Forged Shafts Manufacturer
- Our custom shaft forging delivers strength, precision, and durability to meet the toughest industrial demands with tight tolerances.
- Each forged shaft is made to your specifications from design to delivery, ensuring reliable performance in power, marine, automotive, and heavy machinery.
- Custom Shafts Made to Your Drawings
- Large-size Forged Shafts Available
- Sample Service, MOQ is 1 Piece
- Urgent Delivery in 15–30 Days
- Monthly Output: 500–1000 Tons
- ISO9001, PED, SGS Certified
By Shaft Structure
We manufacture forged shafts in a variety of structural designs to meet diverse mechanical and operational demands across industries.
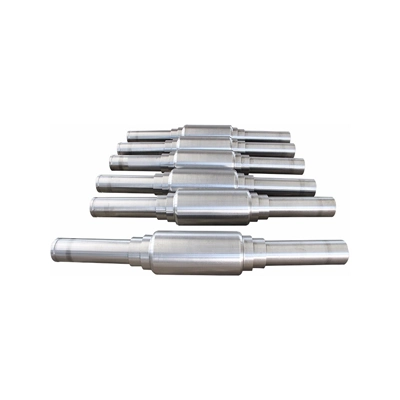
Stepped Shafts
- Varying diameters support gears, pulleys, and bearings.
- Smooth transitions reduce stress and improve strength.
- Used in gearboxes, turbines, and precision machinery.
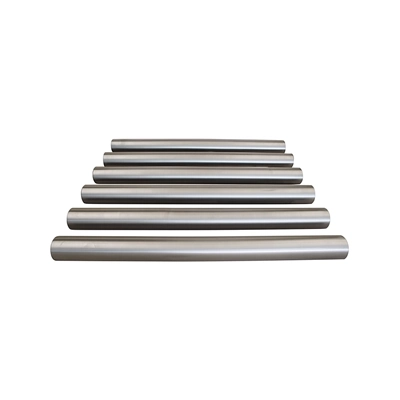
Straight Shafts
- Uniform diameter enables consistent torque transmission.
- Simple to machine and balance efficiently.
- Ideal for pumps, conveyors, and motors.
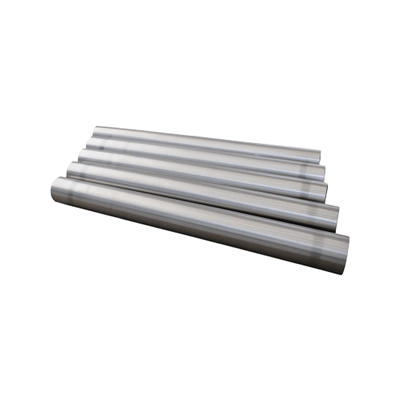
Hollow Shafts
- Bore reduces weight while maintaining strength.
- Enables internal routing for cables or fluids.
- Used in robotics and electric drives.
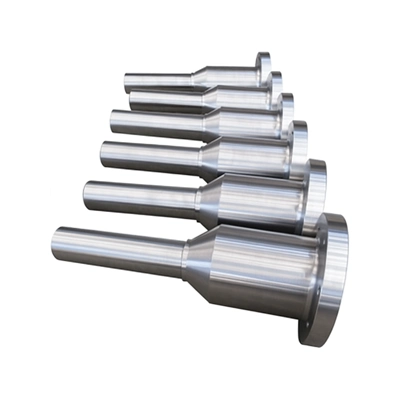
Flanged Shafts
- Flange connects directly with bolts or couplings.
- Used in HVAC, fire, water, and industrial systems.
- Found in marine and power applications.

Spline Shafts
- External splines provide precise torque transfer.
- Support axial movement with rotational accuracy.
- Match straight, involute, or serrated profiles.
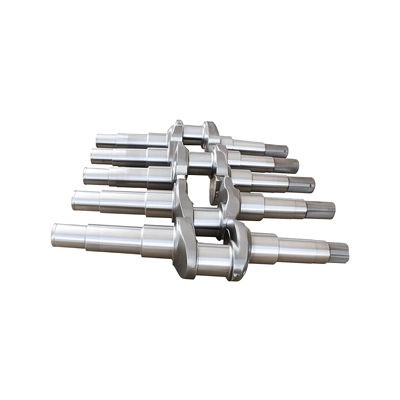
Crank Shafts
- Convert reciprocating motion into rotary drive.
- Include counterweights to reduce operational vibration.
- Used in engines, compressors, and presses.
