Ring Forging Services
- Our ring forging services deliver high-strength, seamless rings with superior grain flow and dimensional accuracy.
- We offer full customization in size, material, and tolerance to meet your exact specifications, ideal for demanding applications in aerospace, energy, and heavy machinery industries.
- Machining Tolerance: ±0.01mm
- Up to 30% Lower Procurement Cost
- Capable of Forging Large-sized Ring Products
- Meets ISO9001 Quality System Standards
- Conforms to PED and AD2000 Specifications
Our Ring Forging Process
Precision-controlled from billet selection to final inspection, our ring forging process ensures strength, accuracy, and superior structural integrity.
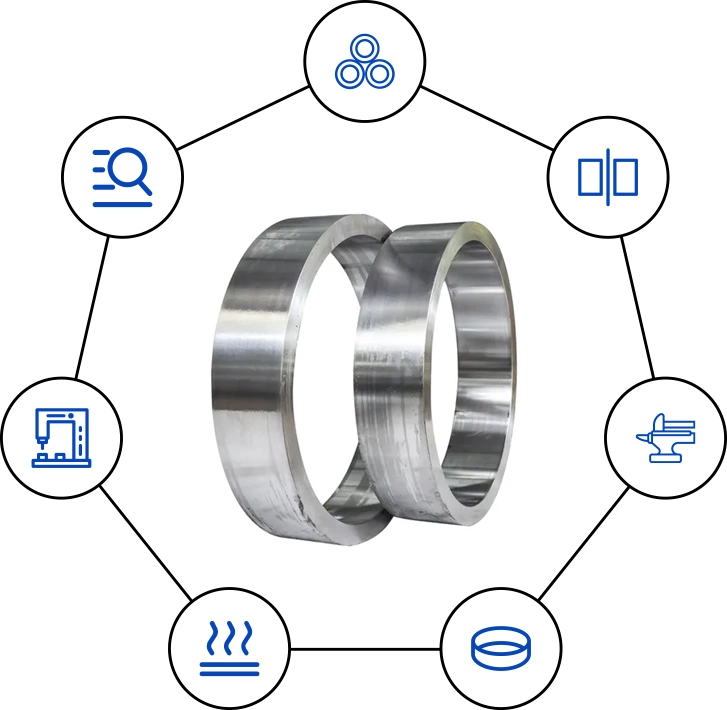
Raw Material Selection
Cutting & Heating
Billets are cut precisely and uniformly heated to achieve plasticity and eliminate internal stress before forging.
Forging
Ring Rolling & Shaping
Heat Treatment
Machining & Finishing
Inspection & Testing
Available Materials
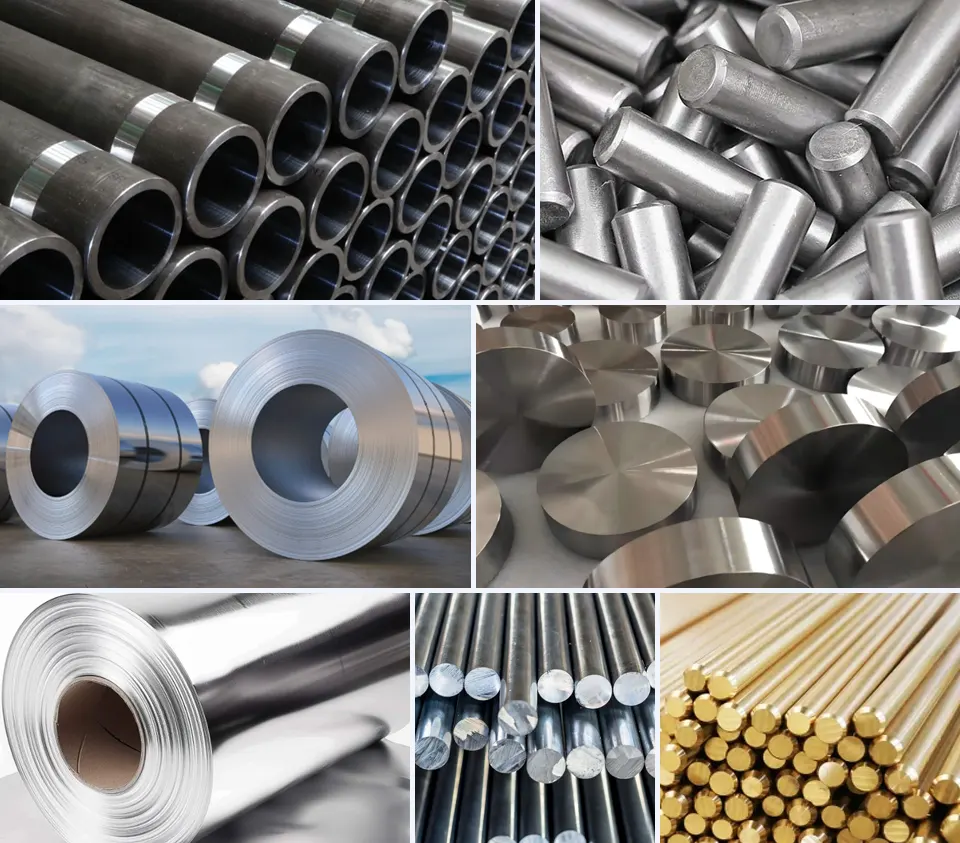
Carbon Steel
