Custom Hot Forging Service
- We choose the most suitable hot forging method to optimize performance and reduce costs by up to 30% through improved material efficiency and minimized machining.
- Our product range includes pipe heads, valve parts, gears, shafts, and rings, all with a near-100% qualification rate. Finishing and assembly services are also available.
- 30 Years of Industry Experience
- 20+ Forging Machines
- Various Forging Processes
- 100+ Metal Materials Available
- Support Semi-finished Customization
- Dimensional Accuracy: ±0.5 mm to ±3.0 mm
Our Forging Process
From raw material to final delivery, we maintain rigorous control at every stage to ensure durability, performance, and consistency.
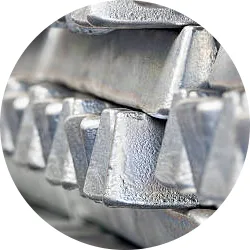
Raw Material Inspection
01
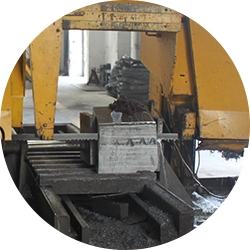
Cutting
02
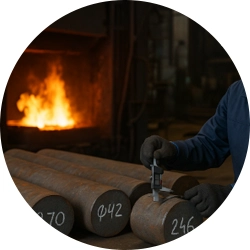
Pre-Forging Inspection
03
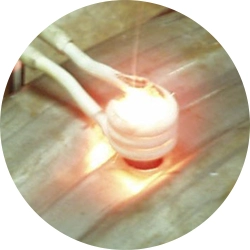
Preheating
04
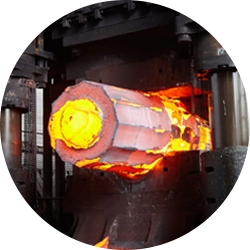
Forging
05
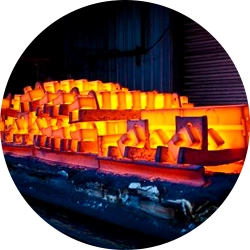
Heat Treatment
06
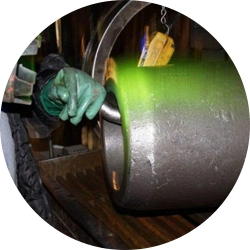
Post-forging Inspection
07
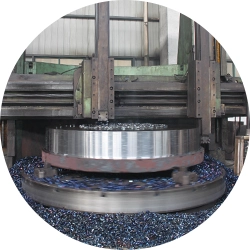
Rough Machining
08
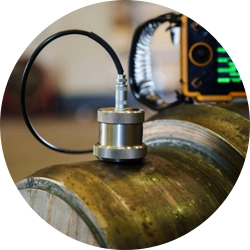
NDT & Dimensional Inspection
09
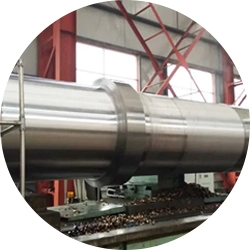
Finishing
10
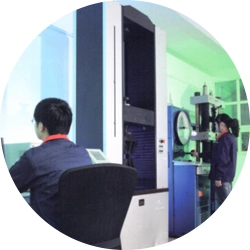
Final Inspection
11
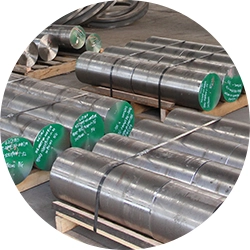
Packaging
12
Based on Die Type
Open-die, closed-die, and semi-closed hot forging all have unique benefits in terms of shape, volume, and accuracy.
- Compresses metal between flat dies without full enclosure.
- Suitable for large, simple, custom-shaped parts.
- Provides excellent grain flow and mechanical strength.
- Utilized in the energy, heavy industrial, and aerospace sectors.
- Metal completely enclosed in precision-shaped impression dies.
- Ideal for accurate, complex parts in large volumes.
- Reduces machining with high dimensional consistency.
- Used in automotive, aerospace, and tool manufacturing.
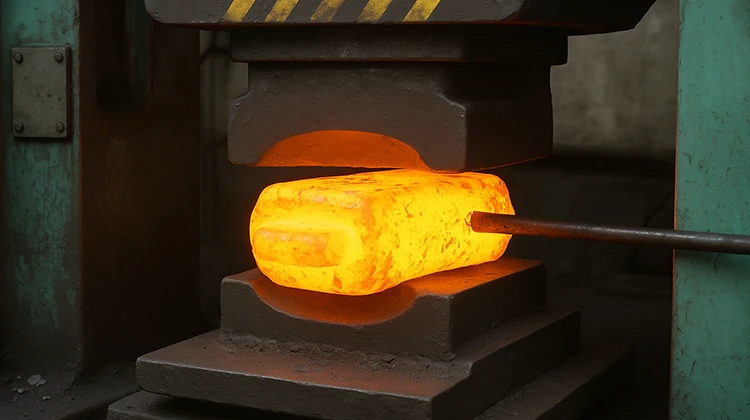
Semi-Closed Die Forging
- Dies partially enclose metal with slight flash escape.
- Balances precision, material use, and production efficiency.
- Suitable for medium-complexity, moderate precision components.
- Applied in hardware, machinery, and mid-volume production.
Based on Equipment Used
In order to precisely and robustly form metal, hot forging techniques employ a variety of equipment, such as hammers, presses, rolls, and rings.
- Dies partially enclose metal with slight flash escape.
- Balances precision, material use, and production efficiency.
- Suitable for medium-complexity, moderate precision components.
- Applied in hardware, machinery, and mid-volume production.
- Increases diameter by compressing heated metal along its axis.
- Commonly used to produce bolts, shafts, and fasteners.
- Performed using vertical or horizontal forging presses.
- Aligns grain flow for superior mechanical strength.
- Shaped by passing heated metal through rotating cylindrical rolls.
- Ideal for tapering, stepping, or contouring shaft-like parts.
- Used as preform for further forging or machining.
- Ensures uniform cross-section and minimizes material waste.
- Shaped by expanding a punched, heated billet into a ring.
- Used for bearings, flanges, and large aerospace rings.
- Provides improved grain flow and dimensional accuracy.
- Enables control of thickness and ring diameter.
Based on Forging Motion
Axial, radial, and orbital hot forging techniques are all motion-based and optimize force direction for accurate, effective metal deformation.
