Open-die Forging Services
- We provide open-die forging blanks, semi-finished products, finished parts, and prefabricated components with superior strength and grain refinement.
- Our offerings include shafts, flanges, rings, gear blanks, and heavy blocks for industries like power generation, marine, mining, and petrochemical.
- Wide Material Range: Steel, Alloy, etc
- Flexible Batch Size: Prototype to Mass
- Custom Dimensions Based on Client Drawings
- Supports Tight Tolerances and Special Standards
- Certified to ASTM, EN, JIS, BS, etc
- ISO 9001 and ISO 14001 Certified Systems
Our Open-die Forging Process
From ingot selection to final inspection, our open-die forging ensures superior strength, accuracy, and quality for demanding industrial applications worldwide.
Ingot Selection
Select high-quality ingots to ensure excellent raw material properties for forging applications.
Chemical Analysis
Perform chemical analysis to verify material composition meets required industry and customer specifications.
Cutting
Cut ingots into suitable lengths for uniform heating and effective forging process control.
Heating Furnace
Heat billets uniformly in a furnace to the optimal forging temperature for deformation.
Forging
Forge heated billets using open dies to refine grain structure and shape the material precisely.
Heat Treatment
Apply heat treatment to improve toughness, mechanical properties, and internal microstructure after forging.
Blank Inspection
Inspect forged blanks for dimensional accuracy and surface condition before proceeding to machining.
Rough Machining
Conduct rough machining to bring forged parts closer to required final dimensions efficiently.
Flaw Detection
Use non-destructive testing methods to detect internal cracks or defects in the forged material.
Tempering Process
Temper forged components to relieve internal stresses and enhance overall durability and toughness.
Mechanical Property Testing
Test mechanical properties like tensile strength and hardness to ensure compliance with technical standards.
Finish Machining
Perform precision finish machining to meet exact specifications and required tolerances for final use.
Magnetic & Spectrum Inspection
Conduct magnetic and spectrum inspection to verify structural integrity and material composition accuracy.
Packing
Pack forged components securely using protective materials to prevent damage during handling and shipping.
Transport & Shipping
Ship products by sea, air, or train based on delivery terms such as FOB or DDP.
Types of Open-die Forging
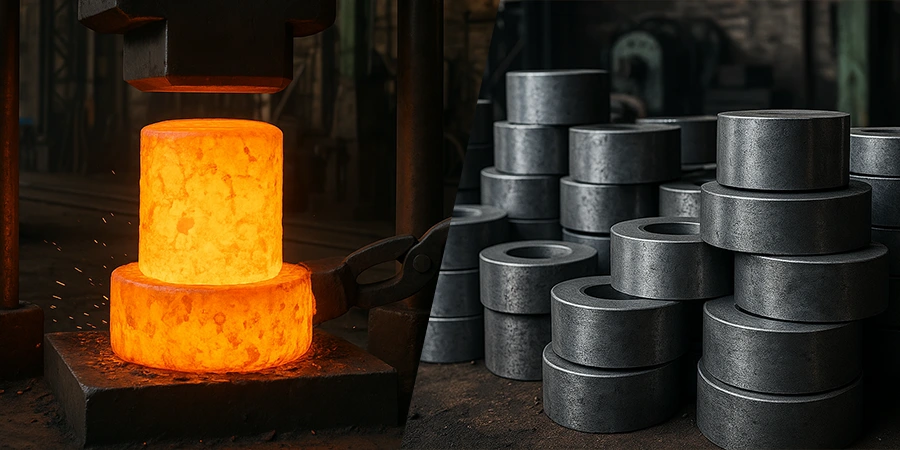
Open-die Drop Forging
- Billet is shaped through repeated controlled die strikes.
- Ideal for discs, shafts, and open-form components.
- Offers material efficiency without complex closed-die tooling.
- Common in mining, construction, and power sectors.
