Custom Forged Rolled Rings
- We produce high-precision forged rolled rings tailored to demanding applications like nuclear power and industrial machinery.
- With advanced technology and export experience, our rings ensure strength, corrosion resistance, and dimensional stability, saving time, labor, and cost in your critical operations.
- 18+ Years of Forging Expertise
- Custom Sizes and Materials Available
- ISO9001-certified Quality Assurance
- PED & AD2000 Compliance Guaranteed
Available Materials
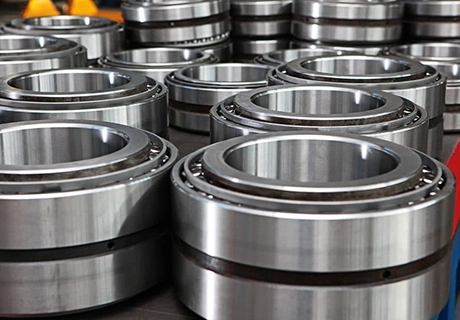
Carbon Steel Rolled Rings
Durable and cost-effective, ideal for structural and pressure vessel applications requiring strength, machinability, and moderate corrosion resistance.
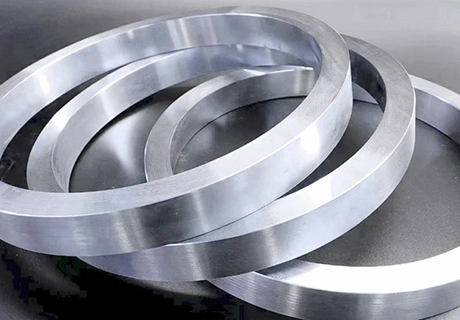
Alloy Steel Rolled Rings
Engineered for high strength, wear resistance, and toughness under extreme conditions, perfect for gears, bearings, and heavy-duty industrial components.

Stainless Steel Rolled Rings
Resistant to corrosion and oxidation, suitable for sanitary, marine, and high-temperature environments requiring strength and aesthetic finish.
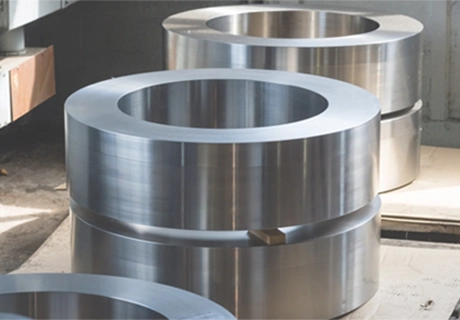
Tool Steel Rolled Rings
High hardness and wear resistance, designed for dies, cutting tools, and applications needing dimensional stability under thermal stress.
Shape Options
To meet a variety of structural and performance application requirements, we provide flat, tapered, contour, rectangular, and hollow forged rolling rings.
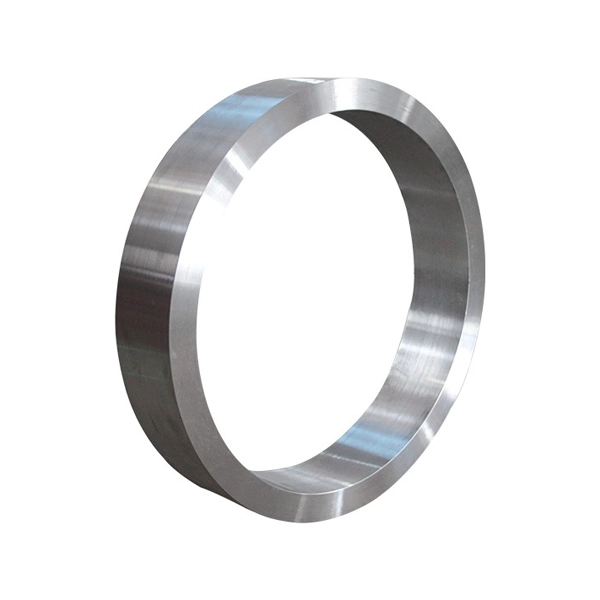
Flat Rolled Rings
- Uniform cross-section, ideal for bearings, flanges, and rotating parts.