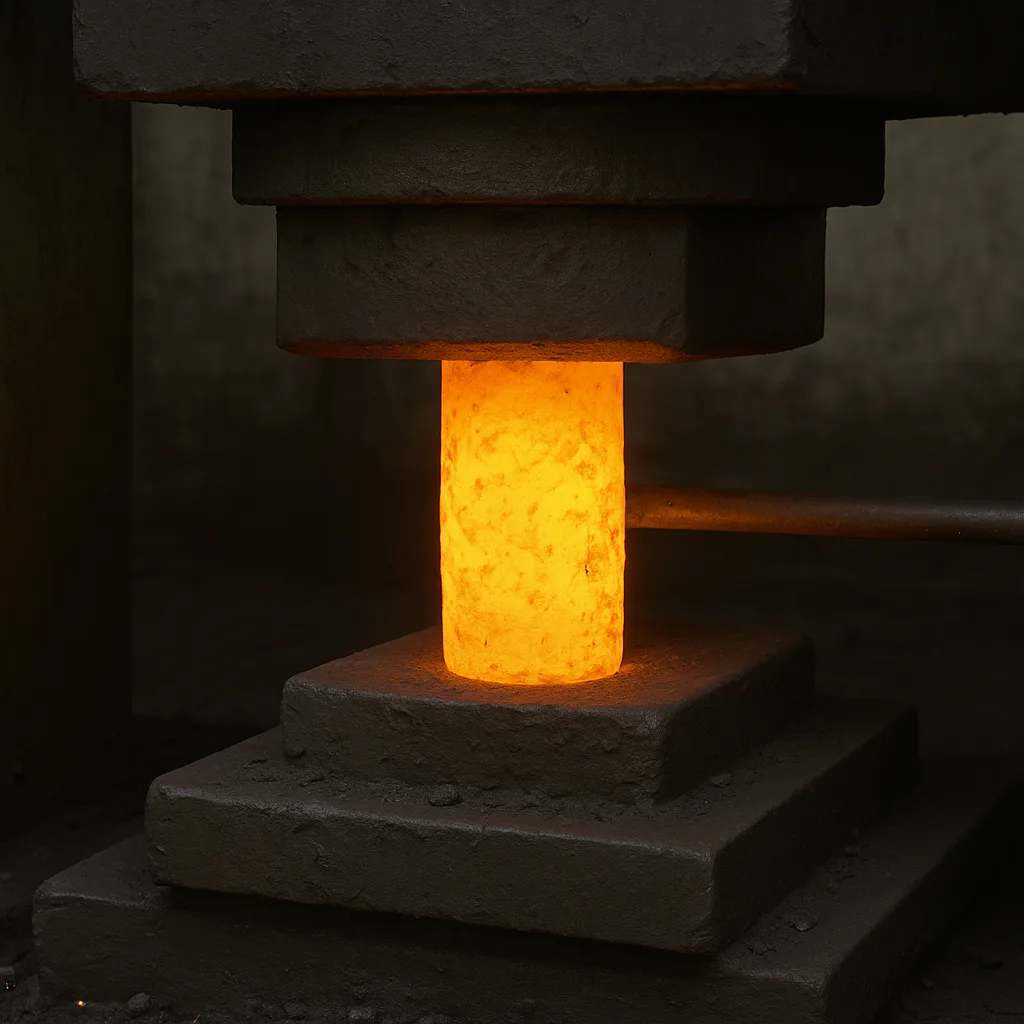
Axial Forging
- Applies force along metal’s axis to shape it.
- Used for shafts, rods, and elongated cylindrical components.
- Enhances grain alignment for improved mechanical properties.
- Common in open-die or closed-die forging processes.
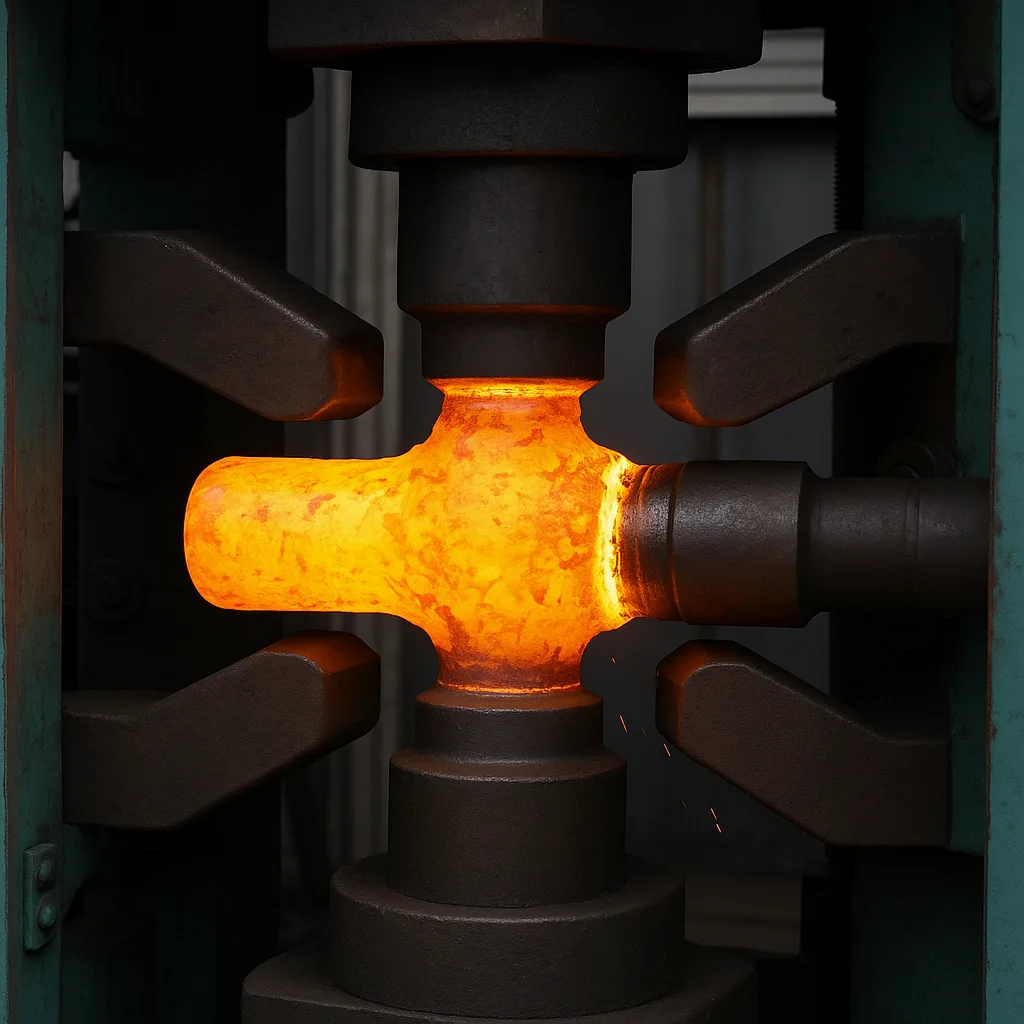
Radial Forging
- Force applied inward from multiple radial directions.
- Ideal for hollow parts, tubes, and stepped shafts.
- Ensures uniform cross-sectional deformation and high accuracy.