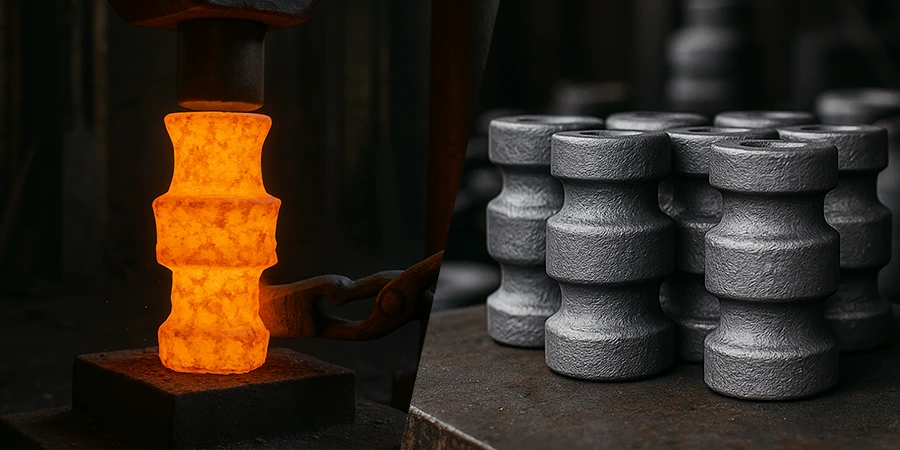
Open-die Hammer Forging
- Forging with repeated hammer blows for shaping metal.
- Produces custom shafts and stepped or irregular parts.
- Delivers strong grain flow and internal soundness.
- Preferred for low-volume or manual control jobs.
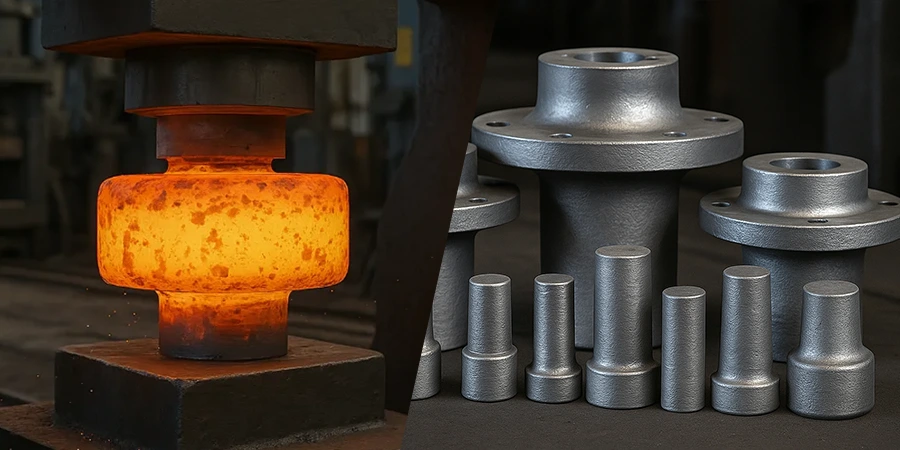
Open-die Press Forging
- Hydraulic press applies continuous pressure for shaping.
- Excellent for large, precise, and heavy-duty parts.
- Produces refined grain and consistent internal structure.
- Common in aerospace, energy, and heavy machinery.