Alloy Steel
Stainless Steel
Titanium Alloys
Nickel Alloys
Aluminum Alloys
Brass
Tolerance for Ring Forging Services
Parameter | Tolerance Range |
Forging Grain Flow | ±15° to ±30° |
Perpendicularity | ±0.1 to ±0.3 mm |
Radial Runout | ±0.05 to ±0.2 mm |
Axial Runout | ±0.1 to ±0.5 mm |
True Position | ±0.2 to ±0.4 mm |
Forging Deformation | ≤5% |
Section Uniformity | ±0.1 to ±0.2 mm |
Hardness Distribution | ±5 to ±10 HV |
Surface Deformation (Peening) | ≤0.1 mm |
Sintering Shrinkage | ±0.2 to ±0.5% |
Microstructure Homogeneity | ≤5% variance in grain size |
Bore Concentricity | ±0.1 mm |
Tensile Strength Variation | ≤5% variance |
Yield Strength Deviation | ±5% |
Nondestructive Testing Methods for Forged Ring Quality
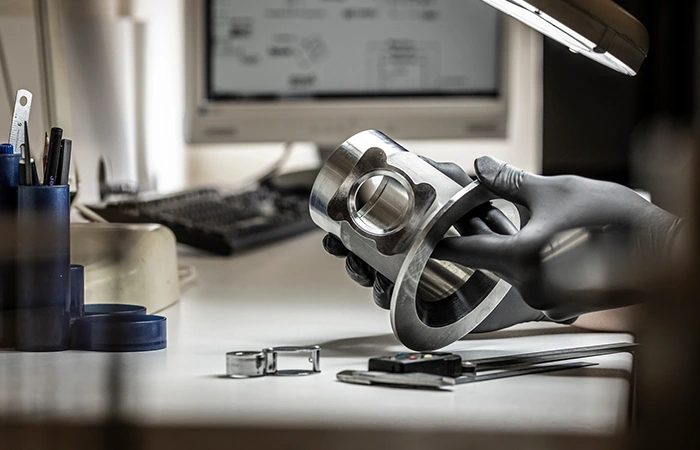
Visual Inspection (VT)
Conducted by certified inspectors to assess surface condition, geometry, and visible defects.
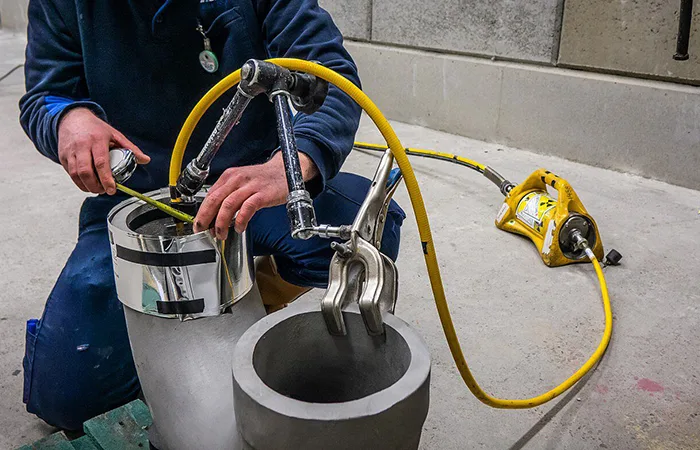
Radiographic Testing (RT)
Uses gamma or X-rays to examine internal structures and find inclusions, voids, or fissures that are hidden.