- Increases material utilization and reduces final machining.
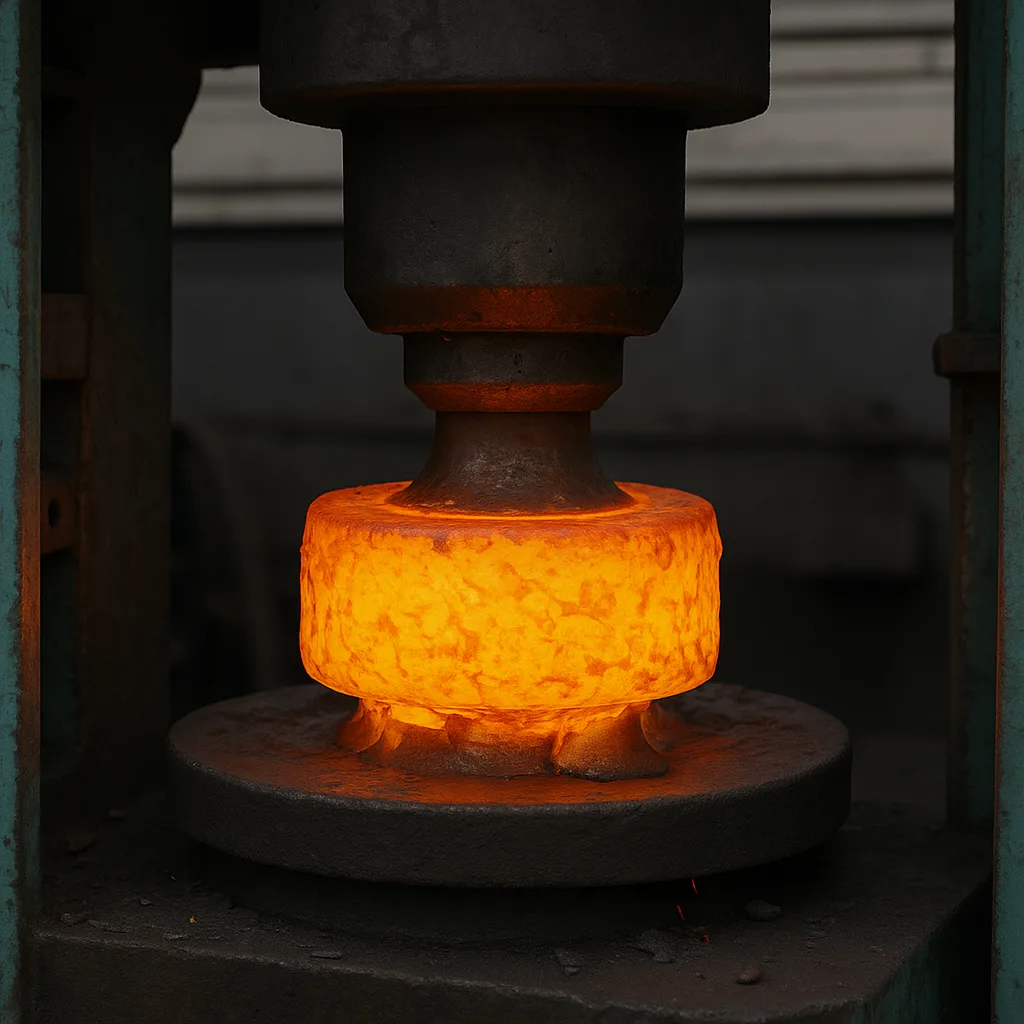
Orbital Forging
- Rotating die orbits while pressing against workpiece gradually.
- Reduces load, enables efficient shaping of complex parts.
- Suitable for gears, bearing races, and rings.
- Enhances finish and improves metal flow characteristics.
Materials We Forge
We work with a wide variety of forging-grade metals to meet industry-specific mechanical, thermal, and structural performance requirements.
Material Category | Material Grade / Model | Typical Applications |
Carbon Steel | AISI 1010, 1020, 1045, 1050 | Shafts, flanges, brackets, mechanical parts |
Alloy Steel | 4130, 4140, 4340, 8620 | Gears, axles, connecting rods, spindles |
Stainless Steel | 304, 316, 410, 420, 431 | Food equipment, chemical valves, pump housings |
Tool Steel | H13, D2, A2, O1, S7 | Dies, punches, cutting tools, molds |
Aluminum Alloys | 6061, 6082, 7075, 2011 | Aerospace structures, automotive fittings, electronic enclosures |
Copper Alloys | C11000 (Copper), C36000 (Brass), C95500 (Bronze) | Electrical parts, fittings, marine and architectural hardware |
Titanium Alloys | Grade 2 (CP), Grade 5 (Ti-6Al-4V) | Aerospace fasteners, medical implants, racing components |
Nickel Alloys | Inconel 718, Monel 400, Hastelloy C276 | Jet engines, turbines, chemical reactors |
Magnesium Alloys | AZ31B, AZ61A, ZK60 | Aerospace frames, auto parts, camera housings |
Superalloys | Rene 41, Waspaloy, Udimet 720 | Turbine blades, exhaust components, space propulsion |
Post-forging Processes
To guarantee performance, accuracy, durability, and constant quality assurance, post-forging procedures include heat treatment, CNC machining, surface finishing, and testing.
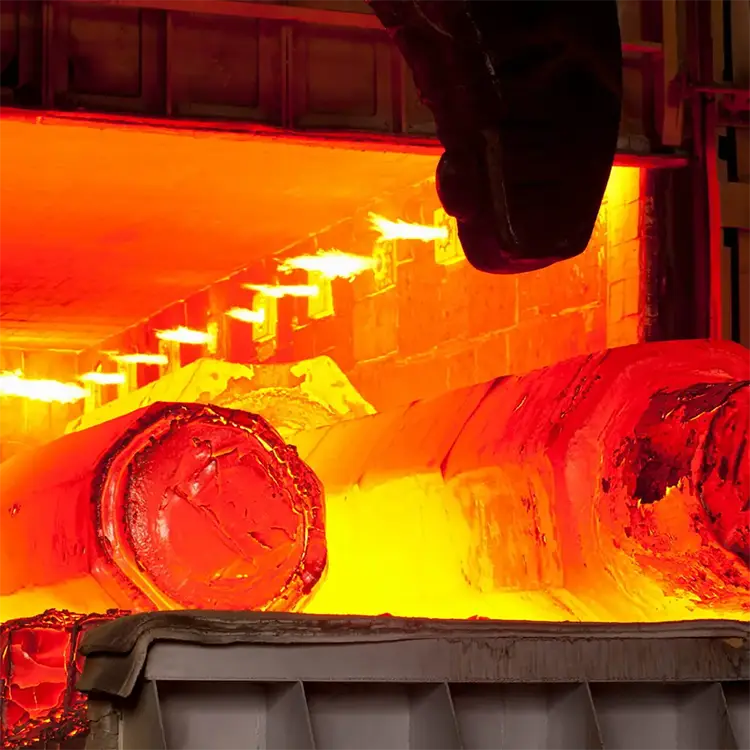
Heat Treatment
Uses advanced computer-controlled furnaces and imported quenching medium to ensure uniform temperature, high precision, and improved product mechanical properties.