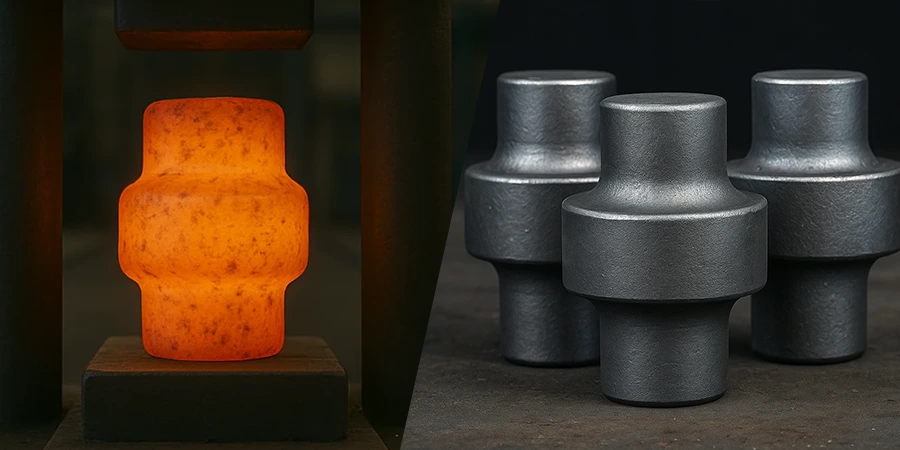
Open-die Upset Forging
- Increases section thickness by compressing billet height.
- Forms flanges, shaft ends, and thickened zones.
- Improves strength and fiber alignment in stressed areas.
- Ideal for connectors, shafts, and structural parts.
Tolerance for Open-die Forging
Our open-die forging processes are designed to meet exact size and structural standards. Below are the typical tolerances we maintain:
Parameter | Tolerance Range |
Grain Size Variation | ≤ 2 ASTM units |
Planarity (Out-of-Flatness) | ±0.5 mm – ±3.0 mm |
Axiality Deviation | ±1.0 mm – ±2.0 mm (per 100 mm length) |
Perpendicularity | ±0.5° – ±2.0° |
Sectional Thickness Variation | ≤ ±0.25 mm |
Edge Distortion | ±0.5 mm – ±2.0 mm |
Forge Ratio (Area Reduction) | 3:1 – 5:1 |
Shape Deformation | ±2% – ±5% |
Temperature Control (In-Process) | ±20°C – ±50°C |
Grain Flow Orientation | ±5° – ±15° |
Surface Hardness Variation | ±5 – ±25 HV |
Face Circularity | ±0.5 mm – ±2.0 mm |
Bore Concentricity | ±0.3 mm – ±1.0 mm |
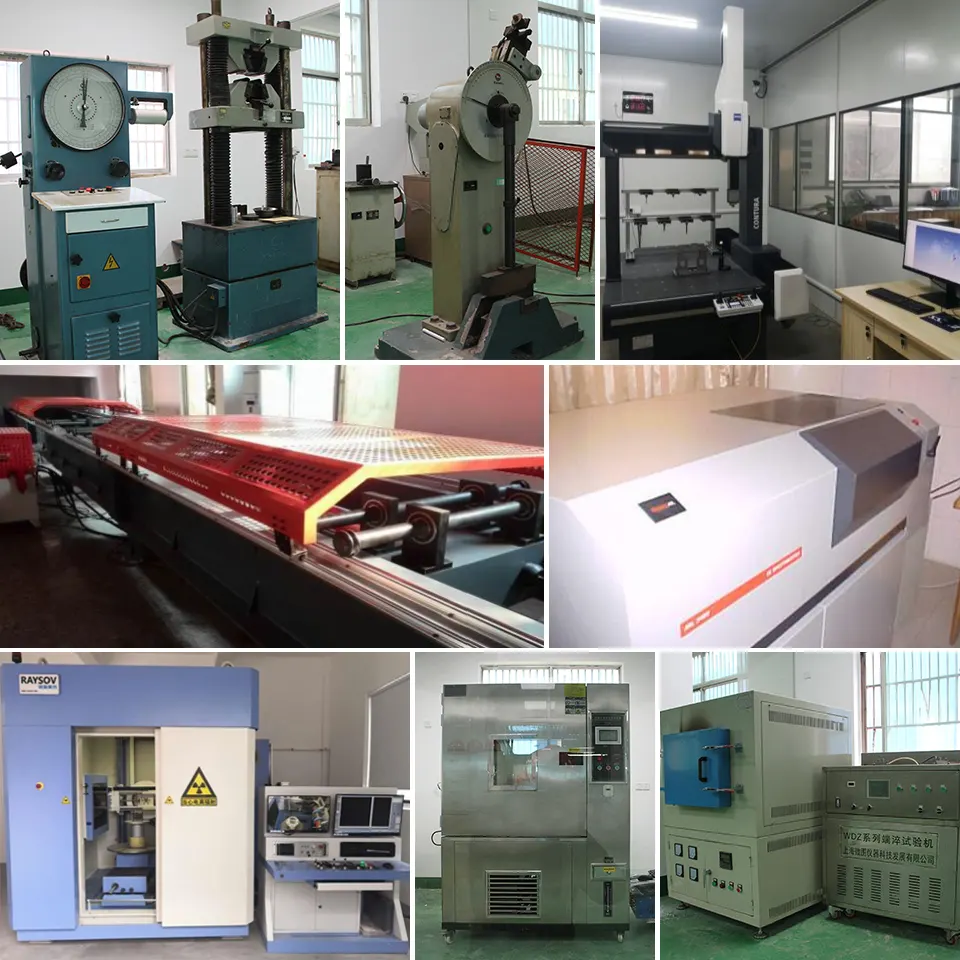
Quality Testing