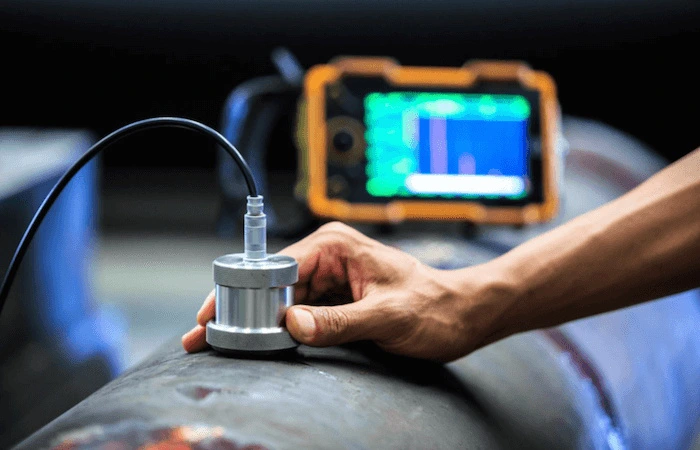
Ultrasonic Testing (UT)
Applies high-frequency sound waves to identify internal imperfections, such as inclusions and discontinuities, within the material.
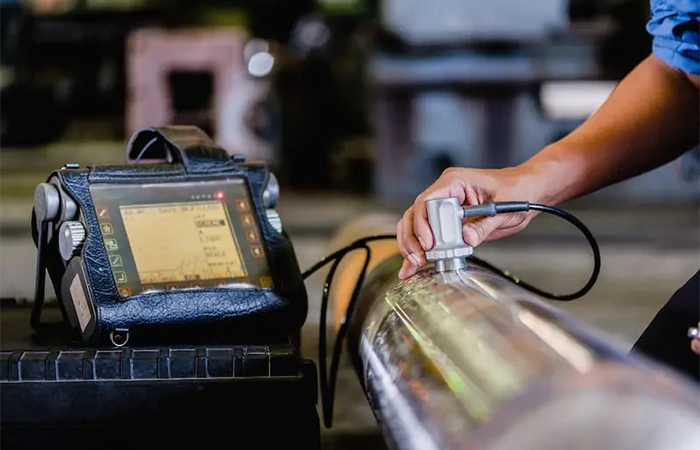
Eddy Current Testing (ET)
Detects surface and just-below-the-surface cracks in conductive materials via electromagnetic induction without coming into direct contact with them.
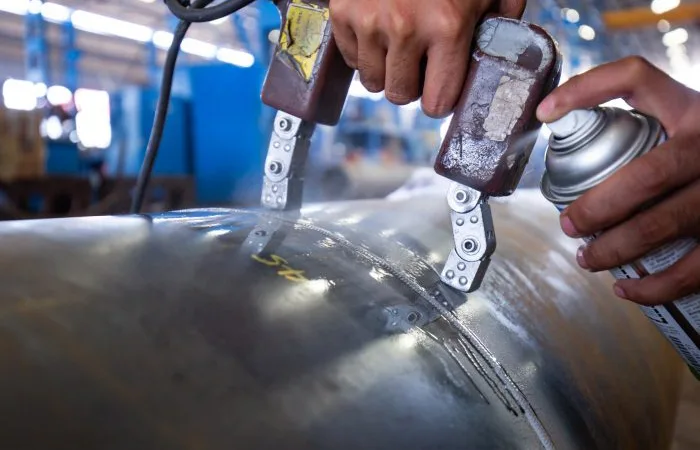
Magnetic Particle Testing (MT)
Reveals surface and slightly subsurface flaws in ferromagnetic materials through magnetic fields and iron particle application.
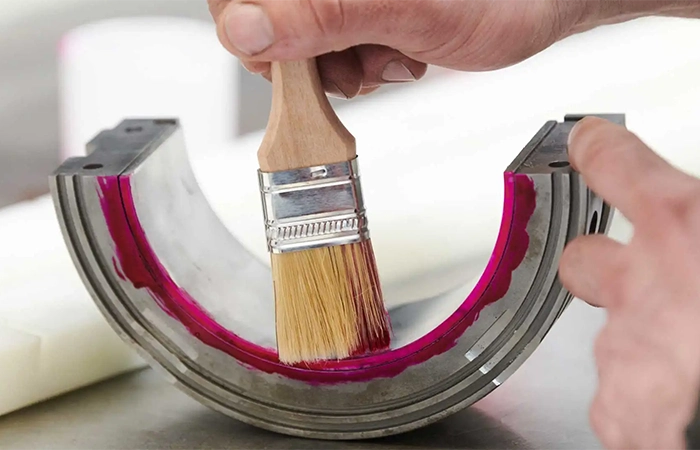
Dye Penetrant Testing (PT)
Exposes surface-level cracks or defects using visible or fluorescent dyes, ideal for non-magnetic and non-ferrous materials.