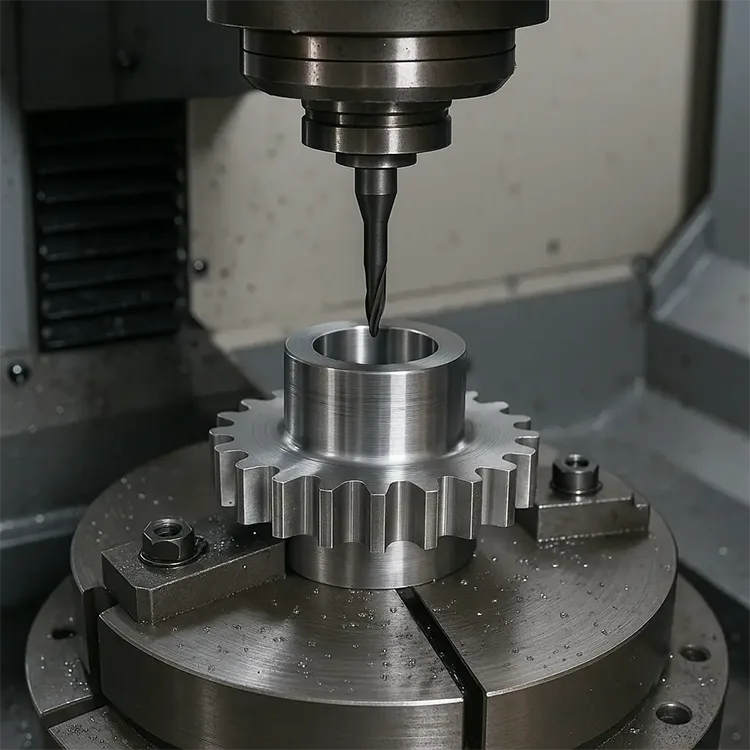
CNC Machining
Equipped with CNC machines bearing up to 70 tons, including gantry and deep hole boring for diverse precision machining requirements.

Surface Finishing
Applies shot blasting, polishing, coating, and passivation techniques to enhance corrosion resistance, improve surface quality, and meet customer specifications.
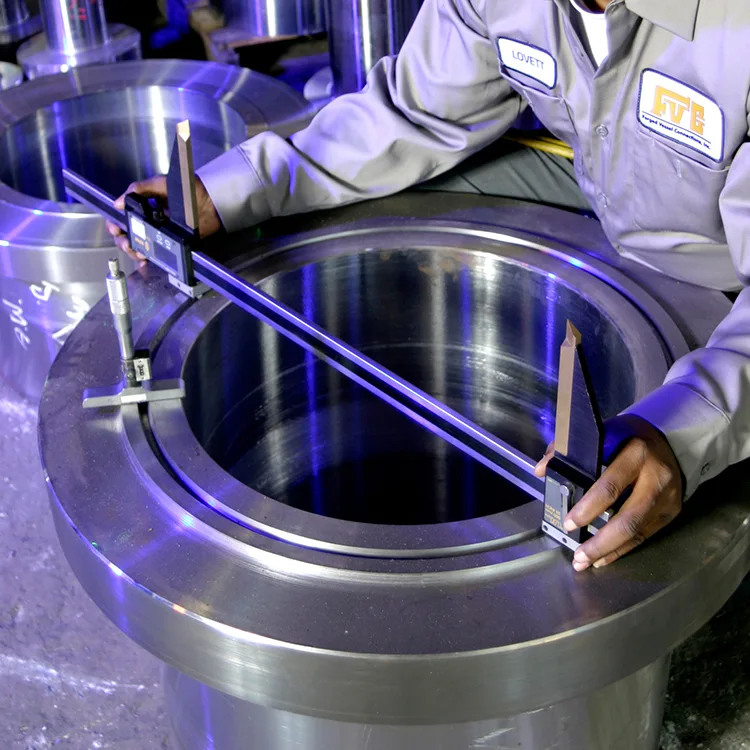
Inspection & Testing
Performs dimensional checks, hardness testing, and uses SPECTRO spectrometer, metallographic analyzer, ultrasonic and magnetic flaw detectors to ensure strict quality.
Precision Tolerances in Hot Forging
Parameter | Tolerance |
Dimensional Accuracy | ±0.5 mm to ±3.0 mm |
Flatness | 0.25 mm per 100 mm length |
Roundness | ±0.5% of diameter |
Straightness | 1.0 mm per 100 mm length |
Surface Finish | Ra 3.2 to 12.5 µm |
Weight Deviation | ±2% of nominal weight |
Angularity | ±1.0° |
Feature Alignment | ±0.2 mm per 100 mm |
Thickness Variation | ±5% of nominal thickness |
Edge Radius | ±0.2 mm to ±1.0 mm |
Bore Diameter | ±0.1 mm to ±0.5 mm |
Fillet Radius | ±0.2 mm |
Draft Angle | 3° to 5° |
Concentricity | ±0.05 mm to ±0.2 mm |
Parallelism | ±0.1 mm per 100 mm |
Depth Accuracy | ±0.3 mm to ±1.0 mm |
Thermal Distortion | ±0.1% of overall dimensions |
Our Projects
Forged Shafts
Forged Cylinder Sleeve
Forged Discs or Forged Hubs
Forged Gear
Complex Forged Shapes
Special Steel Grades
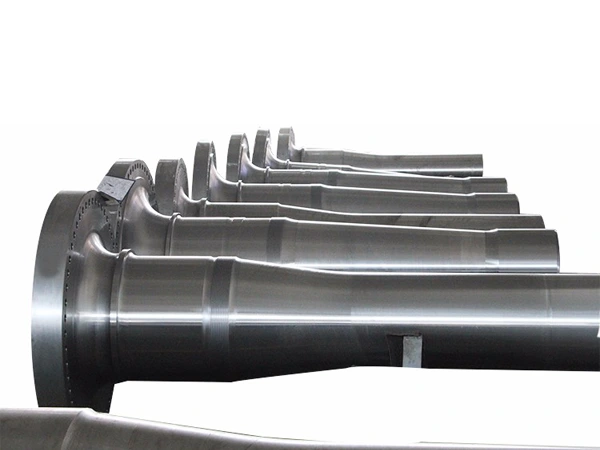
- High dimensional uniformity.
- Custom manufacturing based on drawings.
- Tolerance within ±0.01mm, Ra ≤ 0.4.