With the use of precise heating, shaping, controlled deformation, optional heat treatment, and machining, our open-die forging process turns certified billets into high-strength components.
Deformation Behavior Evaluation
Upset and flow stress tests assess material plasticity and forging behavior under compressive load conditions.
Weldability and Creep Resistance
Weldability index and creep rupture tests ensure structural integrity during welding and prolonged high-temperature service.
Fracture Toughness Verification
KIC testing determines resistance to crack propagation, ensuring durability under stress and fatigue conditions.
Thermal Stability and Oxidation Resistance
Thermal cycling and oxidation tests evaluate resistance to temperature changes and scaling in extreme environments.
Thermal Conductivity Measurement
Laser flash method measures thermal diffusivity, essential for heat management in forged components.
Electrical and Magnetic Property Assessment
Impedance testing verifies electrical conductivity and magnetic permeability for specialized industrial forging applications.
Ductility and Mechanical Strength
Elongation and torsion tests determine stretchability and shear resistance under tensile and twisting forces.
Microstructure and Stress Analysis
SEM/EDS and stress relaxation tests reveal internal grain structure, elemental composition, and long-term load stability.
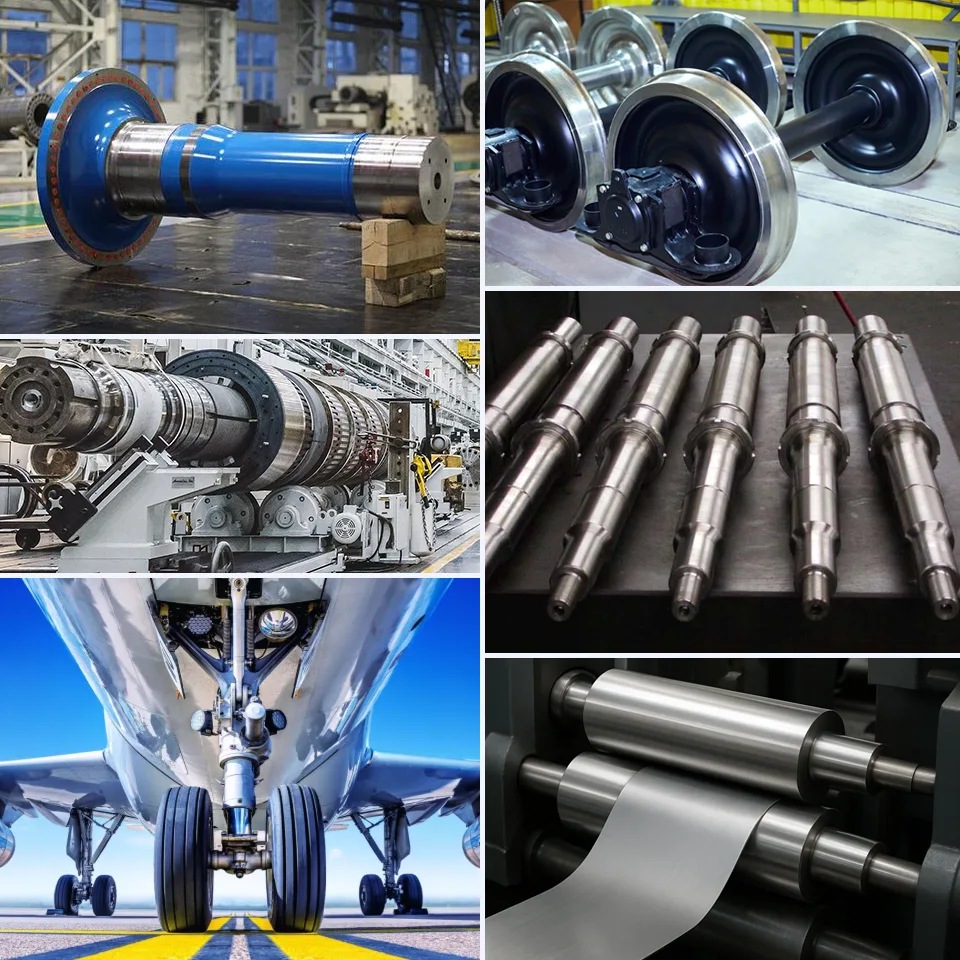
Applications
Open die forging produces large, high-strength parts with excellent reliability, widely used in energy, aerospace, marine, and heavy industries for critical component applications.
- Wind turbine main shafts
- Pressure vessel components
- Marine propulsion and drive shafts
- Power generation rotor shafts
- Mining and excavation equipment parts
- Subsea connectors and riser systems
- Aerospace landing gear components
- Hydraulic cylinder bodies and rods
- Work rolls for steel and paper mills
- Railway axles, wheels, and couplers
- Industrial shafts, spindles, and mandrels
Our Open Die Forging Parts
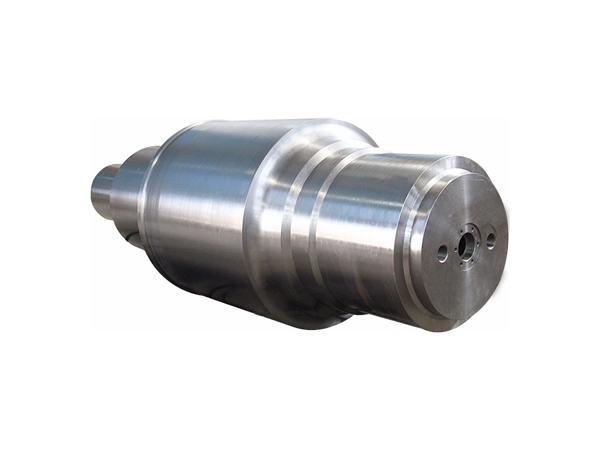
- Heavy-duty shaft for power generation systems.
- Open-die forged for superior structural integrity.
- Custom lengths, diameters, and flange configurations.
- Ideal for steam, gas, hydro turbines.
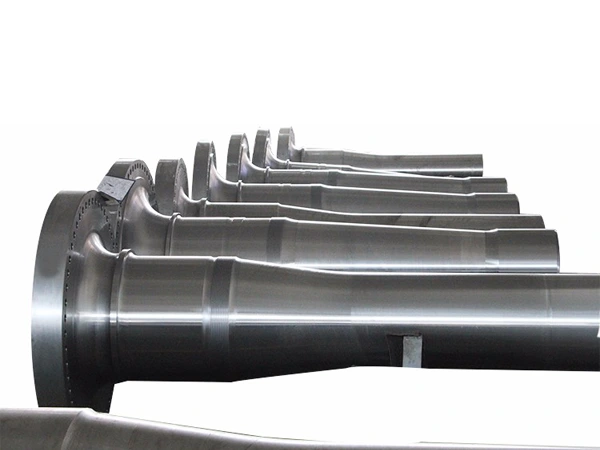
- Materials include carbon, alloy, stainless, nickel steel.