Our Ring Forging Parts
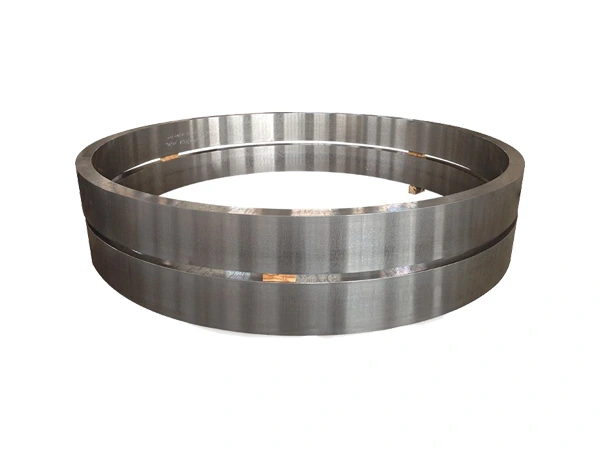
- Max diameter up to 8000 mm.
- Max length reaches 1200 mm.
- Supports forging weight up to 30 tons.
- Precision machining tolerance ±0.01 mm.
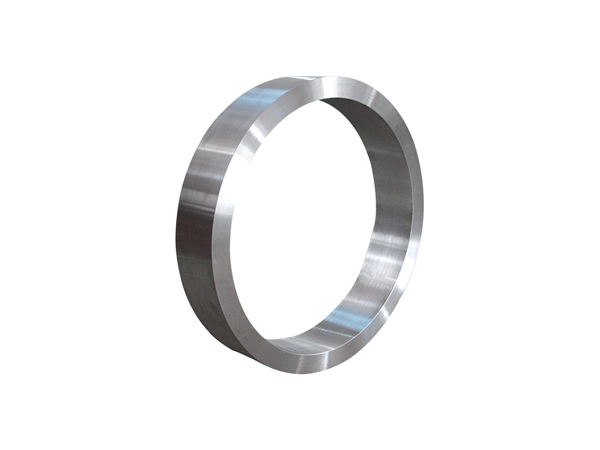
- Good sealing under pressure and temperature.
- Low friction with moving mechanical parts.
- Strong resistance to corrosion and aging.
- Simple structure, quick and easy installation.
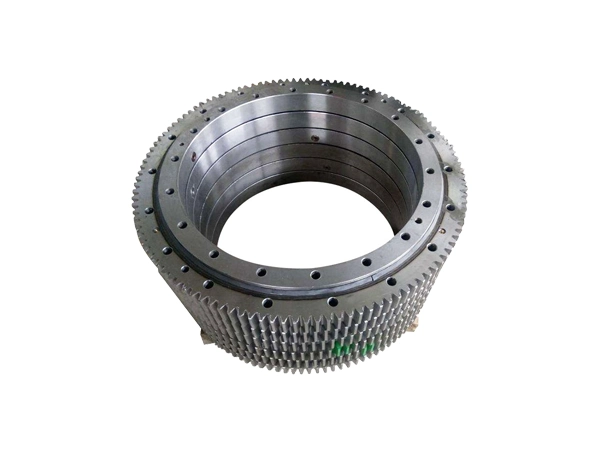
- Also called rotary table or turntable bearing.
- Known as slewing ring or rotary support.
- Bears axial, radial, and tilting force.
- Widely used in real-world industrial applications.
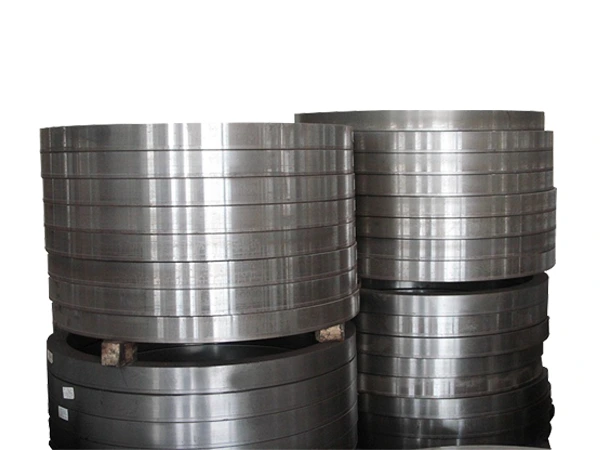
- Produces free forgings from 1–7000 kg.
