Roll Forging Services
- Our roll forging services deliver high-speed production of lightweight, high-strength components with smooth finishes and minimal residual stress.
- The process provides superior structural integrity, minimizes the need for additional machining, and is perfectly suited for aerospace, automotive, and high-performance industrial uses.
- Dimensional Accuracy: ±0.1mm–±0.3 mm
- Fast Production for Complex Geometry Parts
- Short Lead Times for Urgent Runs
- ISO 9001 & AS9100D Certified
- REACH & RoHS Compliant
Our Roll Forging Process
Each stage of our roll forging process is carefully controlled to deliver high-strength parts with excellent dimensional accuracy and minimal material waste.
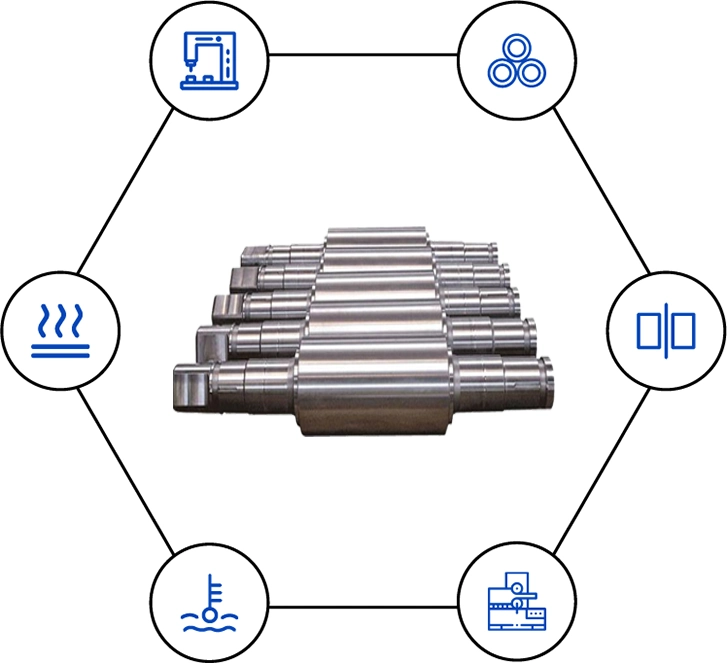
Raw Material Selection
We source high-quality billets or bars with specified chemical compositions and mechanical properties tailored to customer requirements.
Cutting & Heating
The raw material is cut to the required length and uniformly heated(between 980°C and 1300°C) in a controlled environment to achieve optimal plasticity for deformation.
Roll Forging Operation
Heated billets are passed between rotating grooved rolls. The material is progressively compressed and elongated to achieve the desired shape and profile.
Controlled Cooling
After forging, parts undergo a controlled cooling process to relieve internal stresses and ensure consistent metallurgical properties.
Heat Treatment (Optional)
For enhanced performance, we offer tailored heat treatment options such as normalizing, quenching, and tempering, depending on the application.
Machining & Finishing
Forged parts may undergo CNC machining to achieve tight tolerances. Additional finishing processes ensure surface quality and dimensional precision.
Roll Forging Materials
We use a wide range of high-performance metals, selected for strength, formability, thermal stability, and customer-specific requirements, to meet diverse applications.