- Made for wind turbine motor systems.
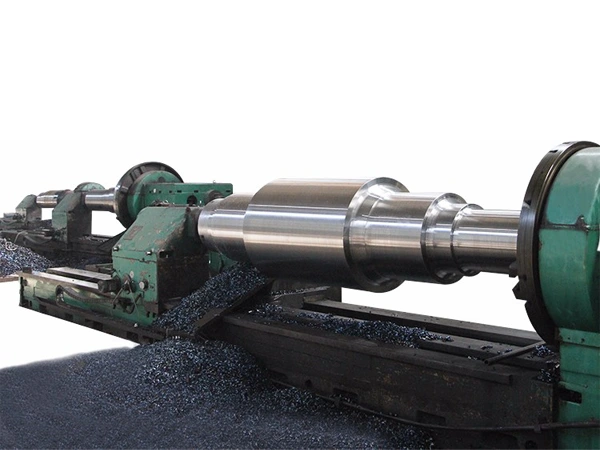
- Wide material options including nickel alloys.
- Shapes include flanged, step shafts, spindles.
- Supports heavy machinery and metalworking.
- Ideal for energy and power generation.
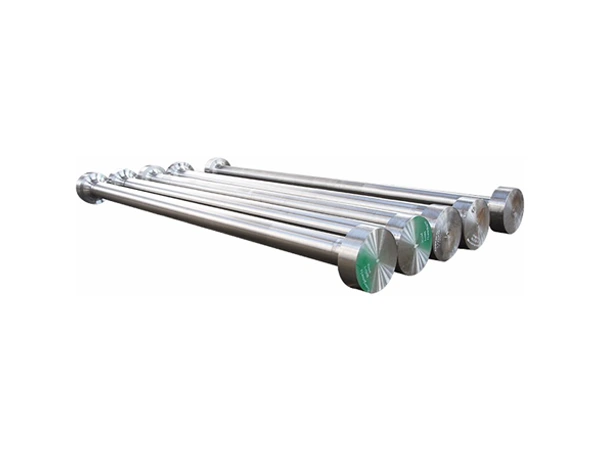
- Made from first-grade ingot steel.
- Generator and rotor shafts available.
- Includes turning, milling, drilling, boring.
- FOB, CIF, DDP delivery options.
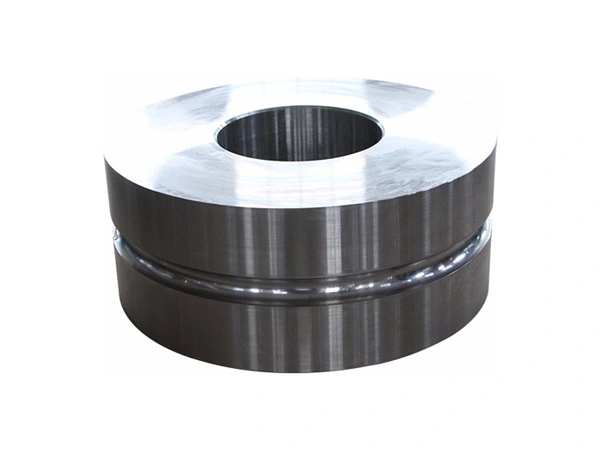
- Material options include alloy and steel.
- Includes forging, heat treatment, machining.
- Finishes include nickel, chrome, plain, polished.
- Suitable for multiple industrial applications.
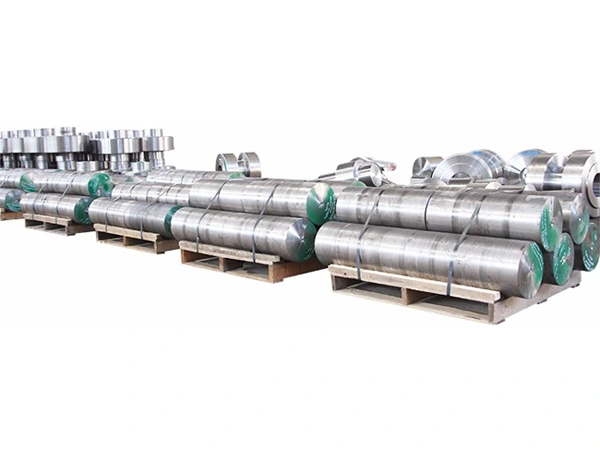
- Available in multiple steel alloy grades.
- Ideal for bushings and casing covers.
- Suitable for building and machinery use.
- Certified with ISO9001, PED, SGS.
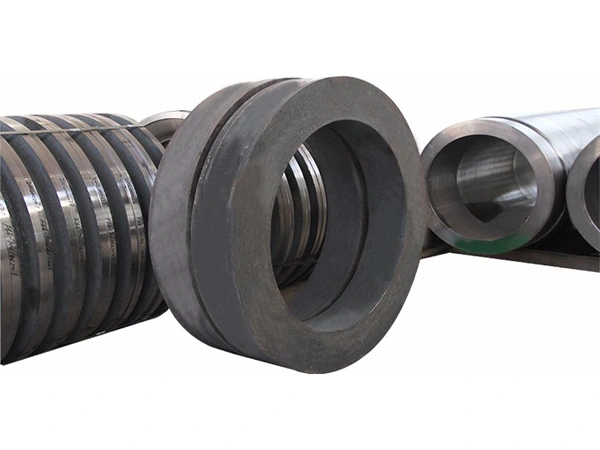
- Carbon, alloy, stainless, nickel alloys available.
- Durable under high mechanical stress.
- Suitable for railway and crane equipment.
- Applied in automotive and mining industries.
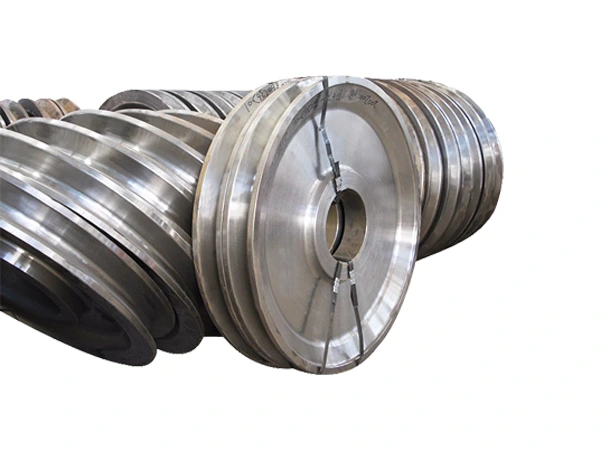
- Made from high-grade steel alloys.
- Supports open and die forging methods.
- CNC turning, milling, drilling supported.
- Ideal for automotive, aerospace, and medical.