- Max rolled ring diameter reaches 3000 mm.
- Custom sizes available per client requirement.
- KM-180 ultrasonic flaw detector ensures quality.
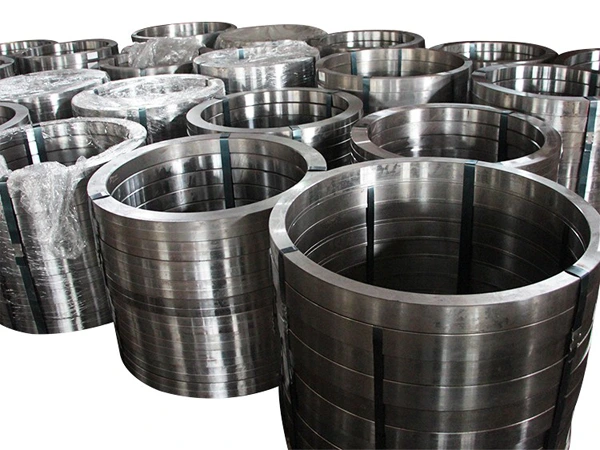
- Used in vessels containing gas or liquid.
- Suitable for normal, low, stainless steel conditions.
- Developed for extreme environments like nuclear plants.
- Resists corrosion, pressure, and temperature variations.
Applications
Our precision ring forging services serve a wide range of industries that demand high-strength, fatigue-resistant components for critical operations.