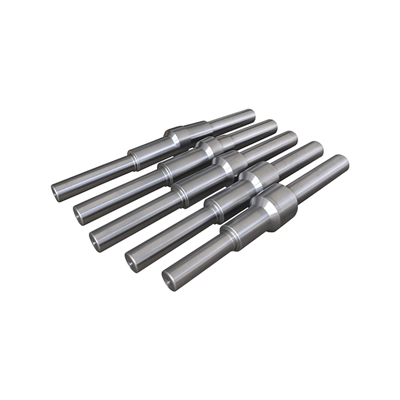
Eccentric Shafts
- Offset sections create controlled oscillating motion.
- Used in pumps, presses, and screens.
- Require high precision for smooth operation.
By Material
For your particular application, we provide a large selection of high-performance materials for Forged Shafts to guarantee optimal strength, longevity, and performance.
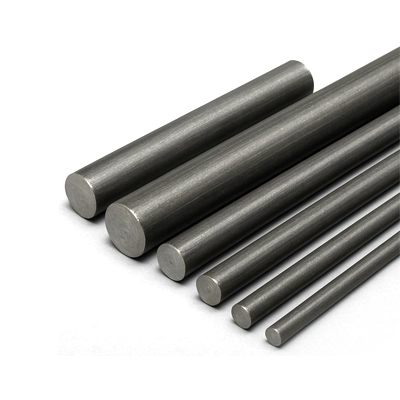
- Affordable and tough for general engineering and mechanical use.
- Good machinability, weldability, and wear resistance.
- Available in grades for specific strength and hardness needs.
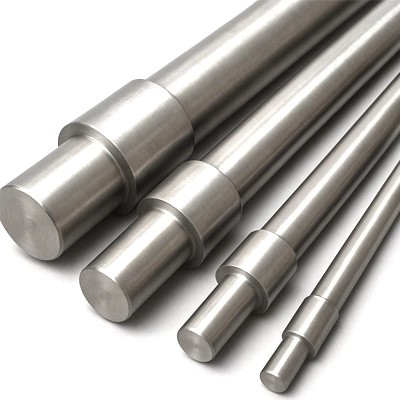
- Alloyed for improved strength, fatigue, and impact resistance.
- Ideal for aerospace, automotive, and high-load industries.
- Maintains performance under extreme stress, heat, and pressure.
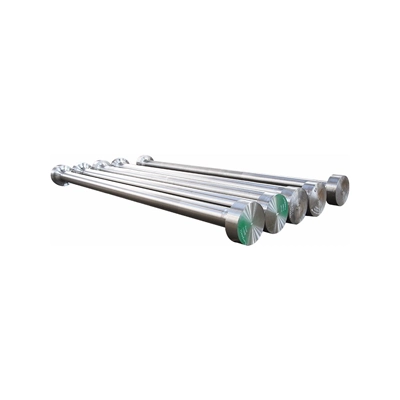
- Corrosion-resistant shafts for marine, food, and pharma use.
- Retains strength in corrosive or humid environments.
- 304, 316, 410 grades offer varying resistance levels.
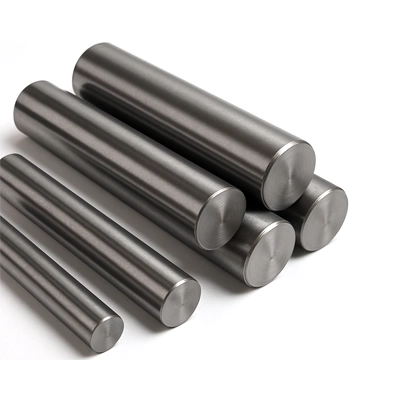
- Designed for wear, heat, and shock resistance.
- Grades like D2, H13, O1 offer excellent hardness.
- Used in dies, molds, and tooling applications.
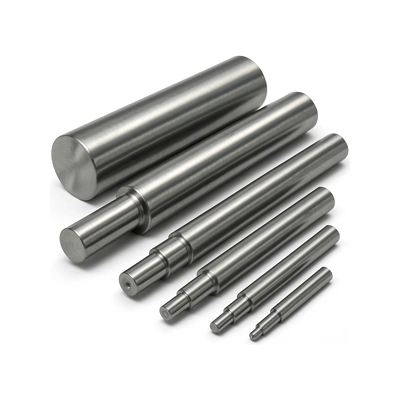
- Withstands heat, corrosion, and pressure in harsh conditions.
- Preferred in oil, chemical, and aerospace industries.
- Inconel, Monel offer thermal and structural reliability.
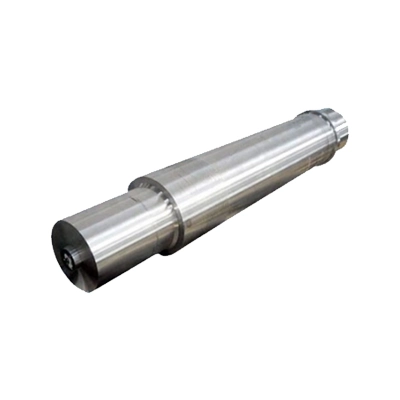
- Lightweight, strong shafts for aerospace and medical sectors.