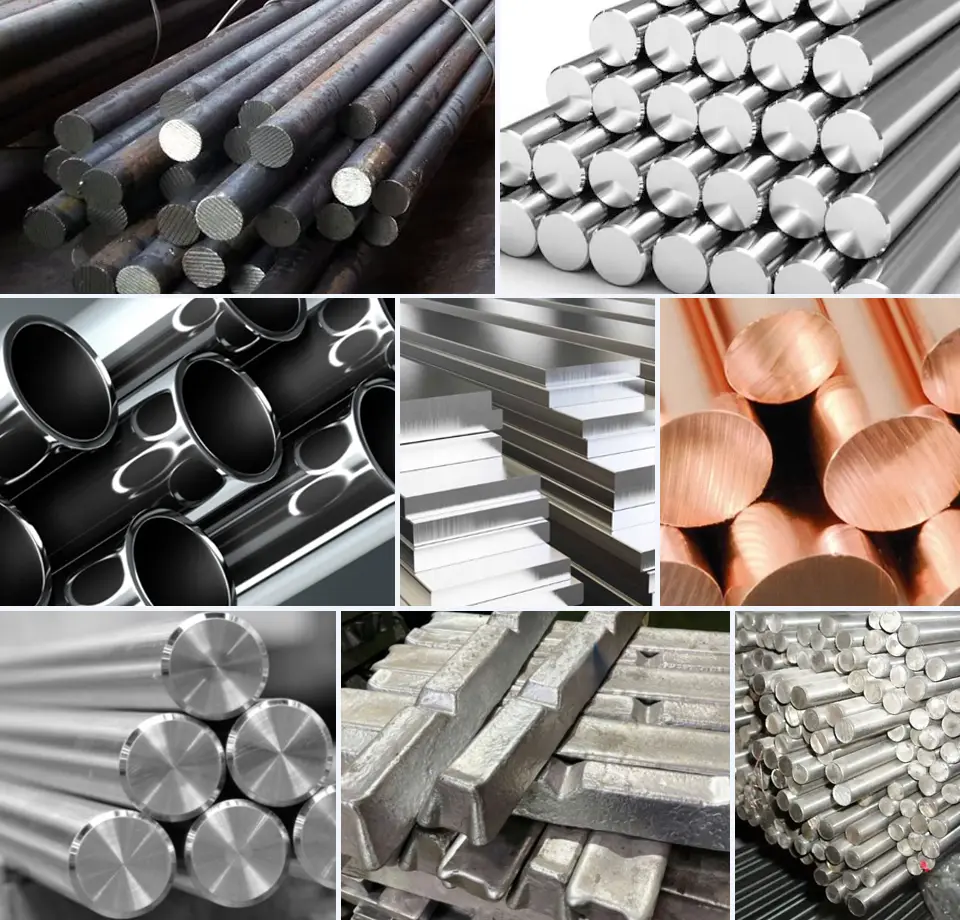
Carbon Steel
Offers excellent strength and cost-efficiency, ideal for shafts, rods, and automotive parts requiring durability, machinability, and wear resistance.
Alloy Steel
Strengthened with chromium, molybdenum, and other elements for high toughness, strength, and fatigue resistance in mechanical and structural uses.
Stainless Steel
Resists corrosion and scaling at high temperatures, perfect for roll-forging valves, fasteners, medical tools, and food-processing components.
Aluminum Alloys
Corrosion-resistant and lightweight, perfect for automotive, aerospace, and structural parts needing formability and a strong strength-to-weight ratio.
Copper Alloys
Outstanding thermal and electrical conductivity, well-suited for connectors, electrical contacts, and forged parts in heat transfer applications.
Titanium Alloys
Extremely strong, lightweight, and corrosion-resistant; ideal for aerospace, medical, and high-performance parts in harsh or weight-sensitive environments.
Magnesium Alloys
Among the lightest structural metals, offering superb machinability and used in aerospace and automotive parts for efficiency and weight savings.
Nickel Alloys