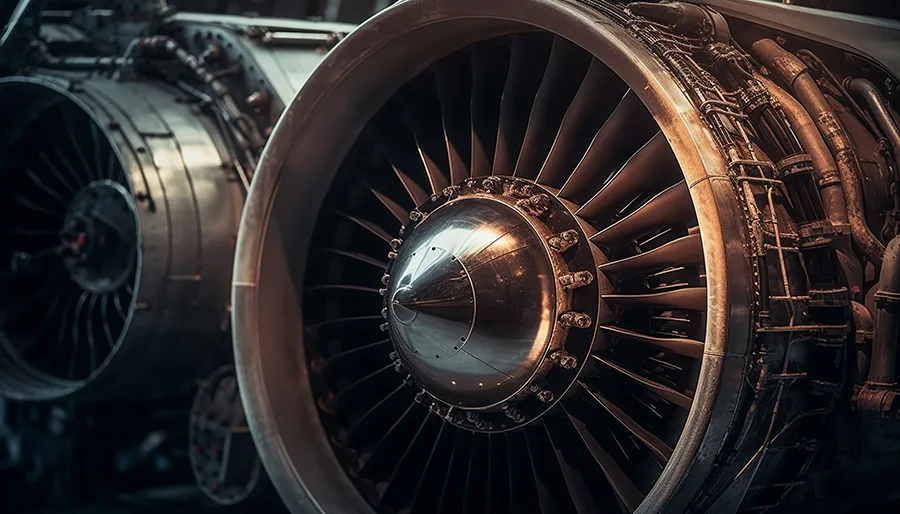
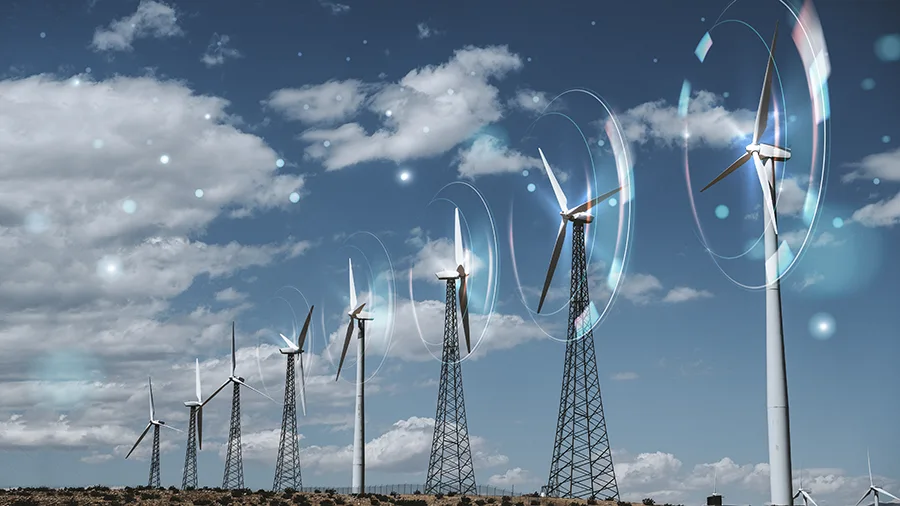
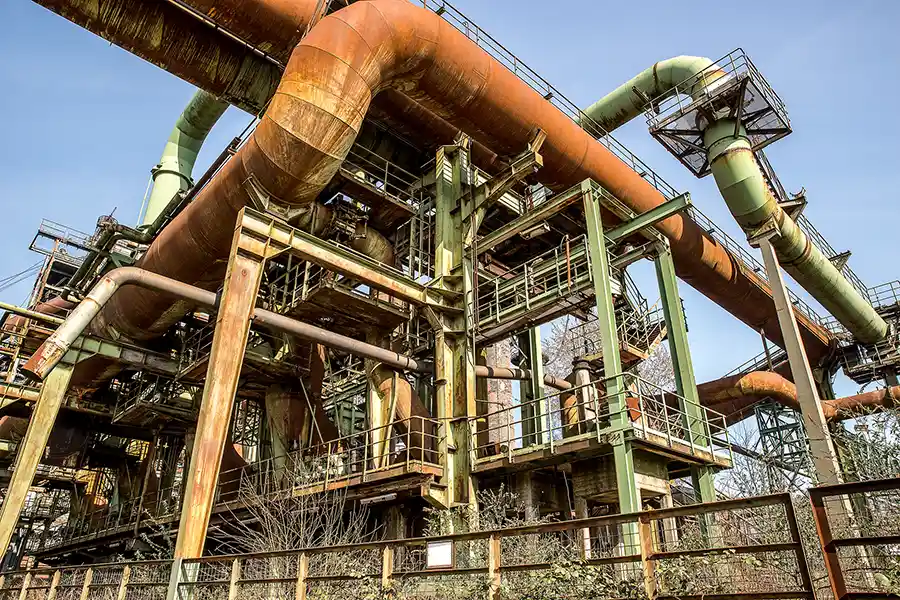
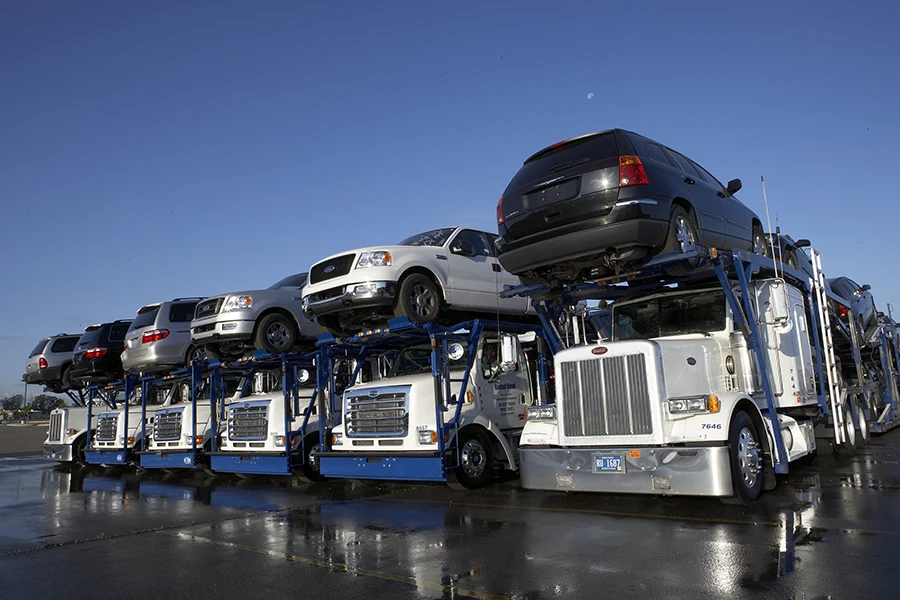
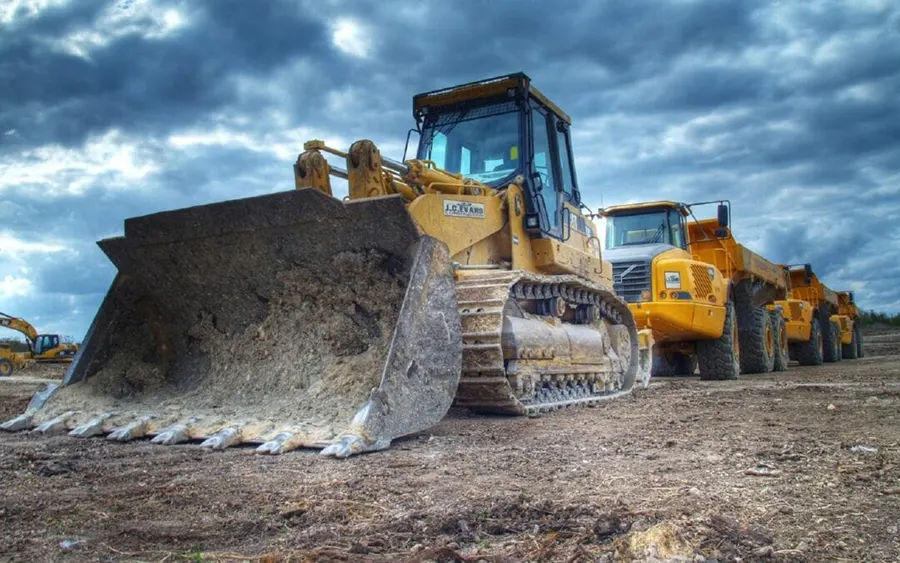
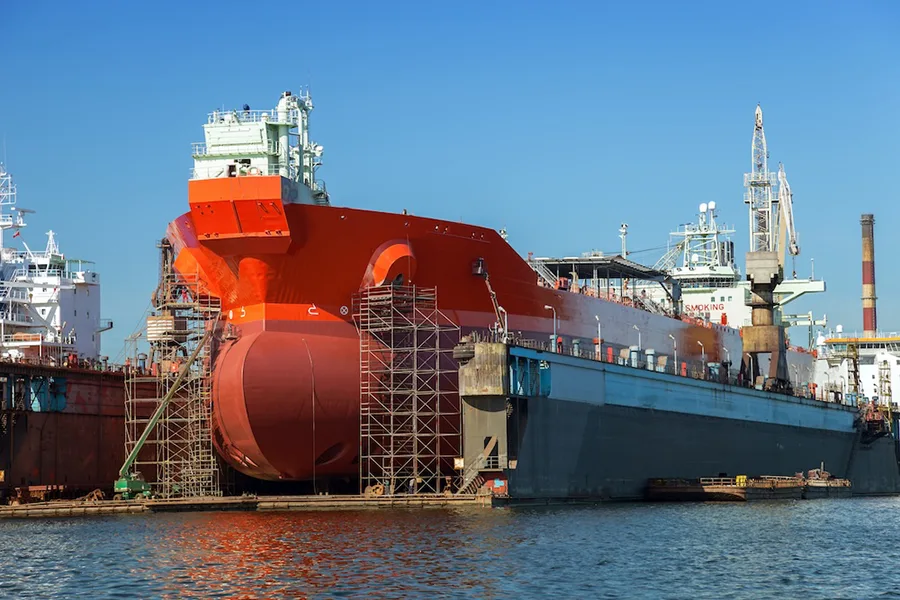
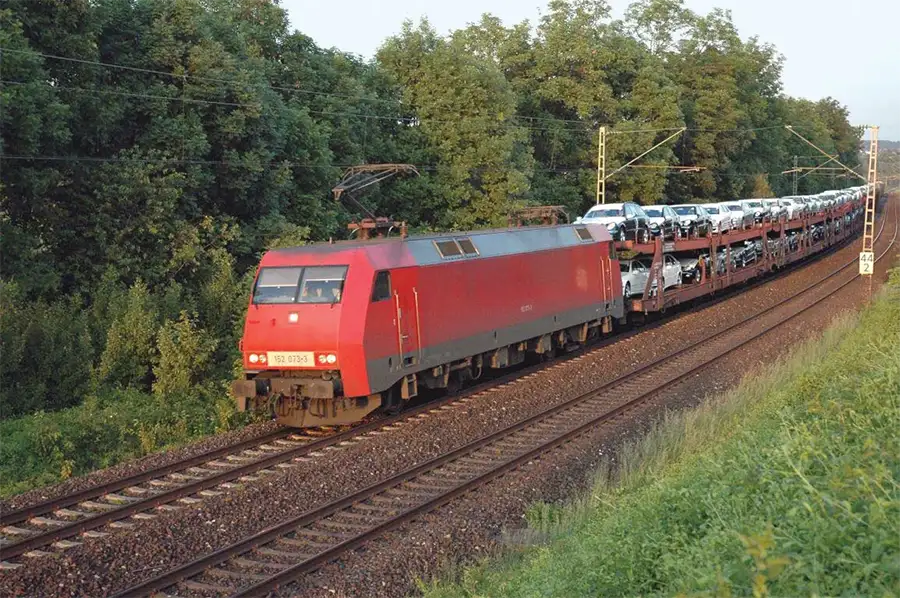