- Offers biocompatibility, fatigue strength, and corrosion resistance.
- Ti-6Al-4V used in extreme, weight-sensitive environments.
Our Forged Shaft Production Process
We utilize a controlled, multi-step forging process to ensure exceptional strength, precision, and performance in every forged shaft produced.
Material Inspection
Inspect certified 40CrMo bars, verify documentation, and organize inventory properly.
Billet Cutting Preparation
Precisely cut alloy bars to specified shaft length per engineering drawings.
Billet Pre-Heating Furnace
Uniformly heat billets to forging temperature, around 1,150 °C, to ensure consistency.
Initial Forging Operation
Rough-shape shaft using hydraulic press or hammer until the basic contour is achieved.
Upsetting End Formation
Form enlarged heads, flanges using upset dies under controlled conditions.
Groove Fullering Process
Define grooves and transitions using fullering tools with die precision.
Intermediate Die Blocking
Refine shaft shape through blocked impression dies approaching final geometry.
Flash Trimming Execution
Remove flash precisely using trimming dies, preparing for normalization treatment.
Normalize Treatment and Storage
Heat‑treat shafts for grain refinement, then cool and store properly.
Applications
Our custom forged shafts deliver reliable performance under extreme conditions, tailored to meet specific load, torque, and environmental demands across various industries.
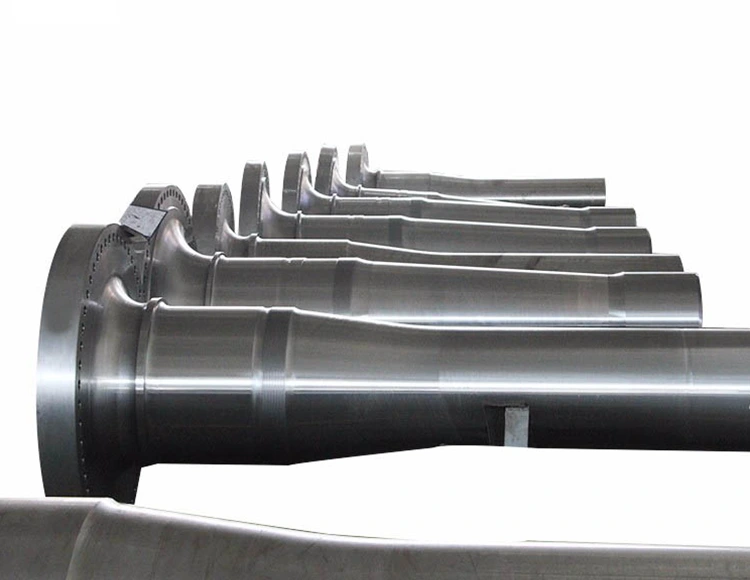
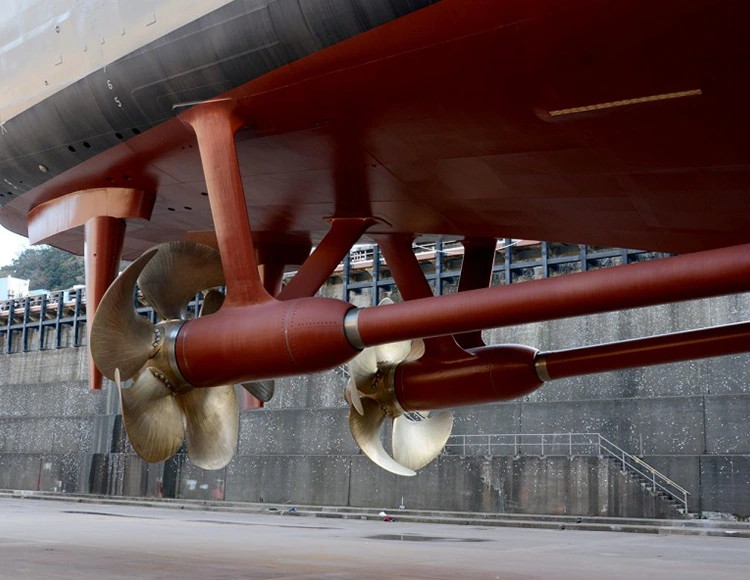
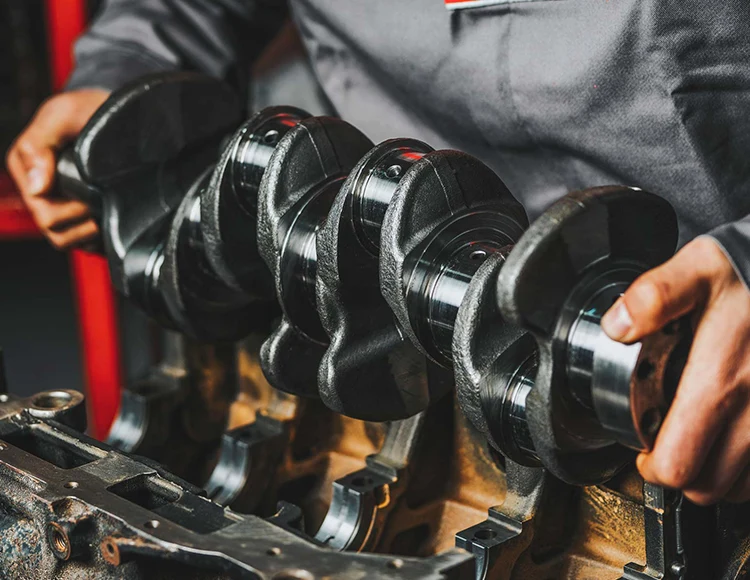
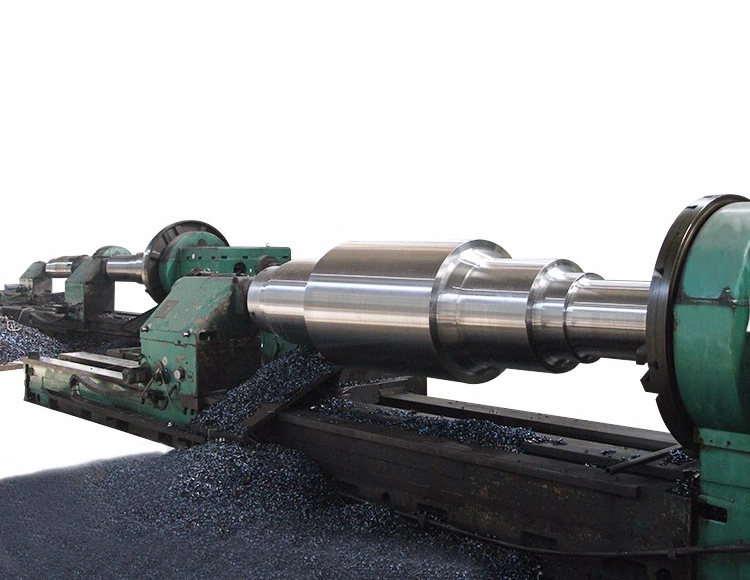

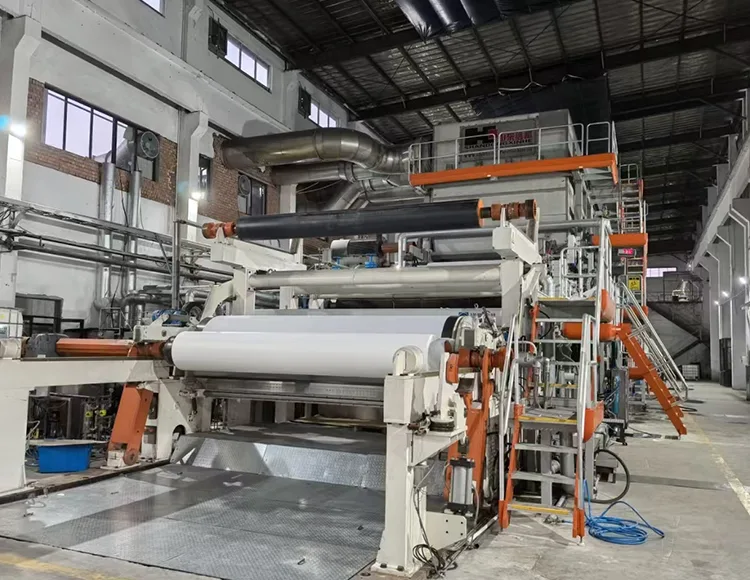
Power Generation Rotor Shafts
Used in turbines, generators, and wind turbines; engineered for high torque, continuous loads, and thermal stability in demanding power generation environments.
Marine Shafts
Built for propellers and tail shafts; made with corrosion-resistant alloys to withstand saltwater, high torque, and long-term marine propulsion requirements.
Automotive Shafts
Custom-forged drive, axle, and transmission shafts; deliver high fatigue resistance, dynamic load endurance, and precise alignment for automotive systems.
Aerospace Shafts
Lightweight titanium or nickel alloy shafts; provide high strength, corrosion resistance, and stability under extreme temperature and pressure conditions.
Agricultural Shafts
Designed for tractors and PTO systems; rugged, wear-resistant shafts that perform reliably in dusty, muddy, and high-load agricultural environments.
Industrial Shafts
Used in fans, pumps, compressors, and mill drives; offer stable torque transmission, vibration resistance, and long-term performance in heavy industry.