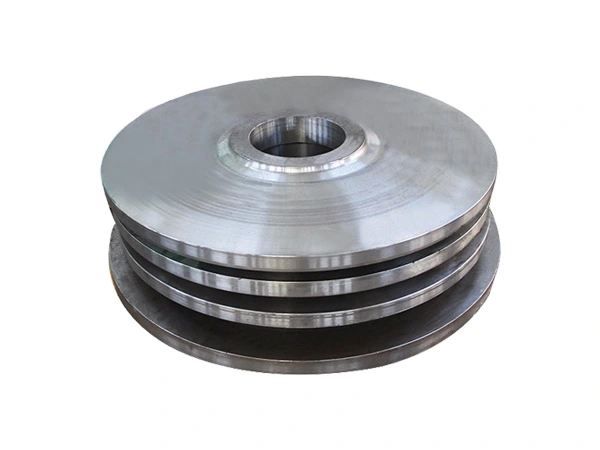
- Wide range of material options.
- Good thermal and mechanical properties.
- Nonmagnetic and completely non-toxic.
- Suitable for vessels and infrastructure use.
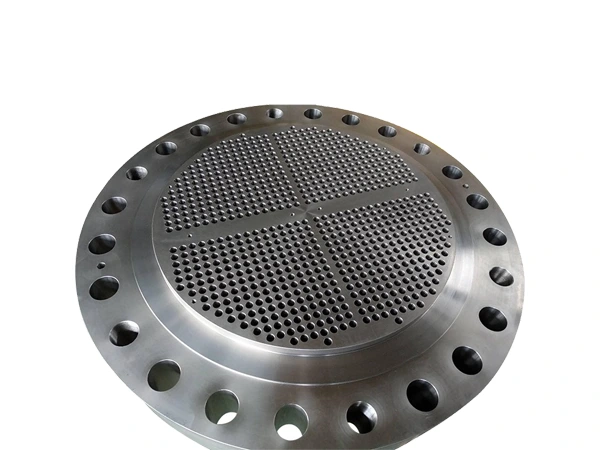
- Forged specifically for heat exchanger systems.
- Suitable for boilers and pressure vessels.
- Complex hole shapes easily fabricated.
- Drilled and machined per customer request.
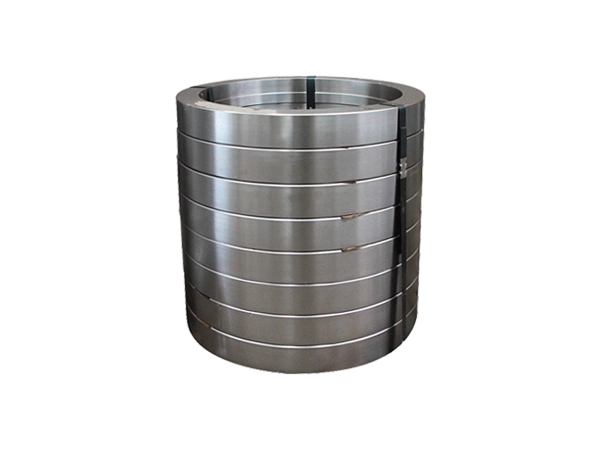
- Material flexibility for diverse applications.
- Spur, helical, bevel gear shapes supported.
- Supports low-volume production needs.
- Certified by ISO9001, PED, SGS.
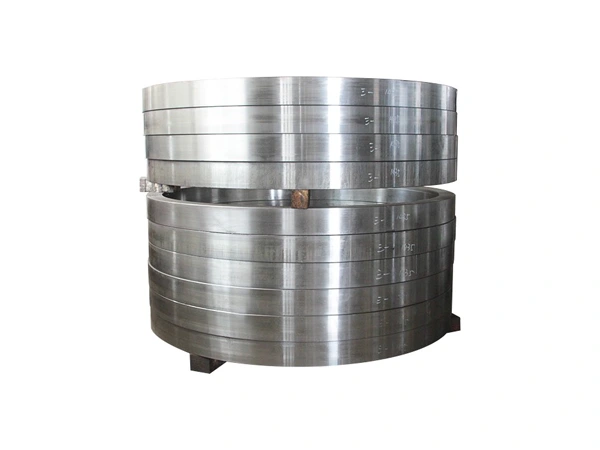
- Carbon, alloy, stainless, nickel steels applied.
- Suit various gear types.
- Enhances strength through open die forging.
- Supports small batch and custom orders.
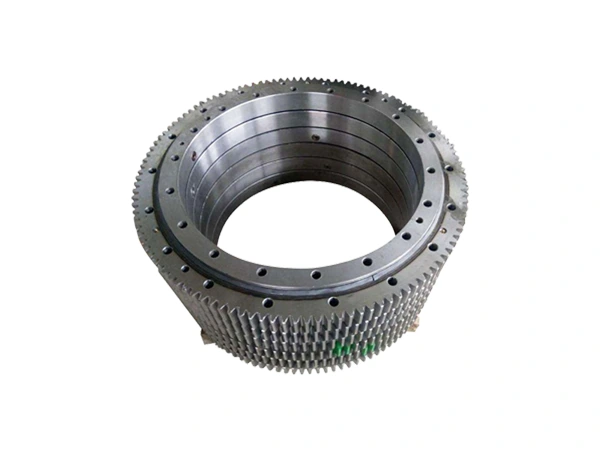
- Equipped with hammers and hydraulic presses.
- Supports annealing, normalizing, hardening processes.
- Heat treatment tailored to client needs.
- Rough or final machining available.
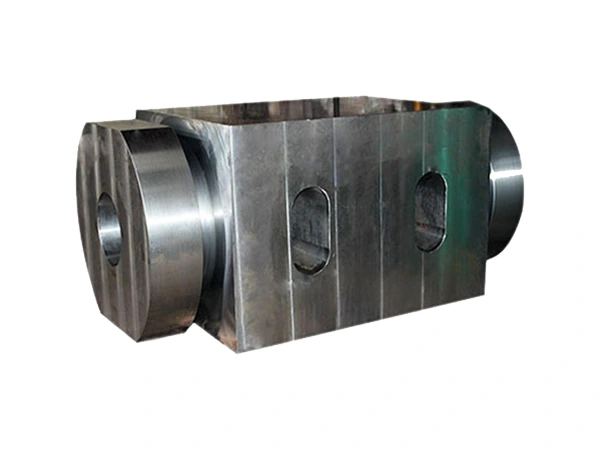
- Forged into various complex part shapes.
- Handles water, oil, steam, liquefied gas.
- Manufactured to ASTM, BS, EN, JIS.
- ISO-certified for consistent global quality.