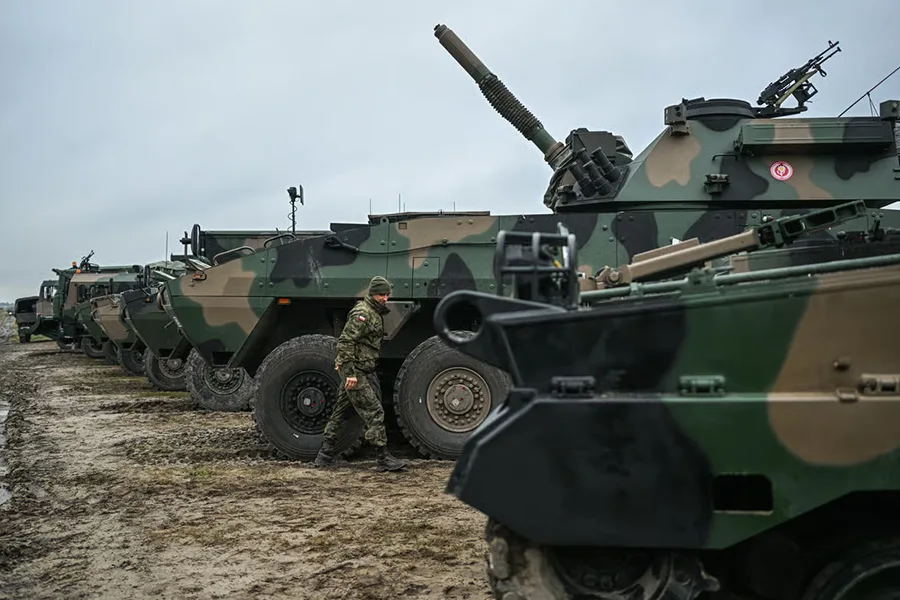
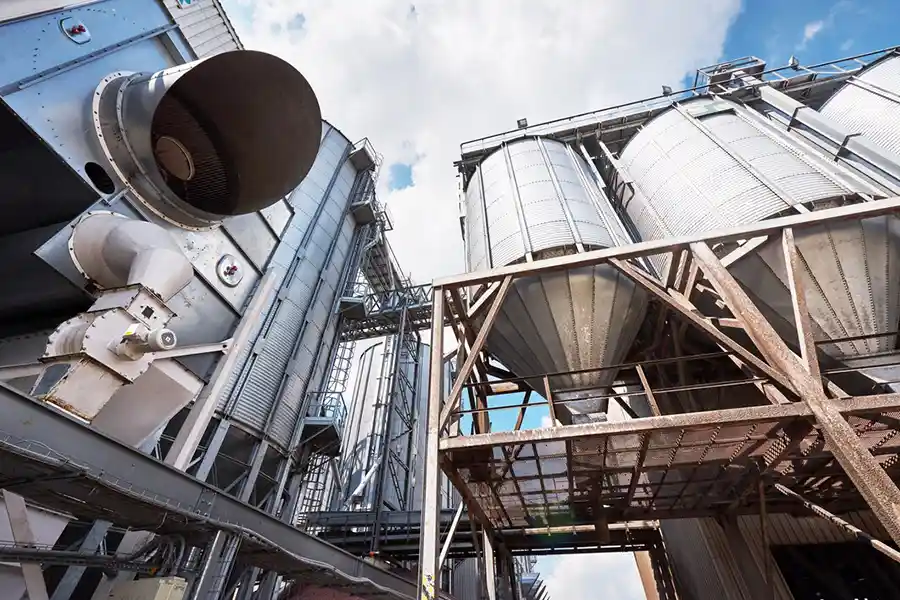
Aerospace
Power Generation
Applied in wind turbines, nuclear plants, and thermal power systems, forged rings ensure long service life under extreme thermal and mechanical stress.