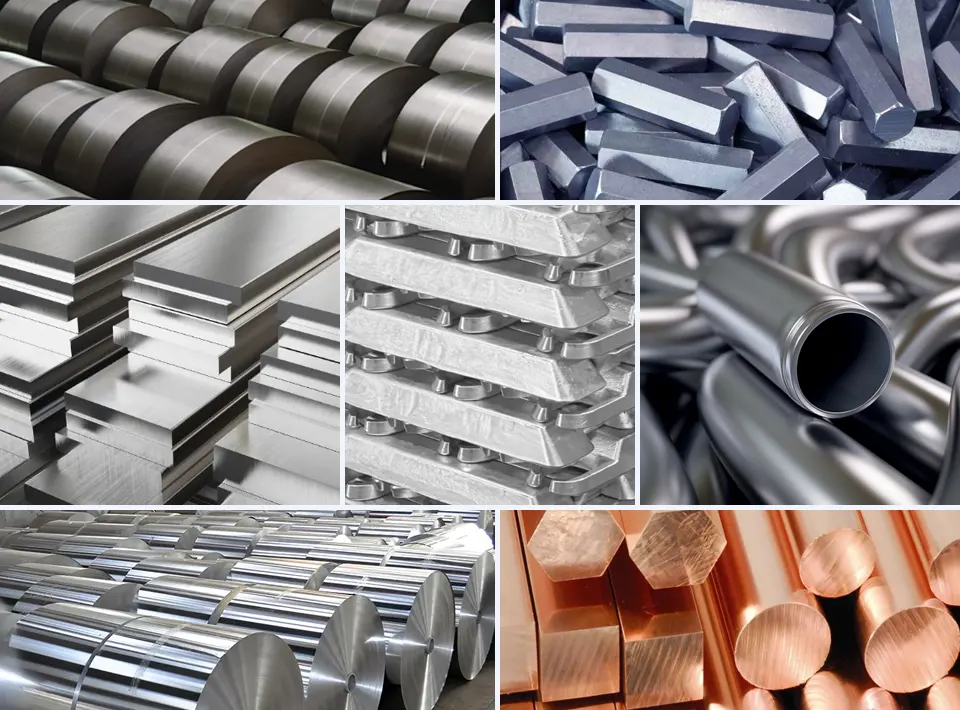
Tolerance for Drop Forging Services
Parameter | Tolerance Range |
Grain Flow Alignment | ±15° to ±30° |
Hardness | ±5 HRC (Rockwell) |
Section Size | ±0.2 mm to ±3.0 mm |
Corner Radius | ±0.2 mm to ±1.5 mm |
Surface Finish (Forged) | Ra 1.6 to Ra 3.2 µm |
Dimensional Accuracy of Holes | ±0.1 mm to ±0.3 mm |
Shaft Runout | ≤0.05 mm |
Flatness of Forged Plate | ≤0.3 mm per 100 mm |
Forged Part Length Deviation | ±0.3 mm to ±1.0 mm |
Forging Temperature | ±10°C to ±30°C |
Forge Closure Pressure | ±5% |
Strain Hardening | ±10% |
Our Drop Forged Parts
For a variety of industries, we create precision, strength, and longevity in our drop forged components. Their dependability is seen in demanding automotive and aerospace applications.