High-temperature and corrosion resistance, used in roll forging turbine components, chemical equipment, and aerospace fasteners requiring extreme durability.
Tolerance for Roll Forging Services
We maintain strict tolerance standards to ensure every roll-forged component meets the precise specifications required for high-performance applications. Below are our standard tolerance capabilities.
Tolerance Parameter | Tolerance Value |
Section Reduction | ±0.5% to ±1.0% |
Perpendicularity | ±0.2 mm per 100 mm |
Length of Thread Relief | ±0.05 mm |
Radius Consistency | ±0.1 mm |
Profile Accuracy | ±0.3 mm |
Material Flow Control | ±0.2 mm |
Surface Distortion | ≤ 0.3 mm |
End-to-End Concentricity | ±0.3 mm |
Thickness Uniformity | ±0.1 mm |
Twist/Spin Tolerance | ≤ 1° per meter |
Deformation Resistance | ±0.2 mm |
Dimensional Consistency of Keyways | ±0.1 mm |
Cross-Sectional Geometry | ±0.5% |
Flatness of Surface after Rolling | ≤ 0.1 mm |
Edge Contour Accuracy | ±0.2 mm |
Applications
Roll forging is used in many industries to make strong, precise, and cost-effective metal parts. Our roll-forged parts are widely applied in the following sectors:
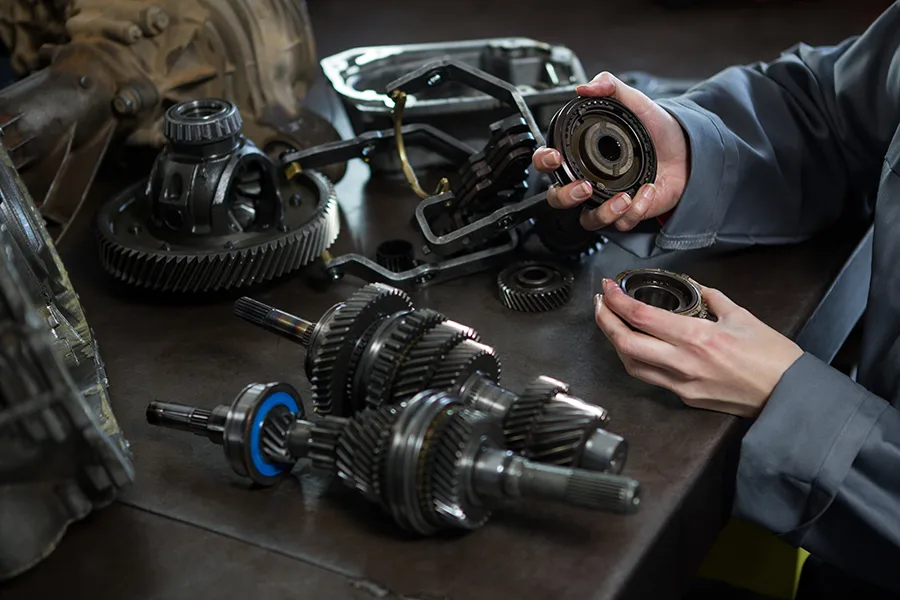