- High accuracy and strength under axial and radial loads.
- Used in aerospace, construction, and automotive industries.
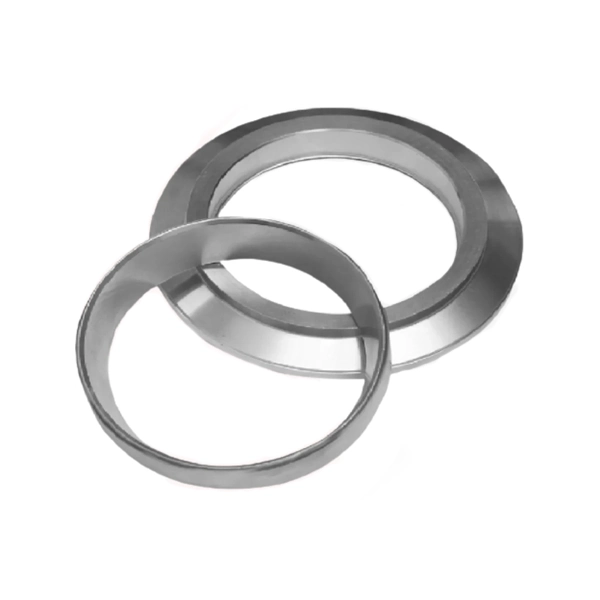
Tapered Rolled Rings
- Angled walls fit tapered components in high-stress systems.
- Reduces weight while ensuring structural integrity and alignment.
- Used in turbines, couplings, and transmissions.
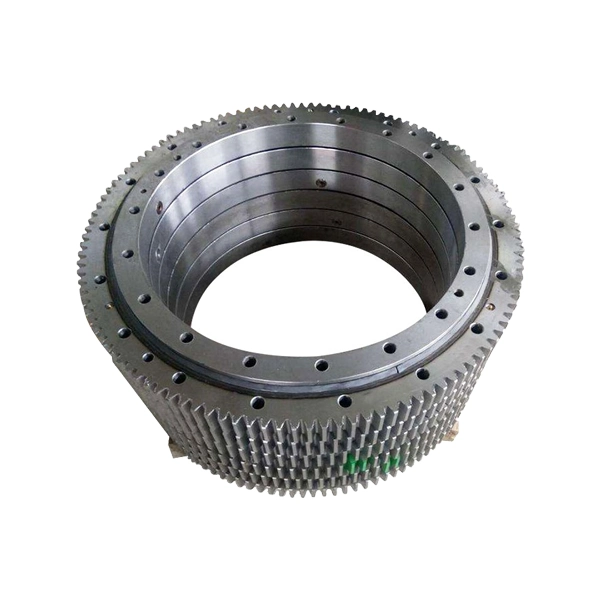
Contour Rolled Rings (Profiled Rolled Rings)
- Forged with complex profiles, reducing post-machining.
- Ideal for gear blanks, races, and stepped parts.
- Applied in energy, transport, and defense industries.
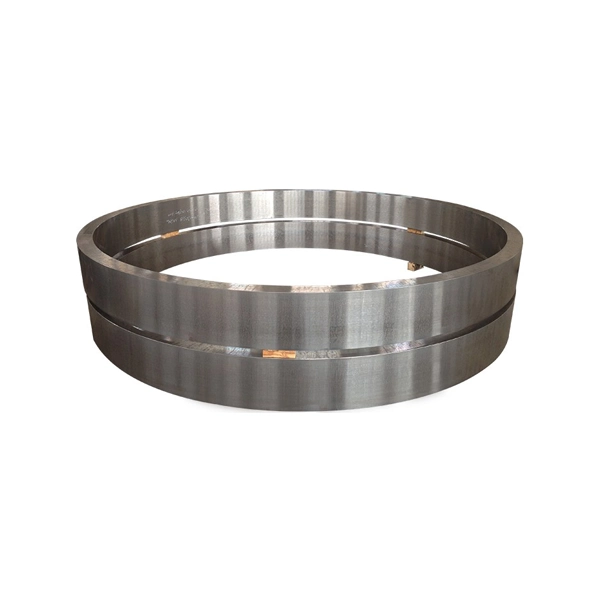
Rectangular Rolled Rings
- Square edges provide uniform load distribution.