- Produced with dimensional uniformity and precision.
- Tolerance within ±0.01mm, Ra ≤ 0.4.
- Fully inspected with 100% UT testing.
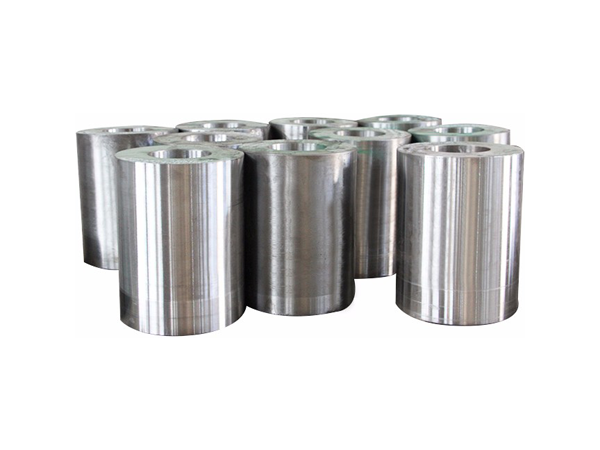
- Carbon, alloy, stainless, nickel alloys available.
- High durability and wear resistance.
- Ideal for various industrial applications.
- Secure packaging in wooden or iron cases.
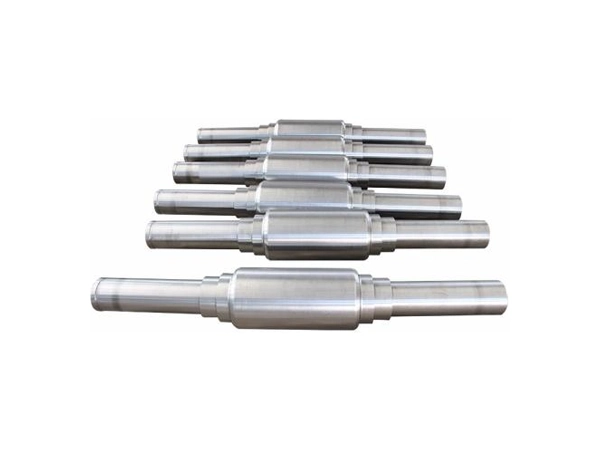
- Chemical elements strictly inspected pre-forging.
- Includes step shafts, main, crank shafts.
- Full service from forging to machining.
- Each shaft tested with sample bar.
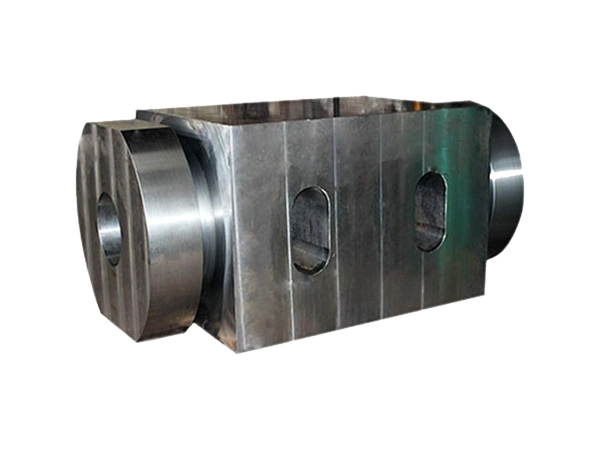
- Forged into various complex part shapes.
- Handles water, oil, steam, liquefied gas.
- Manufactured to ASTM, BS, EN, JIS.
- ISO-certified for consistent global quality.