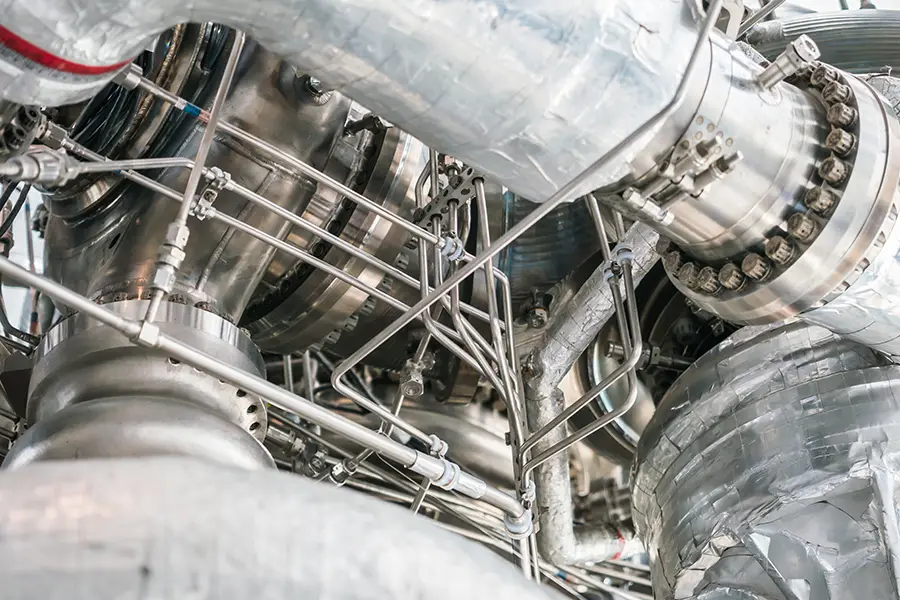
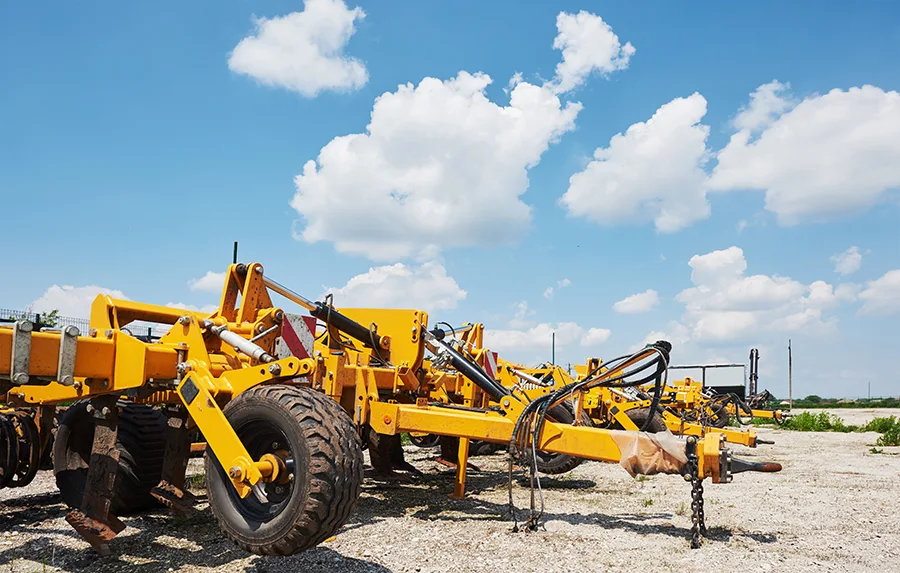
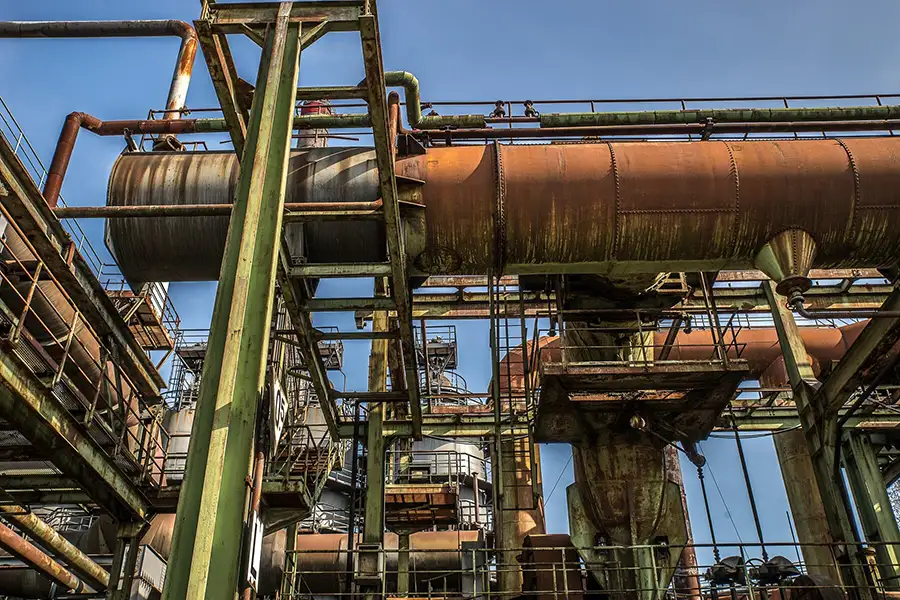
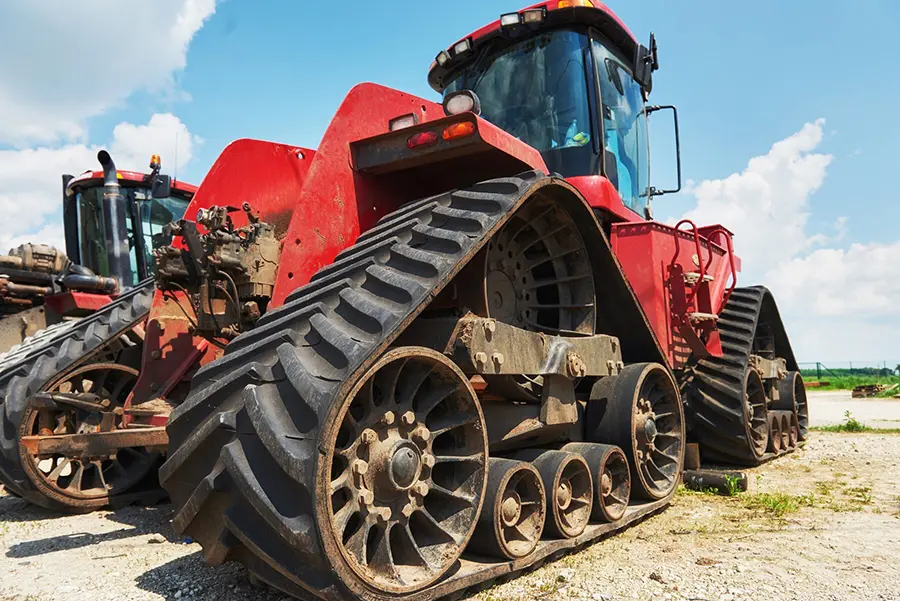
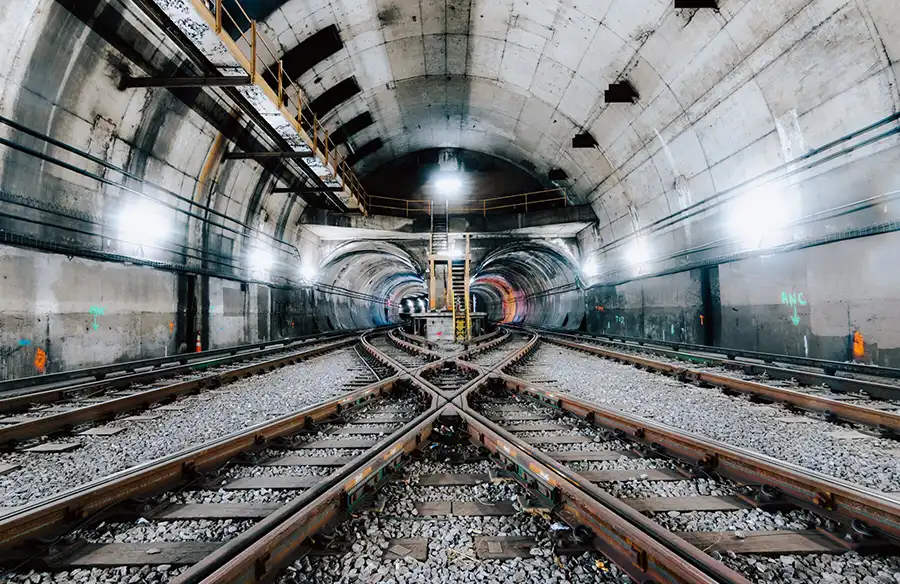
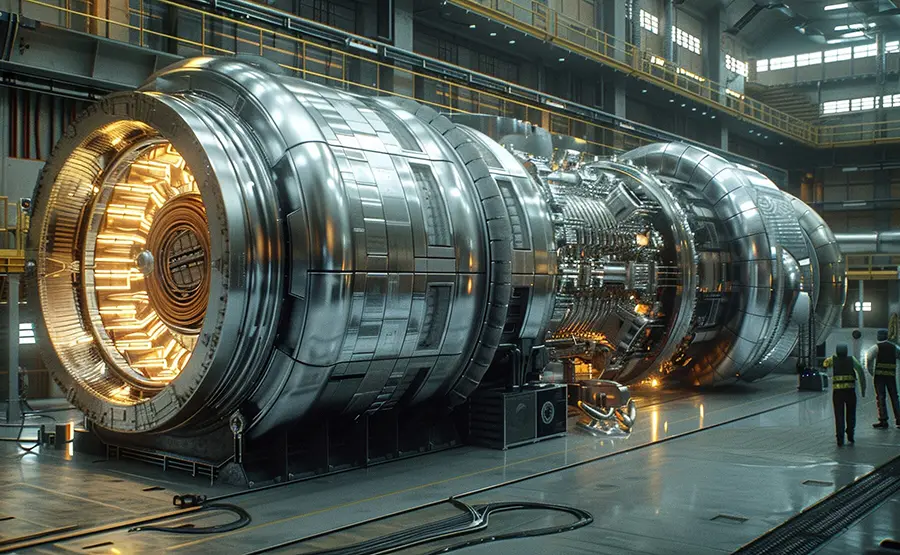
Automotive Industry
Axles, steering components, gear blanks, transmission shafts, and torsion bars benefit from improved fatigue strength and dimensional accuracy.
Aerospace Sector
Structural elements, landing gear parts, and engine shafts require lightweight strength and grain alignment that roll forging delivers.
Construction and Heavy Equipment
Pins, joints, linkages, and drive shafts used in cranes, excavators, and bulldozers demand high strength and wear resistance.
Oil & Gas
Components like drill collars, couplings, and tool joints need impact resistance and structural integrity in extreme environments.
Agricultural Machinery
Durable and wear-resistant parts such as spindles, axles, and discs benefit from the enhanced strength roll forging offers.
Railway and Marine Engineering
Wheels, shafts, and couplings produced through roll forging ensure reliability under high loads and dynamic stresses.
Power Generation
Turbine components, rotor shafts, and couplings require precise tolerances and consistent material structure to ensure operational stability.
Contact Us Now
FAQs
What component shapes can be roll forged?
We produce stepped shafts, tapered parts, gear blanks, flanges, and custom profiles requiring gradual deformation and precise cross-sectional accuracy.
What is your dimensional tolerance capability?
We maintain tight tolerances, including ±0.2 mm on critical dimensions, ±0.1 mm on radius consistency, and ≤1° twist per meter.
Can you roll forge multiple-step profiles?
Yes, we can roll forge stepped, tapered, or complex multi-section parts using progressive passes and custom roll tooling.
What is the maximum size you can roll forge?
We can roll forge parts up to 300 mm in diameter and up to 2 meters in length, depending on material.
Can roll forging reduce material waste?
Yes, it achieves near-net shape parts with minimal flash, optimizing material use and reducing costs compared to traditional forging methods.
Can you handle small batch production?
Yes, we support both small batch and large-scale production runs with flexible tooling and scheduling to meet project requirements.