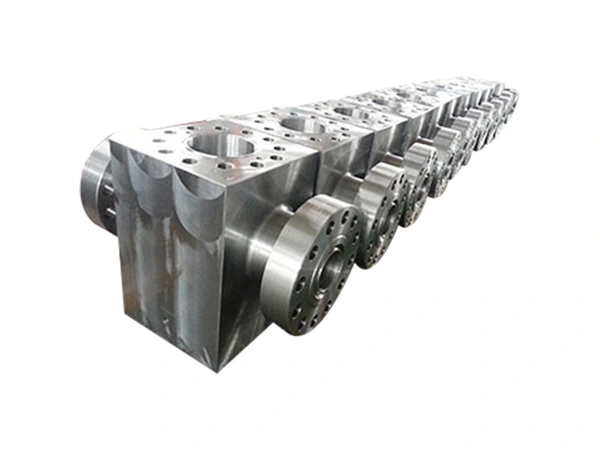
- Carbon and alloy steel material options.
- Reliable sealing and high pressure resistance.
- Suitable for marine and oil applications.
- OEM and customized service available.
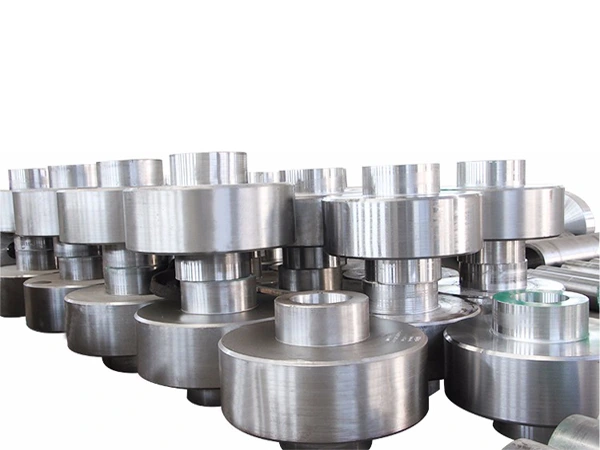
- Supports customer’s own final processing.
- Enables flexible downstream machining options.
- Provides rough turning and pre-machining.
- Used in machinery and metalworking industries.
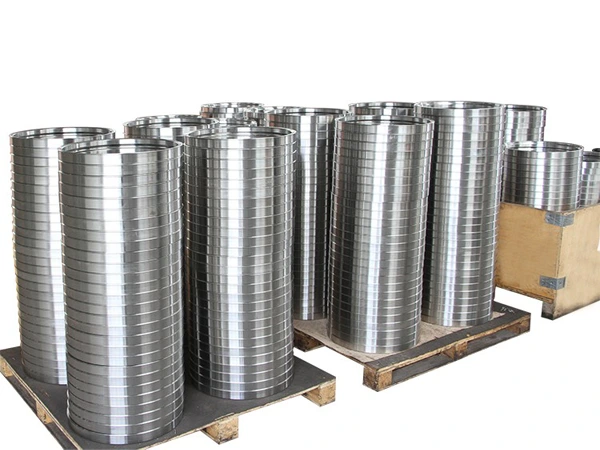
- High strength and excellent toughness.
- Good corrosion resistance in use.
- Allows cost-effective and simplified fabrication.
- Suitable for diverse industrial design needs.
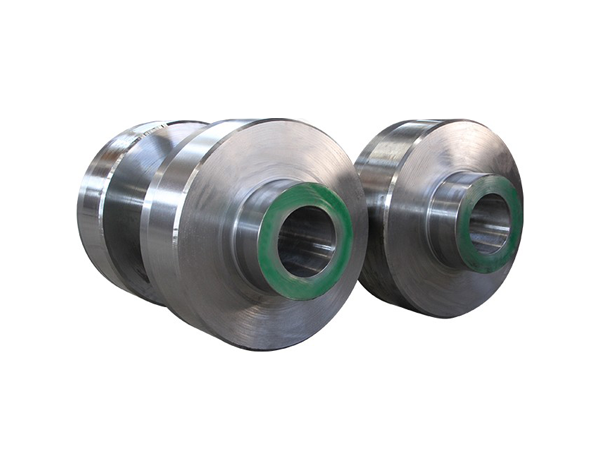
- High-quality 42CrMo4V ingot steel used.
- Excellent strength and toughness properties.
- Full EAF + LF + VD process.
- Suitable for various industrial applications.
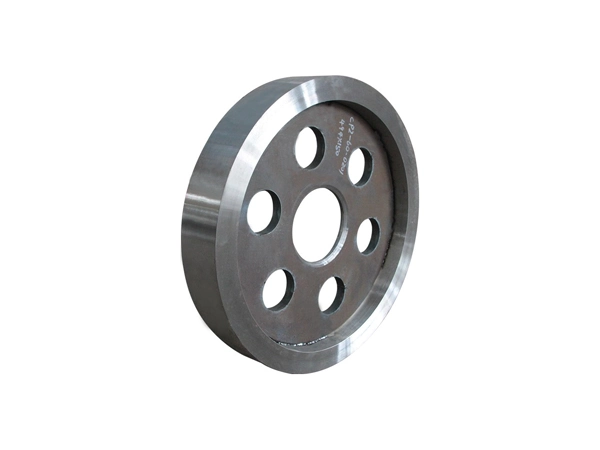
- Smooth cold-rolled surface with gloss.
- Excellent strength at high temperatures.
- Good work-hardening during processing.
- Suitable for structural and construction use.
Application
Our hot forging solution serves the mining, energy, maritime, and chemical sectors, producing robust, wear-resistant parts for harsh, high-stress operations.
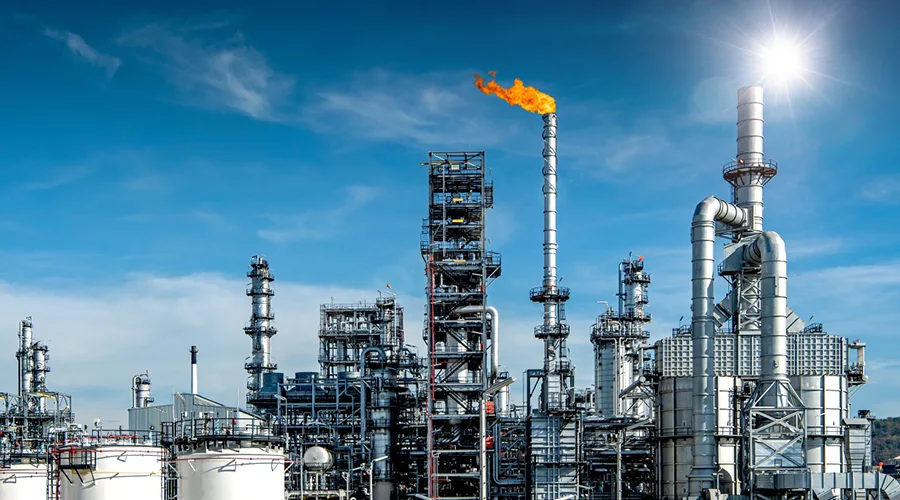
Chemical and Petroleum Industries
Forged components withstand high pressure and corrosion, ideal for valves, flanges, fittings, and reactors in harsh chemical environments.