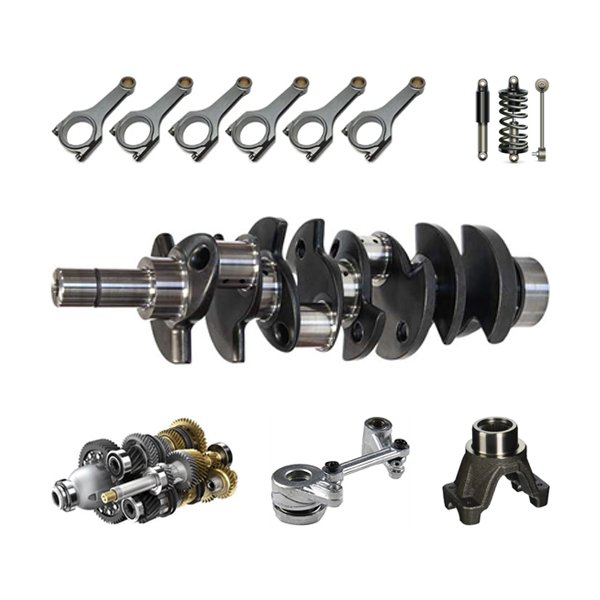
Automotive Parts
- Crankshafts
- Connecting Rods
- Suspension Components
- Steering Components
- Axles and Yokes
- Transmission Gears
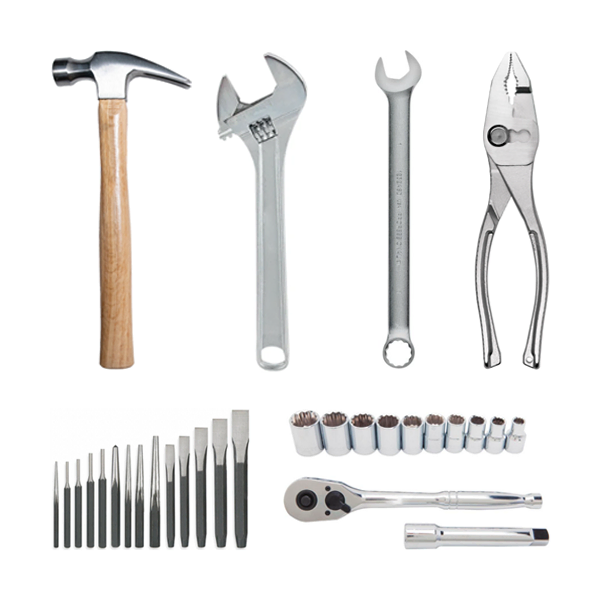
Tools and Hardware
- Hammers
- Wrenches
- Pliers
- Spanners and Sockets
- Chisels and Punches
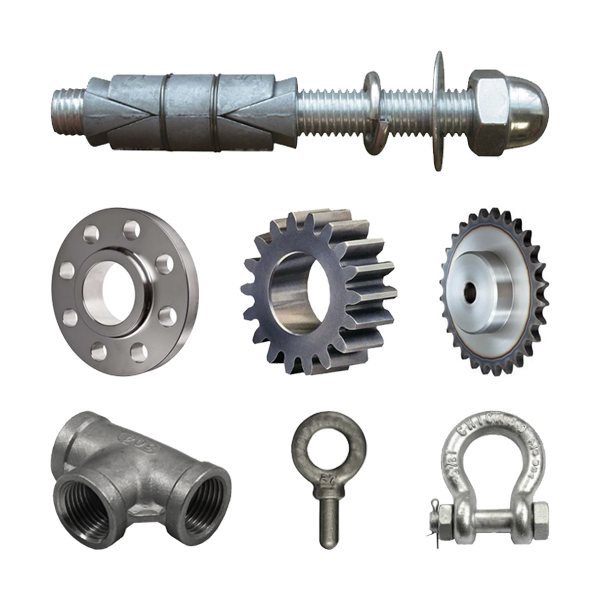
Construction and Industrial Equipment
- Shackles and Hooks
- Sprockets and Gears
- Flanges and Fittings
- Lifting Eyes and Eye Bolts
- Anchor Bolts and Brackets
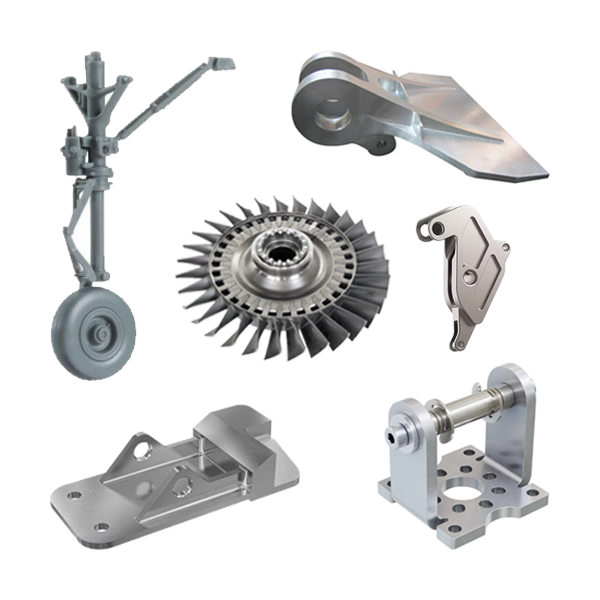
Aerospace Components
- Jet Engine Parts
- Landing Gear Components
- Wing Fittings
- Actuator Mounts
- Structural Brackets