- Common in hydraulic cylinders and precision housings.
- Offers strength and face alignment in static systems.
Our Forged Rolling Rings Production Process
We implement a precise forging and ring-rolling process to manufacture seamless, high-strength rings with exceptional dimensional accuracy and mechanical performance.
Material Cutting & Piercing
Billet Heating
Upsetting
Piercing to Donut Shape
Ring Rolling
Wall Thickness Adjustment
Cooling & Visual Inspection
Finish Machining
Final Inspection & Packaging
Applications
Our forged rolled rings are used in marine, defense, energy, mining, and petrochemical industries for strength, stability, and durability.
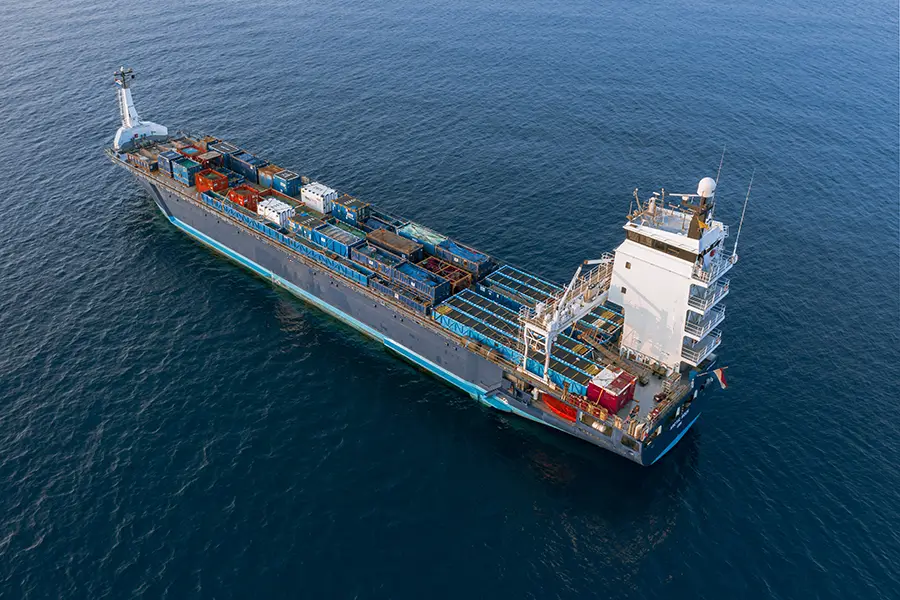
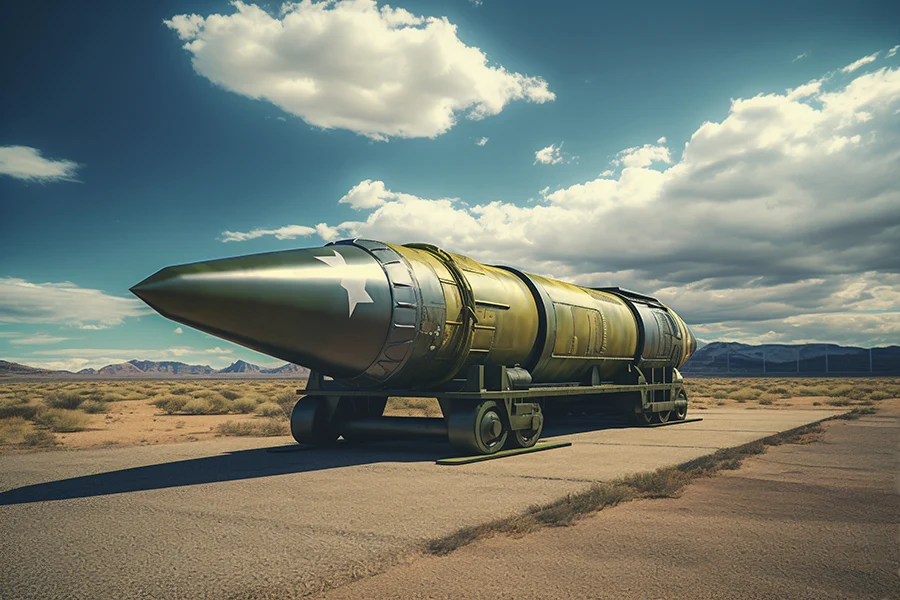
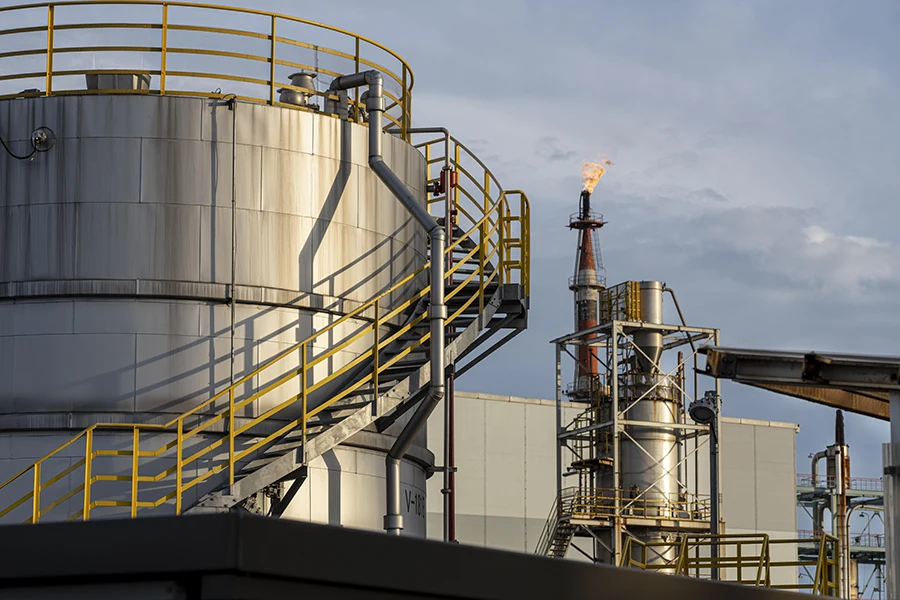
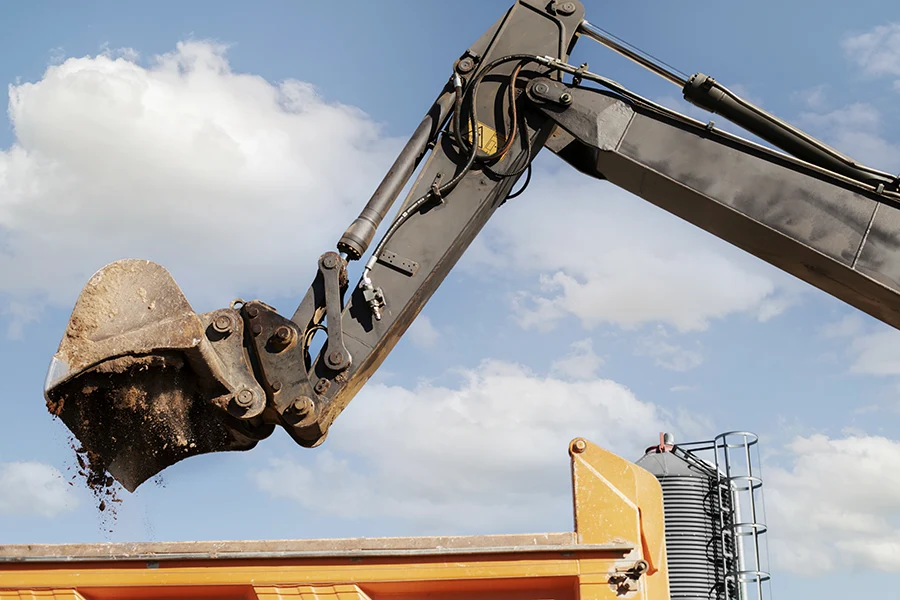
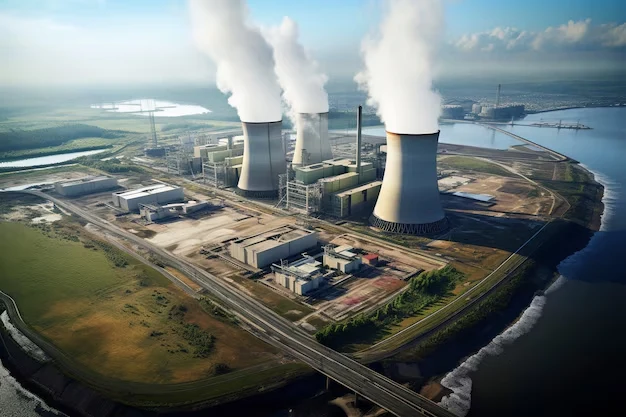
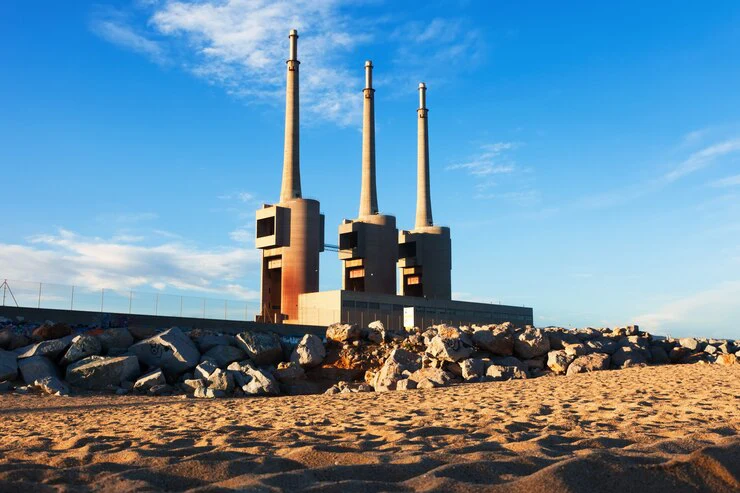
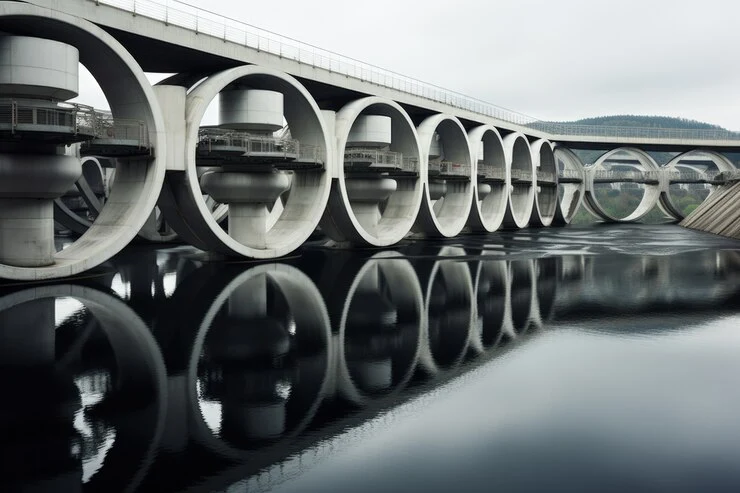