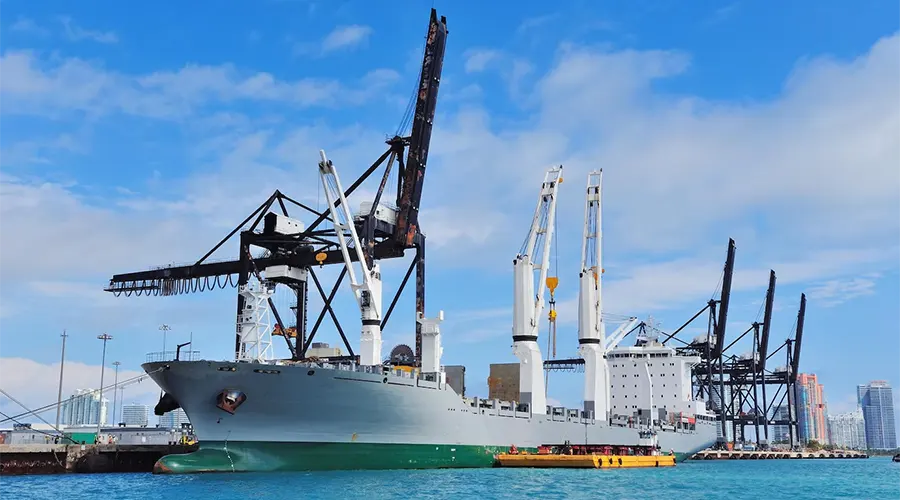
Shipbuilding
Hot forged parts ensure strength and durability for propeller shafts, rudder systems, and structural elements in marine applications.

Power Generation & Energy
Used in turbines, generators, and pressure vessels to deliver high strength, temperature resistance, and long-term operational reliability.
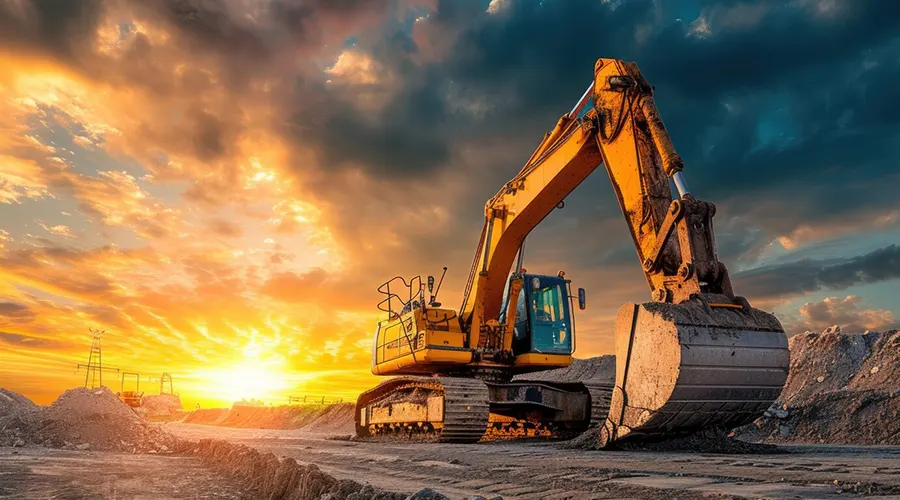
General Mechanics
Provides reliable forged parts for mechanical systems, ensuring high wear resistance, strength, and dimensional stability under dynamic load conditions.
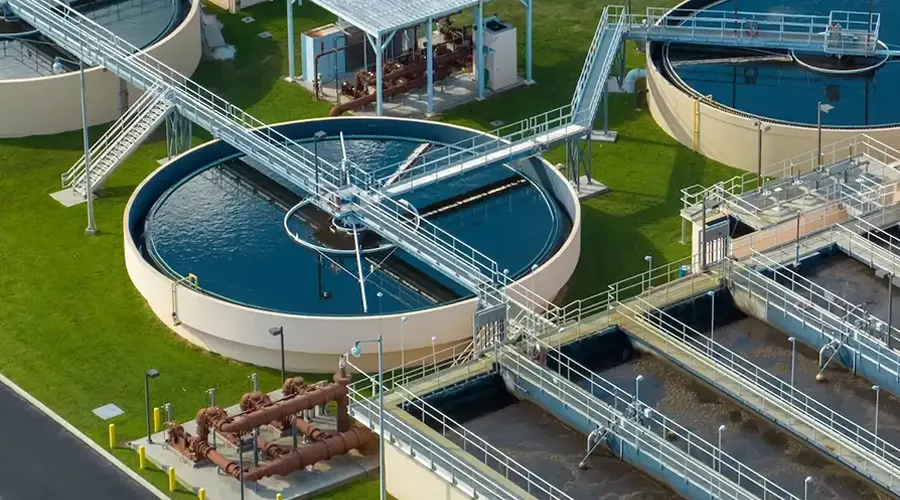
Environmental Technology
Supports wastewater, filtration, and recycling systems with corrosion-resistant forged components meeting environmental and durability standards.
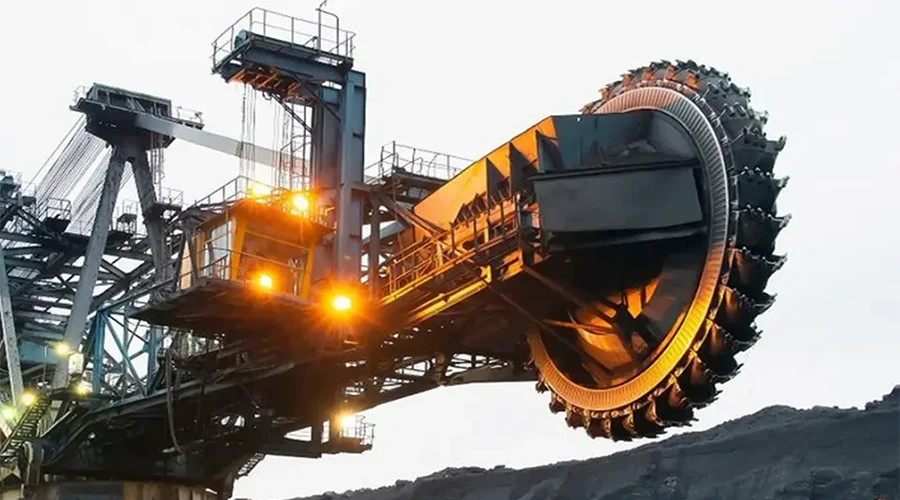
Mining Equipment
Delivers robust forged parts for crushers, excavators, and drilling systems operating in extreme, abrasive, and heavy-duty mining environments.